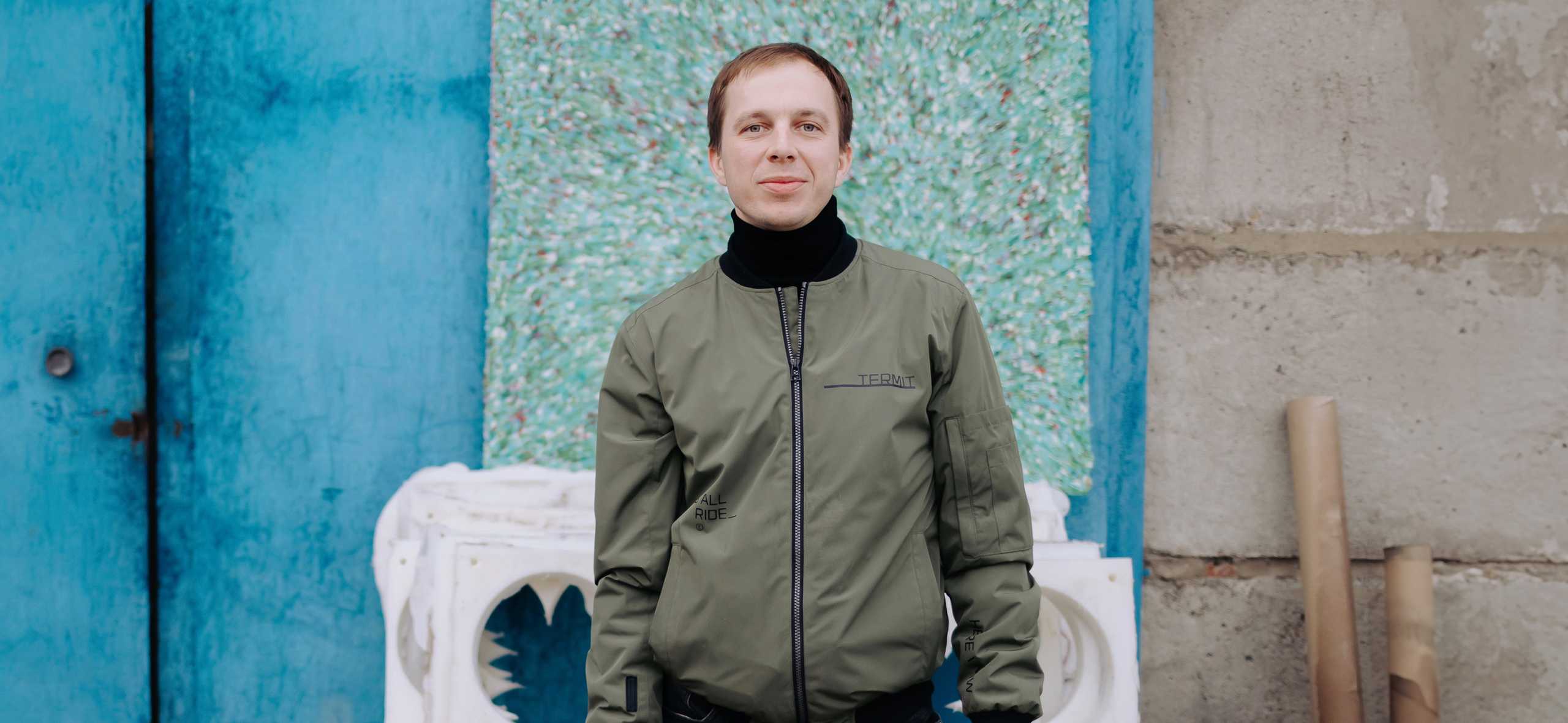
«Могу заработать 200 000 ₽ в день»: как я произвожу станки для переработки пластика
Идея бизнеса появилась в свадебном путешествии в 2018 году.
Мы с женой Настей уехали на месяц в Турцию, Израиль и Таиланд. В России раздельный сбор мусора тогда еще был редкостью, в этих странах на улицах стояли контейнеры для стекла, пластика и бумаги. Все чисто, плюс люди и компании зарабатывают на сборе вторсырья.
Дома я нашел чертежи измельчителя пластиковых крышек и собрал его в гараже. Потом сделал инжектор, чтобы плавить пластик и придавать ему новую форму. С этими устройствами стал участвовать в экологических фестивалях и выставках.
Сейчас мы производим и продаем восемь видов станков, делаем на заказ пластиковые предметы интерьера и сувениры, ездим с мастер-классами по стране. В 2024 году оборот компании превысит 20 млн рублей, а мой доход — от 300 000 до 500 000 ₽ в месяц. Расскажу, как мне это удалось.
Как я сделал первый измельчитель
Идея открыть компанию по переработке пластика появилась на обратном пути. Дома я сделал небольшую презентацию, чтобы поделиться задумкой с друзьями. Так появилось название Infinity Plastic и логотип в виде перевернутой восьмерки — символа бесконечности. Ведь пластик можно бесконечно превращать в новые вещи.
Я собрал друзей и показал им слайды с фотографиями из поездки. Там были турецкие «умные урны», где мусор прессуется под землей, и он не разлагается на жаре, не привлекает животных. Еще урны для раздельного сбора на пляжах Таиланда — это разноцветные обручи с мусорными пакетами для сортировки отходов. Было и про то, что в Израиле люди сдают бутылки в супермаркеты в обмен на деньги или скидки.
Друзья поддержали идею. Я начал искать оборудование на российских сайтах и наткнулся только на крупные промышленные машины. Запускать дорогое производство я не был готов: в переработке не разбирался, да и вкладываться серьезно не хотел.
Случайно я наткнулся на проект нидерландского дизайнера Дейва Хаккенса — Precious Plastic. Это сообщество экоэнтузиастов, которые делятся знаниями о переработке: выкладывают чертежи станков и пресс-форм для отливки изделий из переработанного пластика.
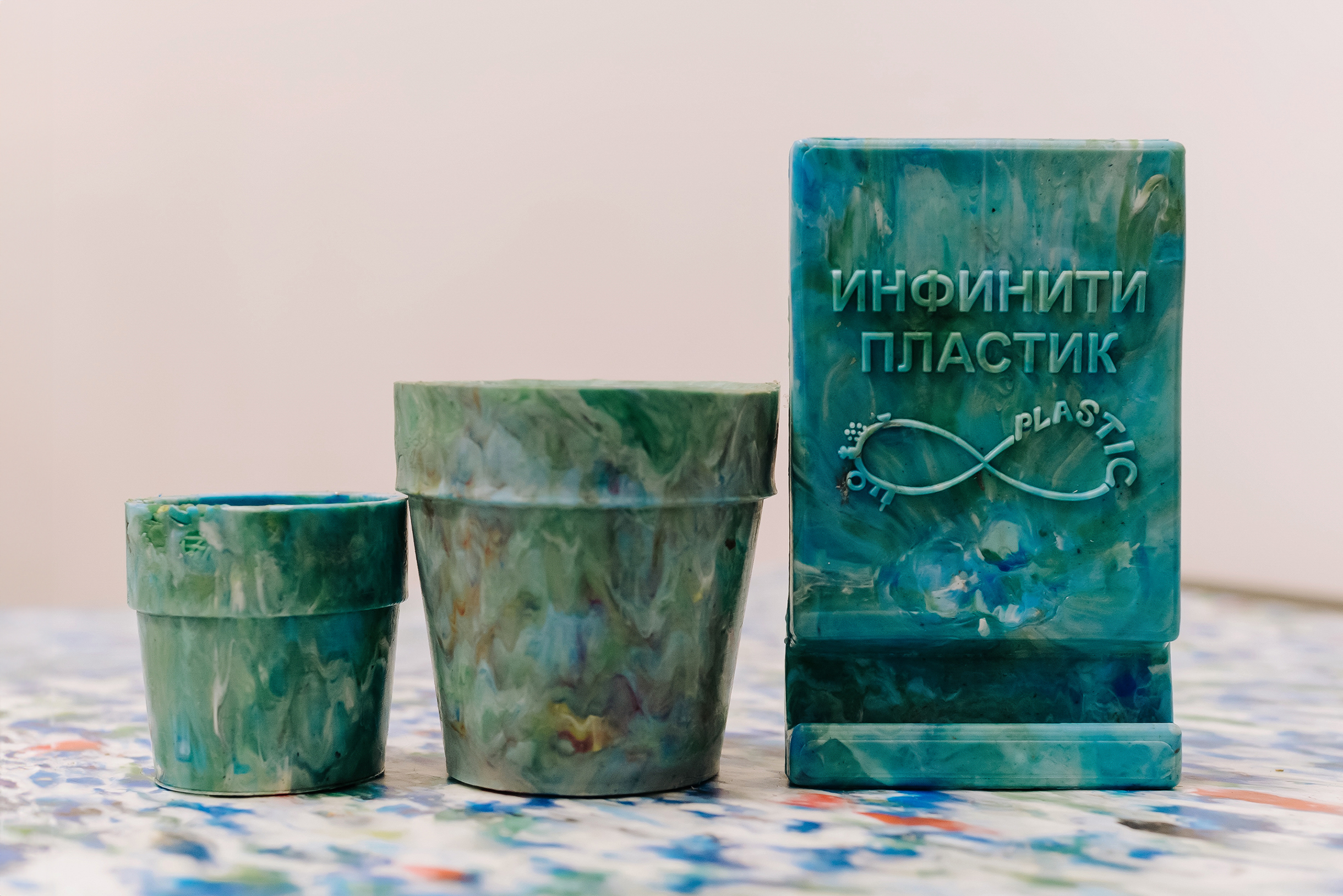
Я скачал чертежи, разобрался по видео, как собрать измельчитель , и начал адаптировать чертежи под российские размеры и материалы. Например, перевел дюймы в миллиметры.
На тот момент я уже пять лет поставлял оборудование на заводы — это до сих пор мой основной бизнес. Я знал, как устроен технологический процесс, где взять нужное железо и найти специалистов для изготовления деталей.
Для переработки первым делом нужен шредер — он превращает твердый пластик в крошку. Затем эту крошку плавят и заливают в пресс-формы. Шредер я собрал в мастерской у родителей. Требовались лист нержавейки, мощный электродвигатель и стальные ножи. За металлом я поехал на металлоприемку: производства сдают туда обрезки листов, из которых вырезали какие-то детали. Обычно их отправляют на переплавку, но любой может купить эти остатки. Это выгодно всем.
Когда друг узнал, что я собираю измельчитель, предложил мне электродвигатель, который годами пылился у него в гараже. По характеристикам он мне подошел, и я купил его за 2000 ₽. Установил двигатель на железную раму, которую сварил из того, что нашел в мастерской.
Пока я возился с измельчителем в мастерской, дома мы копили чистое вторсырье: крышки, бутылки и другой твердый пластик с нужными маркировками. Вот какие годятся для переработки: «ПЭТ 1» , «ПНД 2» , «ПВД 4» и «ПП 5» . Эти виды пластика не выделяют вредных веществ при нагревании.
Еще бывает пластик с маркировкой «ПВХ 3» , «ПС 6» , 7 и другие. «ПВХ 3» может содержать вредные вещества, например ртуть, а «ПС 6» при нагревании выделяет ядовитый стирол. Маркировка 7 означает, что в составе может быть намешано что угодно.
Первый шредер я собрал за два месяца. Можно было быстрее, но я занимался этим после работы, без особых дедлайнов. Мы измельчили накопленный пластик в крошку. Чтобы сделать из нее что-то новое, нужен был инжектор — он нагревает, плавит пластик и выдавливает его в форму. Я нашел чертежи инжектора, собрал станок из того, что было в мастерской, и нагревателя с «Алиэкспресса». Инжектор заработал, и у меня появились первые плитки из переработанного пластика.
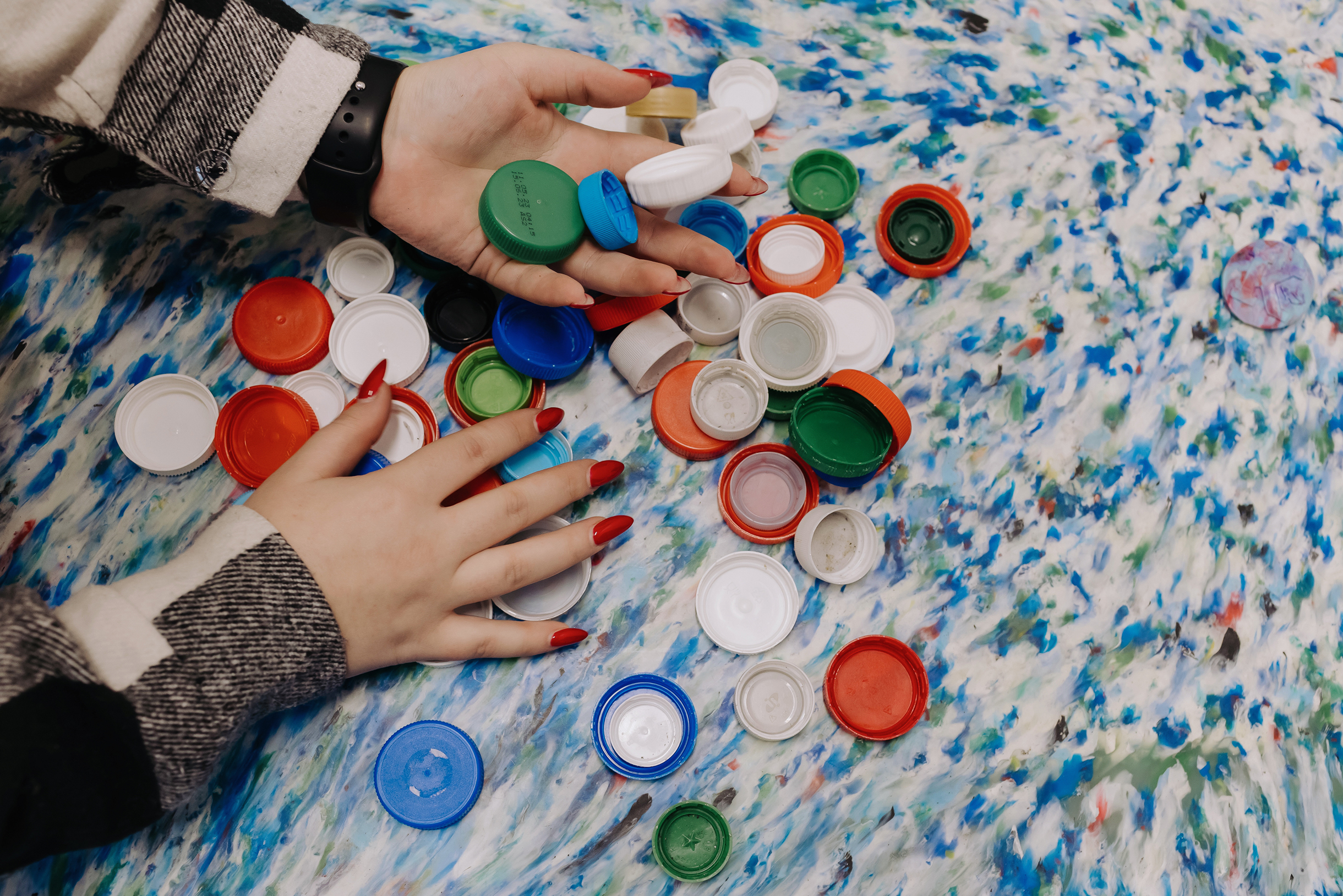
Первые продукты разобрали сразу же
Я решил немного поэкспериментировать и проверить, сколько раз можно переплавлять один и тот же пластик без потери качества. Сделал простую квадратную форму и переплавлял крышки от бутылок в эти плитки. Потом снова измельчал и переплавлял их.
Оказалось, пластик выдерживает восемь-десять циклов. Плитки после одиннадцатого цикла становились хрупкими, плохо выдерживали ультрафиолет и холод. Но если добавлять 20% такой «уставшей» стружки к 80% пластика, переработанного только один раз, снова получается крепкий материал, который не отличается от изделия из свежей крошки.
Я убедился, что пластик можно использовать снова и снова — нужно только собирать и мыть его, а не выбрасывать на свалку. Из переработанного пластика делают синтепон, синтетические ткани для одежды и обуви, ящики для фруктов, канцтовары, уличную мебель, даже рамы для велосипедов. Я начал думать, с чего можно начать и как на этом заработать.
Мой друг, графический дизайнер Андрей Воробьев, рассказал, что будет продавать одежду на фестивале в Нижегородской области, и предложил мне тоже занять место на прилавке. Мы решили сделать значки и брелоки, Андрей разработал для них пресс-формы. За месяц до фестиваля мы сделали 300 штук, купили кольца и булавки и собрали все вручную.
В это же время я купил термопресс, который в типографии используют для переноса изображений на ткань. Мы нашли ему другое применение: клали в пресс пластиковые пакеты в несколько слоев и сплавляли их. Получалось плотное пластиковое полотно, из которого можно было делать косметички, сумки, обложки для документов.
За неделю до фестиваля мы собрали у друзей и знакомых чистые пакеты. Сделали из них пластиковые полотна, скачали лекала поясных сумок в интернете, нашли швею и сделали 25 штук.
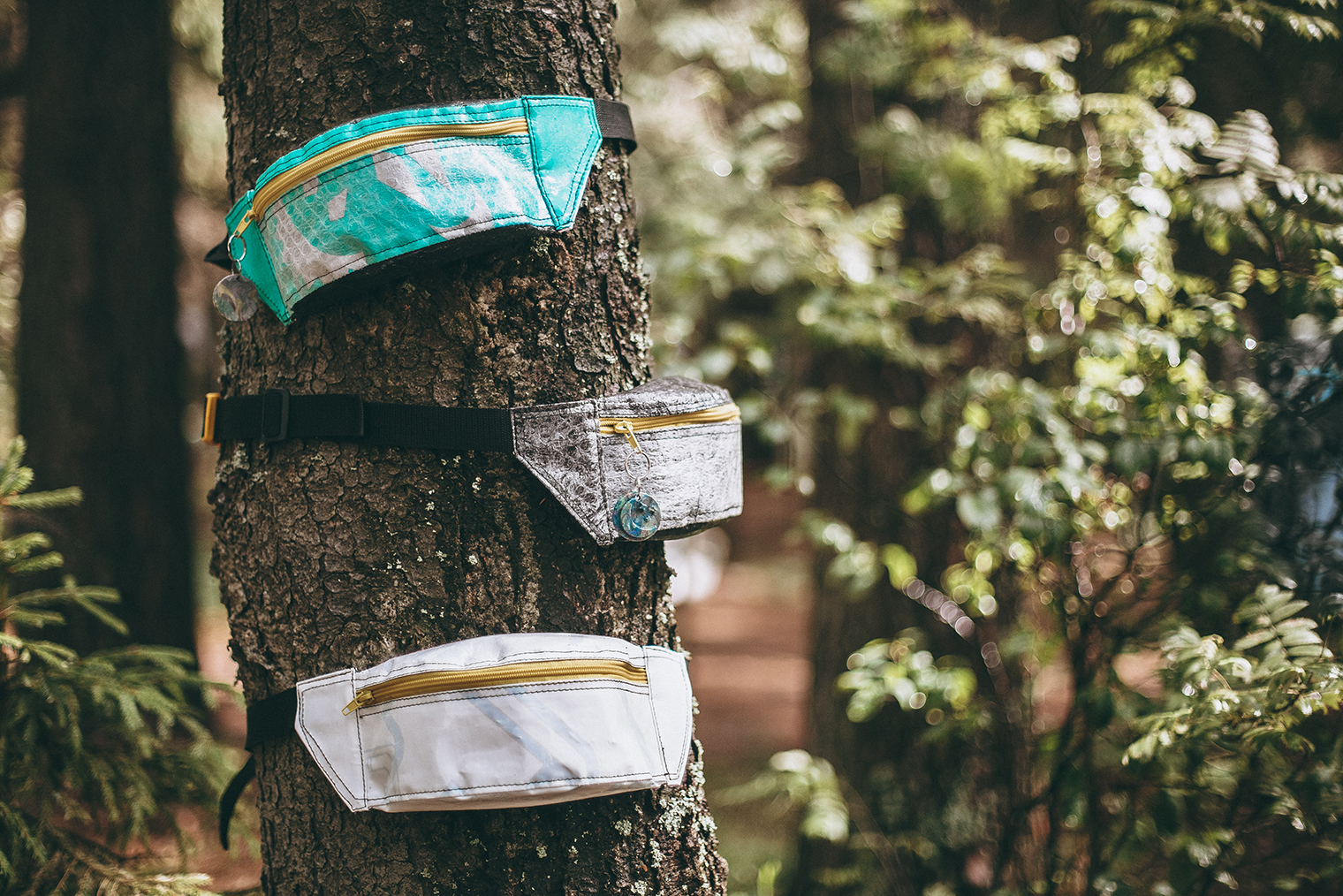
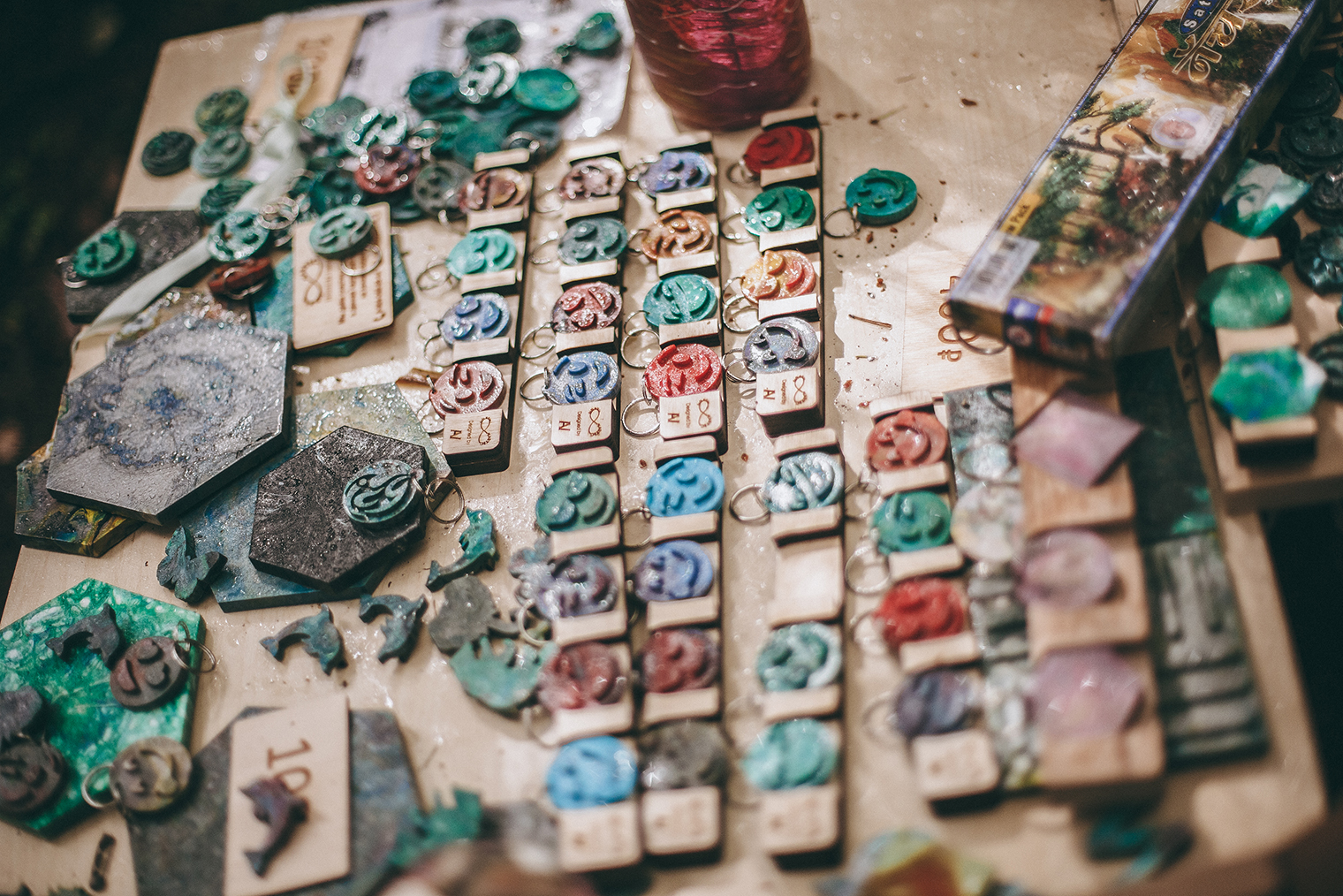
На фестивале мы повесили картонку с надписью: «Infinity Plastic — товары из переработанного пластика». В первый день продавали значки и брелоки по 50 ₽, почти все разобрали. На второй день подняли цену до 100 ₽, а потом до 200 ₽ — и все равно распродали остатки.
Поясные сумки шли чуть медленнее: каждая стоила 1000 ₽, и у некоторых людей цена вызывала недоумение. Они считали, что сумки должны быть дешевле, раз материал достался нам бесплатно. Но пошив каждой сумки обошелся в 500 ₽ — мы купили ремешки, молнии и оплатили работу швеи. Остальная часть цены — это затраты на электричество и наш труд.
Все, что мы заработали на фестивале, ушло на бензин и еду. В знак благодарности за место для торговли я взял на себя расходы на питание Андрея и доставку всего оборудования туда и обратно. Тогда я понял, что продажу изделий из переработанного пластика можно развить в прибыльный бизнес.
Переехали из гаражей в цех
Первые два года мы принимали и перерабатывали пластик в гаражах. Сначала арендовали один за 5000 ₽, через год — второй, а еще через полгода — третий. Гаражи были в удобном месте, и люди сами привозили туда вторсырье. Но с началом пандемии стали спрашивать, можем ли мы забрать его от подъезда.
Так я организовал экотакси: за 200 ₽ забирал пластик у людей. В день было около пяти заявок, я выполнял их между делами, иногда помогала жена. Мы продержались год, а потом передали клиентскую базу друзьям — компании «Раздельно», которые теперь монополисты по вывозу вторсырья в Нижнем Новгороде.
В конце 2020 года владелец гаражей сказал, что собирается продать их, и предложил выкупить все три помещения. Я прикинул, сколько придется вложить в ремонт, и решил, что лучше арендуем что-то побольше.
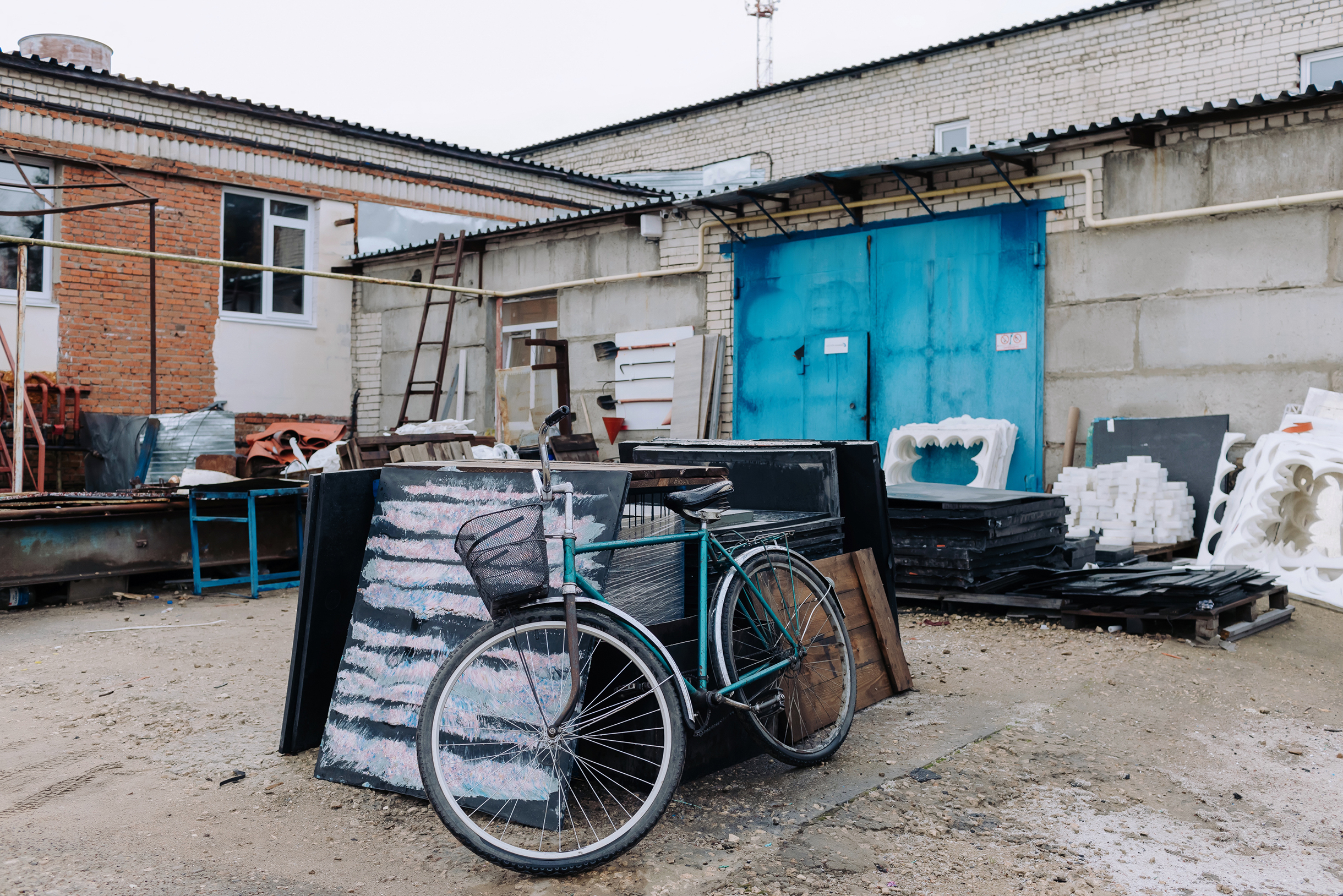
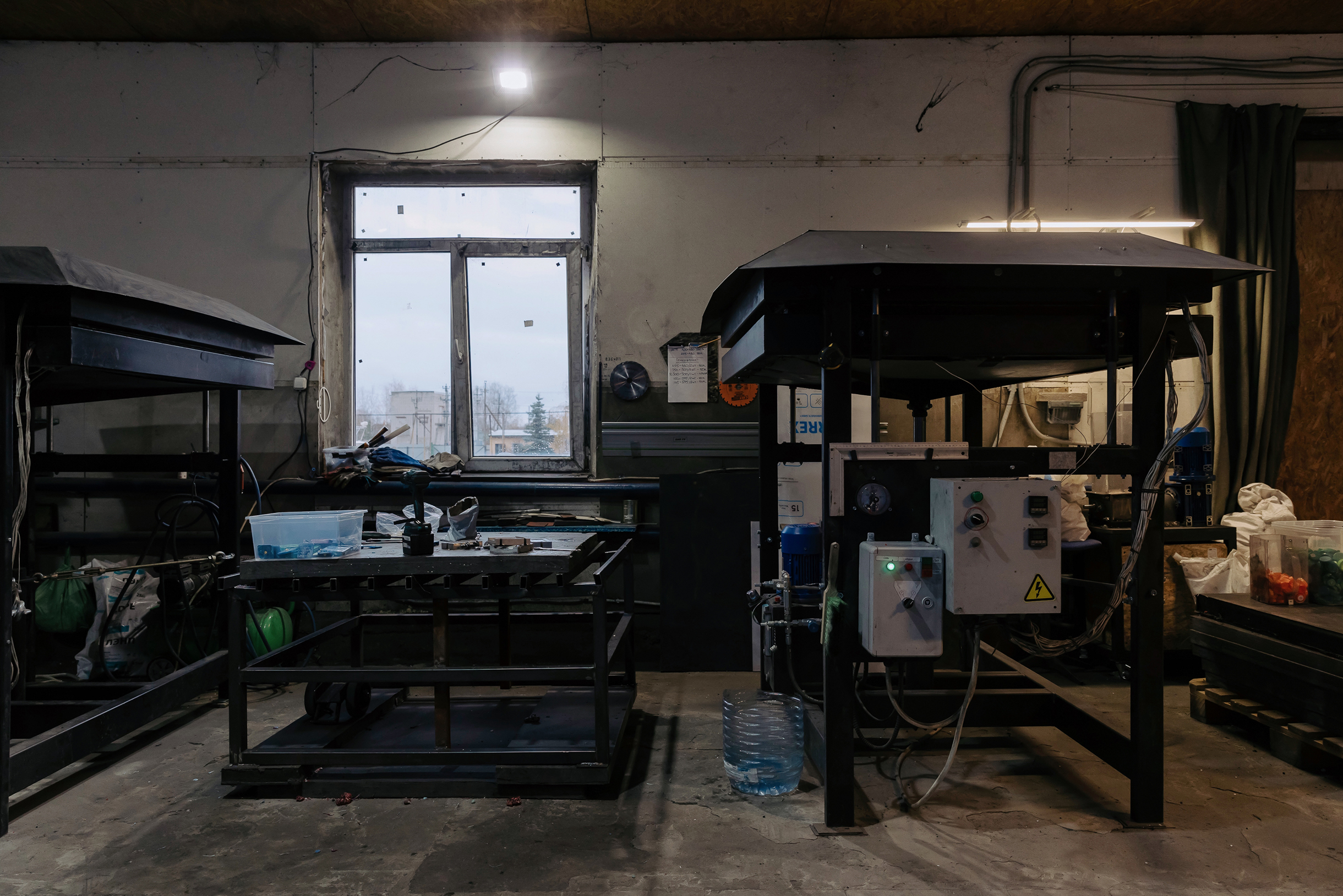
Я начал искать базы в черте города и за его пределами. В итоге выбрал помещение 120 м² за городом. На дорогу теперь уходит в пять раз больше времени, но место отличное: есть нужная мощность электричества, круглосуточный въезд, парковка и открытые складские площади. К тому же наладили сотрудничество с соседями: рядом сварочное производство, у них мы заказываем рамы для оборудования. В 2021 году аренда стоила 30 000 ₽, сейчас уже 50 000 ₽, плюс за электроэнергию платим еще 50 000 ₽ в месяц.
Перед тем как заехать, полгода делали ремонт: постелили пол, оштукатурили стены, поменяли проводку, добавили освещение, установили вентиляцию, поставили перегородки для разделения цеха. Отгородили офис в 15 м², где работаю я и сменные руководители. Сюда же приглашаем клиентов, показываем образцы и заключаем договоры.
Производственную часть разделили на два цеха: в одном — оборудование, сырье и готовая продукция, в другом — слесарная и мастерская, где собираем новое оборудование на продажу.
Ремонт обошелся в 300 000 ₽. В новом месте мы запустились в феврале 2021 года. С тех пор вкладываем по 100 000—150 000 ₽ каждый год в обслуживание, например частичный ремонт крыши.
Расходы на запуск производственного цеха в 2021 году
Всего расходов | 1 520 000 ₽ |
---|---|
Станок-гранулятор | 400 000 ₽ |
Зарплата сотрудникам во время ремонта | 360 000 ₽ |
Ремонт | 300 000 ₽ |
Аренда за полгода | 180 000 ₽ |
Оборудование и техника для офиса | 100 000 ₽ |
Непредвиденные расходы | 100 000 ₽ |
Видеонаблюдение | 50 000 ₽ |
Система пожарной безопасности | 30 000 ₽ |
Расходы на запуск производственного цеха в 2021 году
Всего расходов | 1 520 000 ₽ |
Станок-гранулятор | 400 000 ₽ |
Зарплата сотрудникам во время ремонта | 360 000 ₽ |
Ремонт | 300 000 ₽ |
Аренда за полгода | 180 000 ₽ |
Оборудование и техника для офиса | 100 000 ₽ |
Непредвиденные расходы | 100 000 ₽ |
Видеонаблюдение | 50 000 ₽ |
Система пожарной безопасности | 30 000 ₽ |
Сделал первый станок на продажу
На форуме «Территория смыслов» я познакомился с ребятами из екатеринбургской волонтерской организации «Делай». Они продвигают раздельный сбор мусора и экологическое предпринимательство. Когда они увидели, что из крышек можно делать полезные вещи, загорелись идеей обзавестись оборудованием. Ребята выиграли грант и купили мои станки — так я получил первый заказ.
На тот момент я уже производил шредеры, инжекторы и пресс-формы для отливки. Они хотели полный комплект, и я назвал цену — 150 000 ₽. Но у них был грант всего на 90 000 ₽, так что договорились на эту сумму. Для меня тогда было важнее не столько заработать, сколько запустить бизнес по производству станков и занять эту нишу.
Этот заказ был очень кстати. Я как раз планировал сделать новый электрошредер с улучшенным дизайном. Так что разработал для ребят усовершенствованную модель и немного подзаработал. Оборудование отправил не в Екатеринбург, а на Всемирный фестиваль молодежи в Сочи. Там они презентовали его и даже подарили брелоки из переработанного пластика администрации президента.
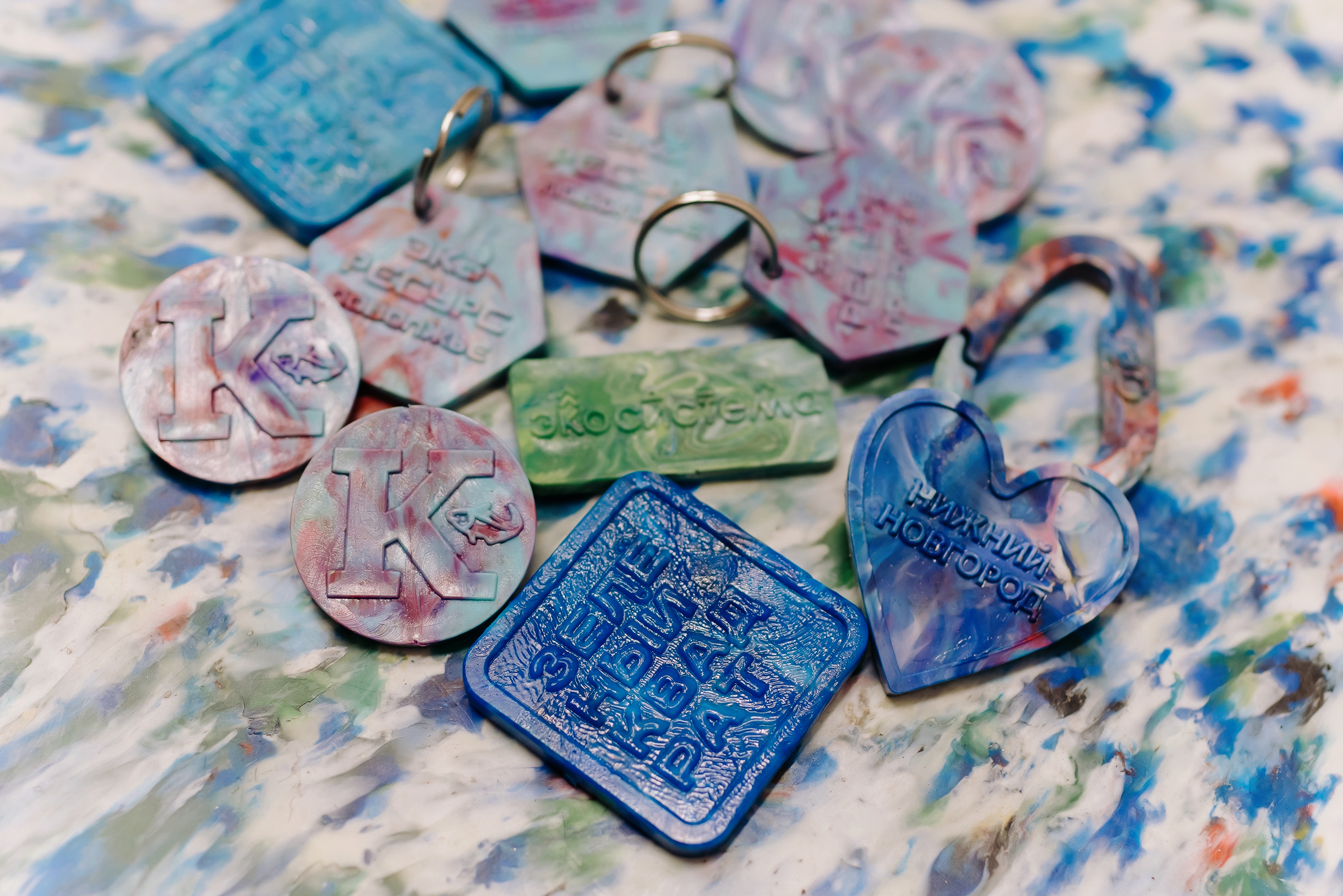
После этого заказа я понял, что государство готово поддерживать подобные проекты. Экоактивисты собирают мусор, но крупные заводы неохотно принимают его — нужен строгий контроль, чтобы не попадались этикетки и пластик с неправильной маркировкой. Так что активистам нужно свое оборудование, которое можно разместить в маленьком помещении, подключить к обычной розетке, открыть окно и за несколько часов переработать сырье в готовые изделия.
Так я стал пионером производства компактного оборудования для переработки в России. В прошлом году зарегистрировал торговую марку Infinity Plastic, потому что нас начали копировать — например, брали фото и описания с нашего сайта и сдавали наши станки в аренду, купив их у нас.
За 150 000 ₽ мы оформили защиту авторского права: теперь статьи и описания на сайте нельзя использовать без ссылки на Infinity Plastic. Патент на станок стоит 100 000 ₽ и занимает 15 месяцев. Процесс все еще идет.
Что мы производим и продаем
У нас сейчас три направления: делаем и продаем оборудование для переработки, создаем изделия из вторичного пластика и участвуем в фестивалях с лекциями.
Начну со станков. В 2021 году мы сделали первый велошредер для городского фестиваля. После этого пошли заказы. Уже через пару месяцев отправили два таких же в Рязань. Тогда он стоил 150 000 ₽, сейчас — 275 000 ₽. Сам велошредер не изменился, но комплектующие сильно подорожали.
Первый велошредер мы собрали из старого велосипеда. Сейчас используем только новые «Стелсы» — так проще, не приходится каждый раз переделывать конструкцию. Иногда просят сделать на базе велосипеда заказчика, но мы отказываем: нужно заново проектировать соединение с измельчителем, а это долго. Обычно с велошредером или электрошредером еще берут инжектор для плавления крошки.
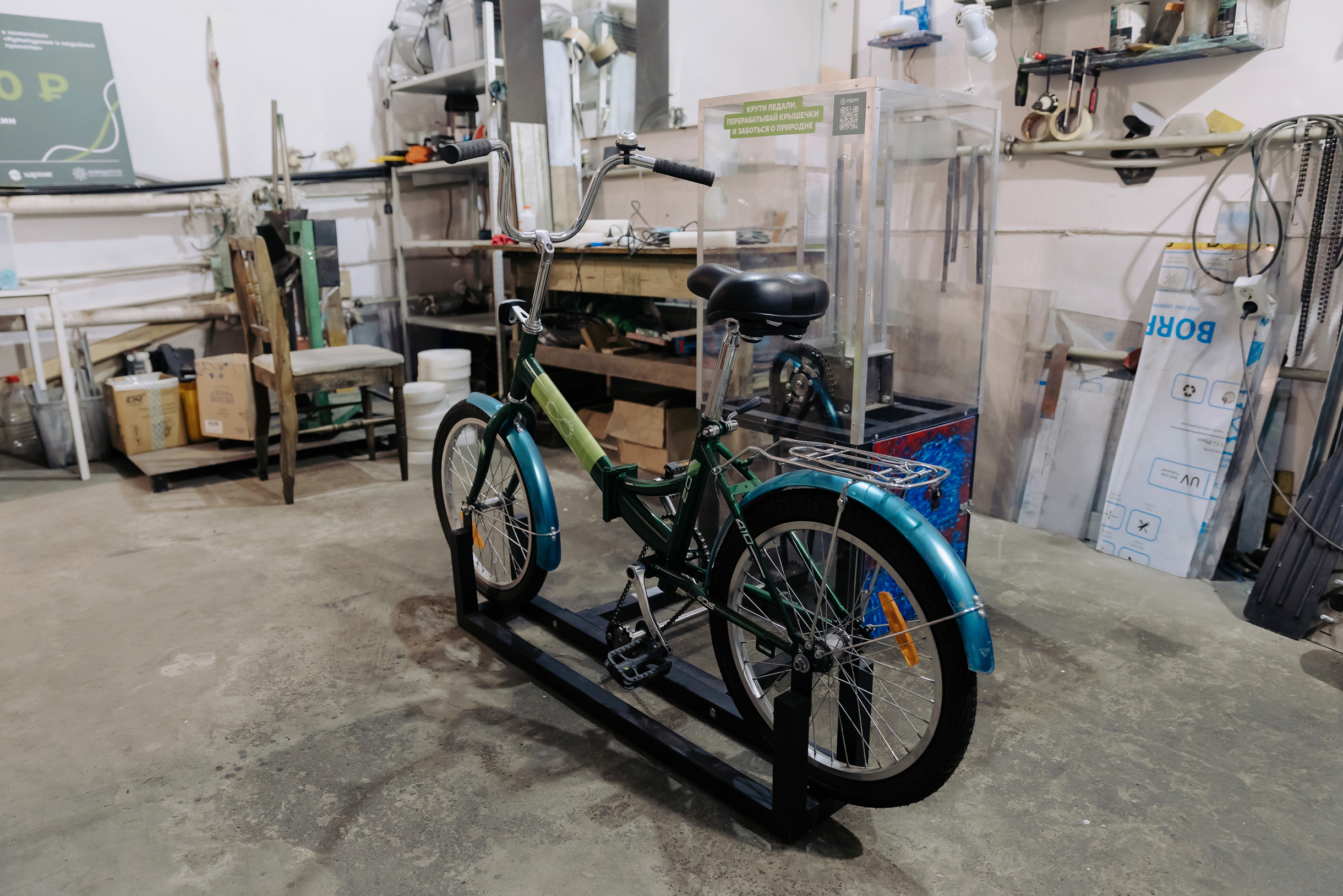
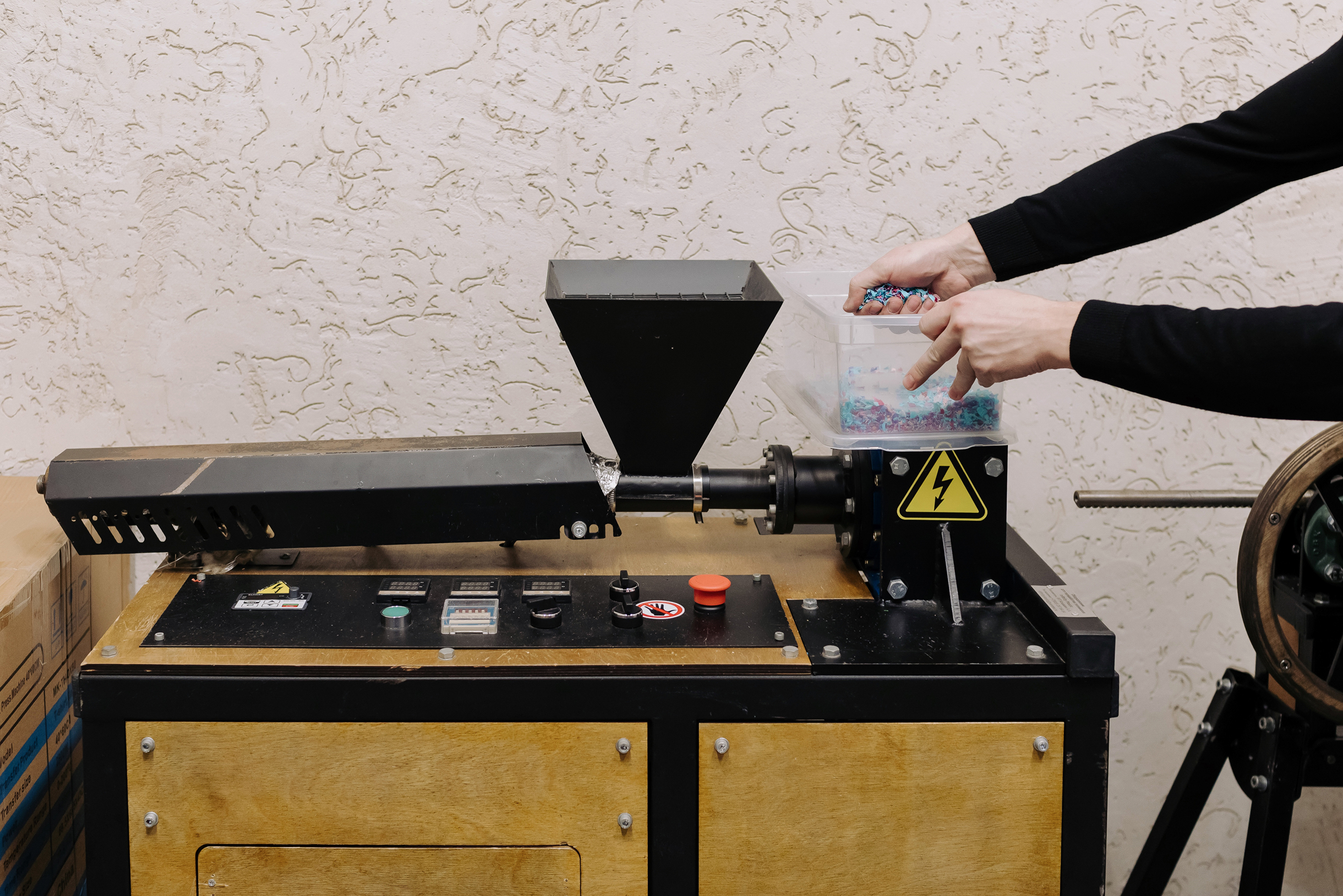
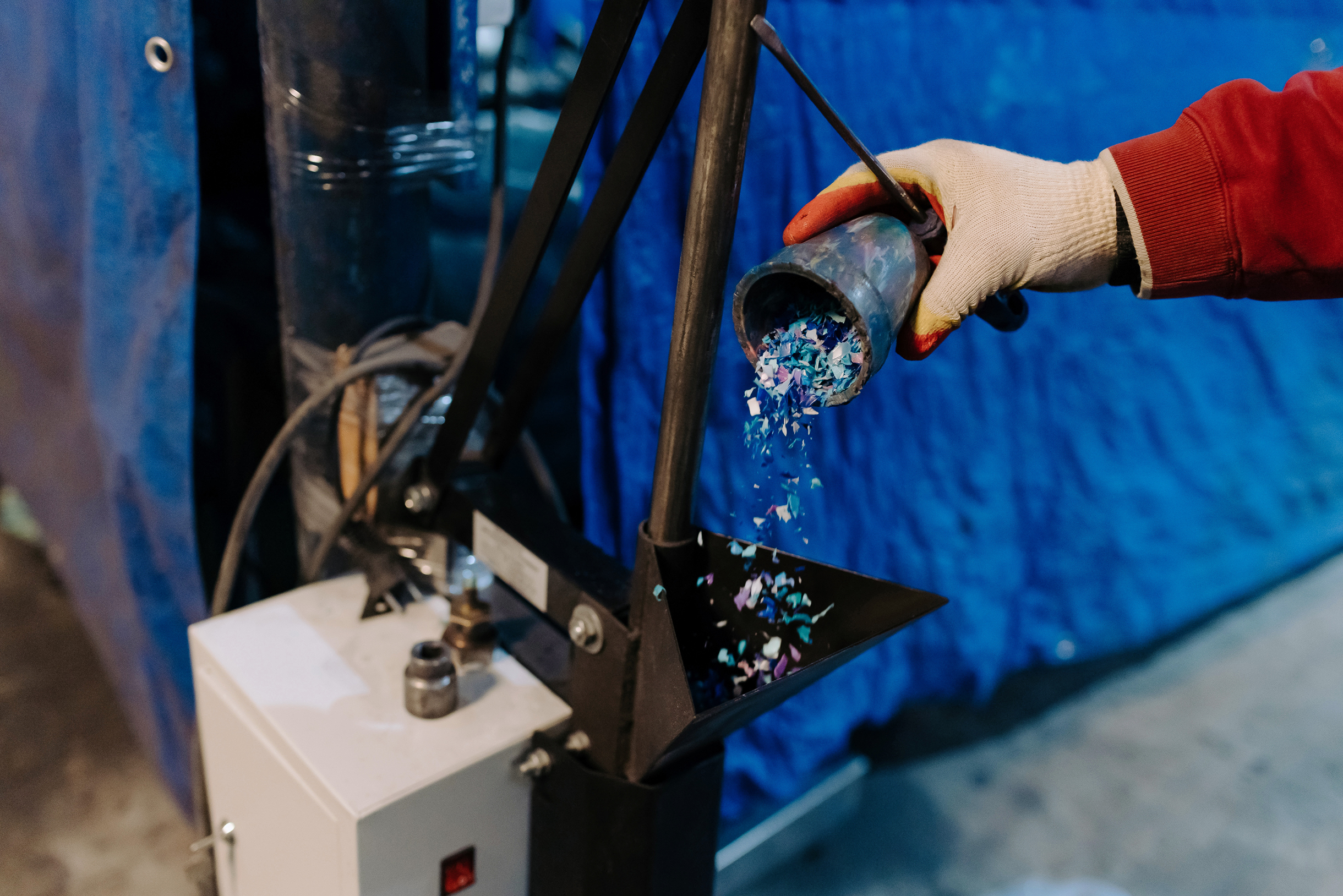
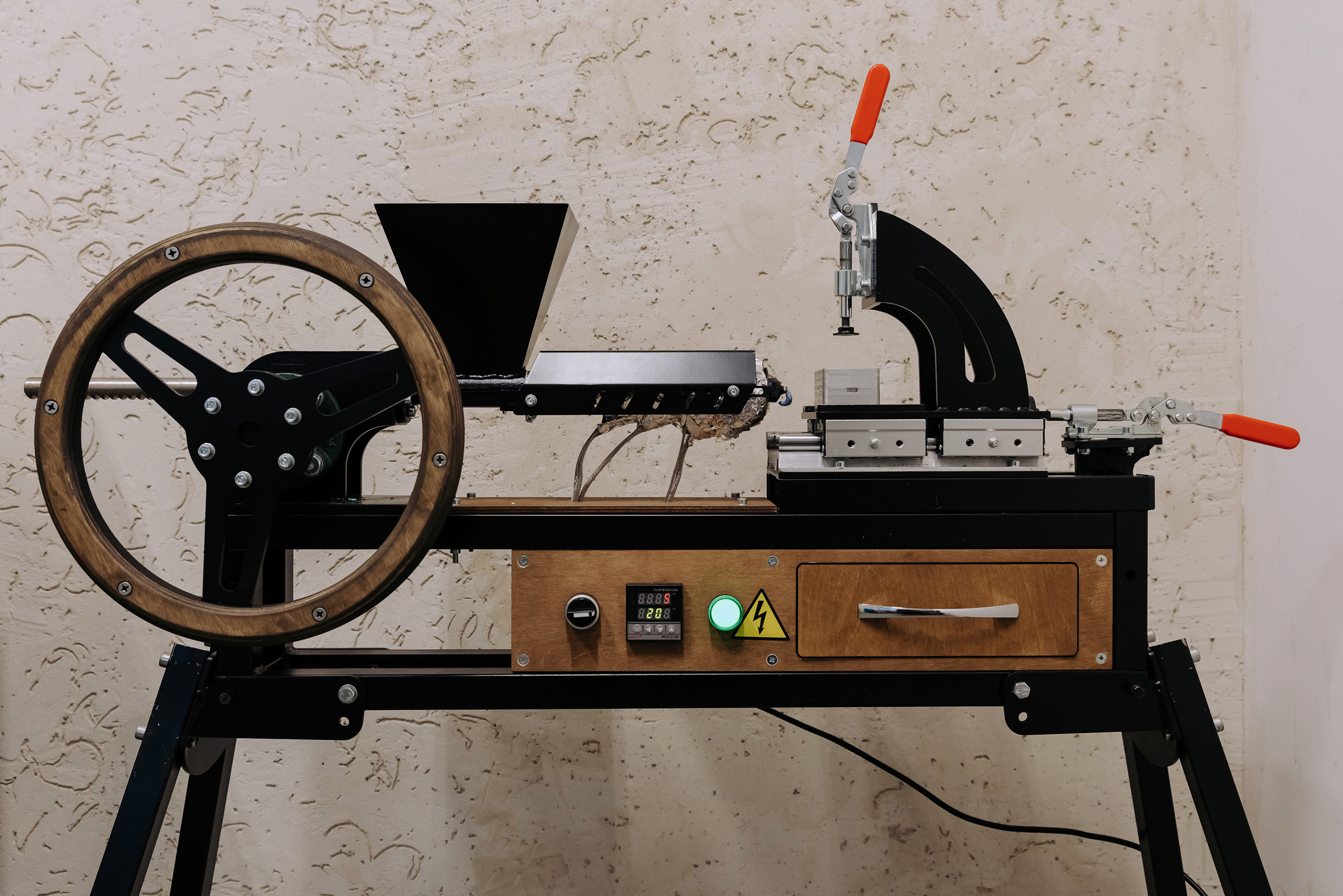
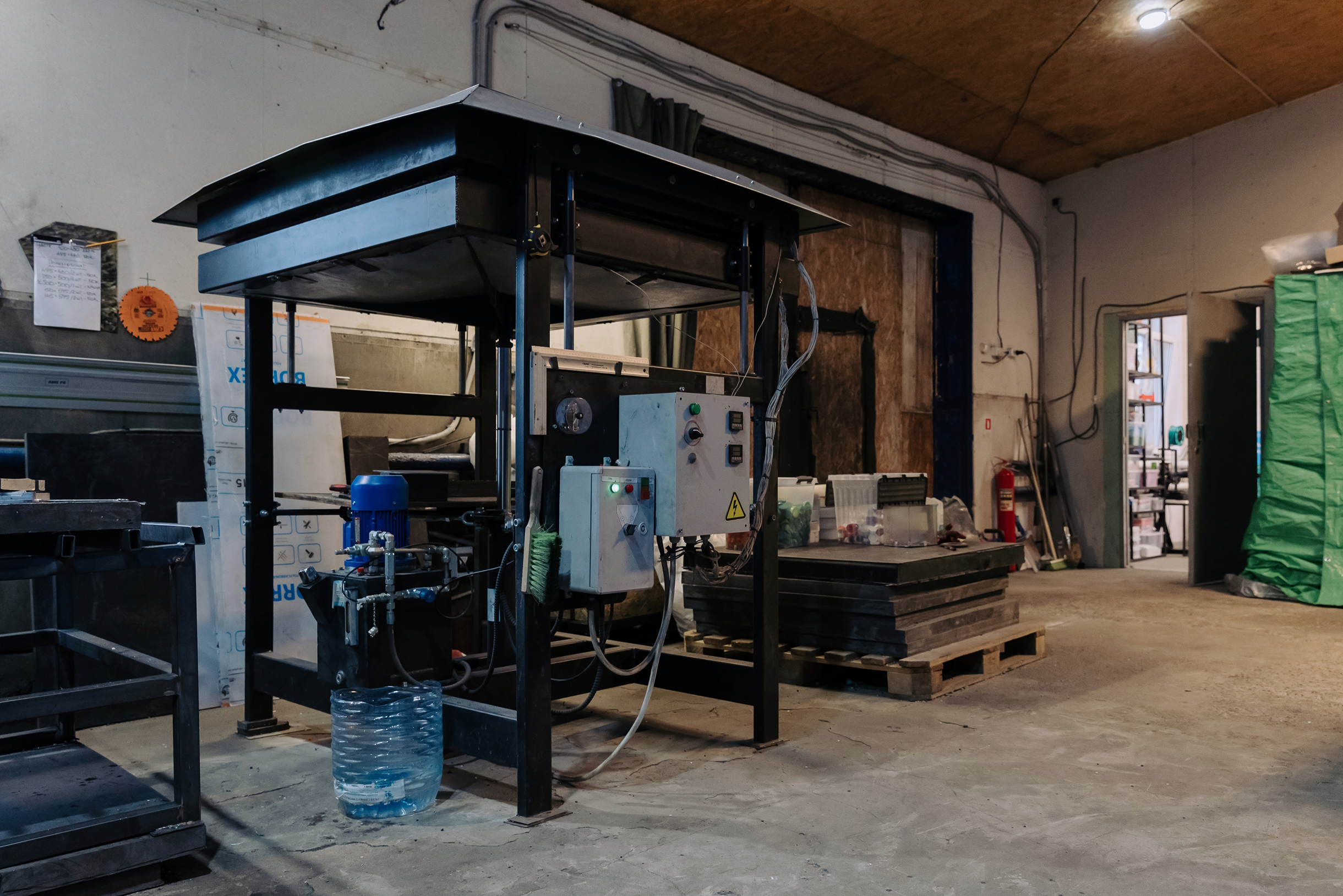
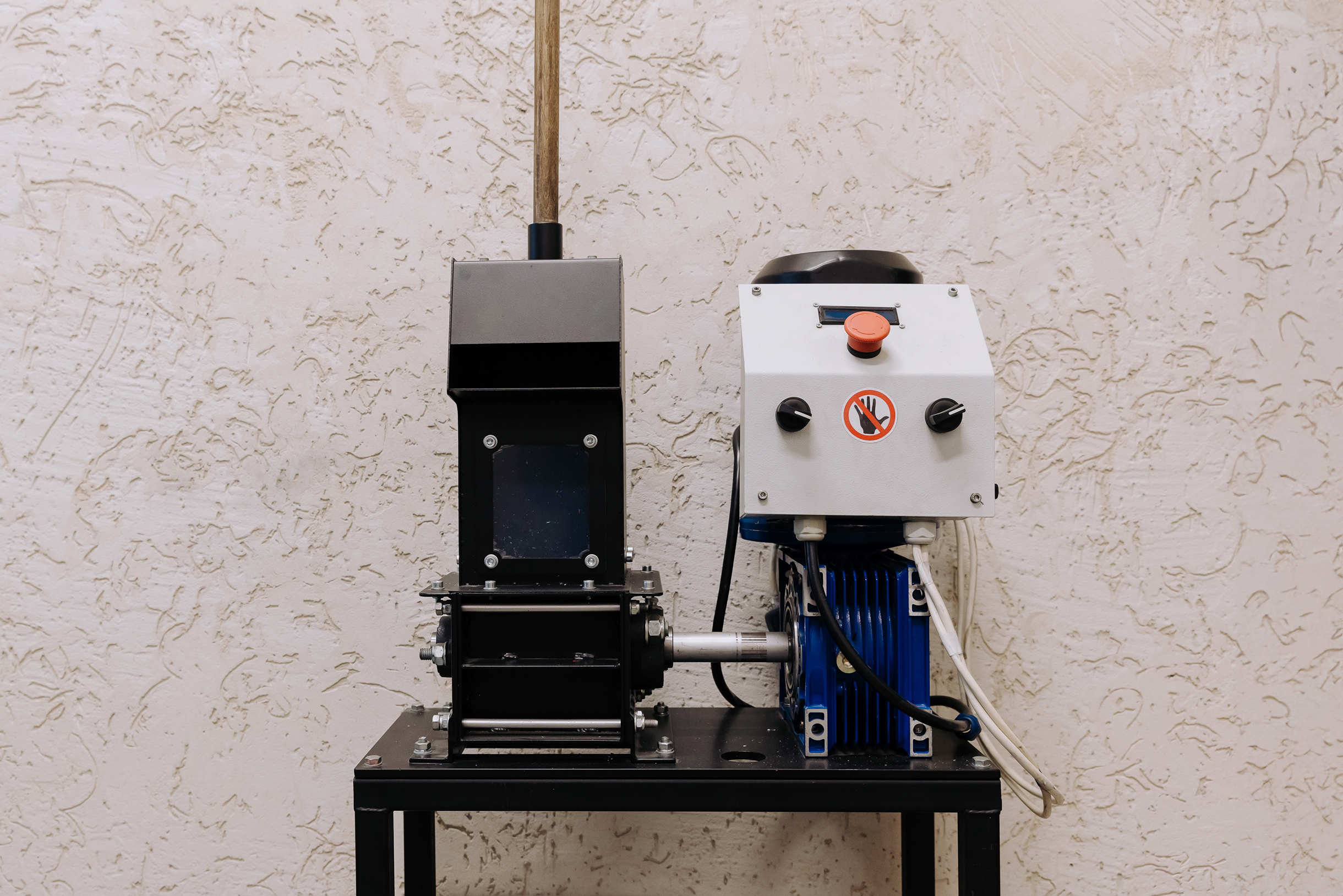
Оборудование обычно покупают комплектами: один из измельчителей, инжектор или экструдер, а также пресс-формы. До конца 2024 года мы планируем продать семь таких комплектов, каждый из которых стоит около 1 млн рублей.
Помимо станков мы производим пластиковые изделия. Работа идет в две смены: днем и ночью. Серийно мы выпускаем только листы из переработанного пластика. Их в основном покупают мебельные производства и используют вместо фанеры. Например, для столов, кресел-качалок и уличной мебели.
Процесс выглядит так: рабочие загружают измельченный пластик в листовой пресс, где он нагревается 3—6 часов в зависимости от толщины изделия, приобретает форму квадрата и остывает под прессом всю ночь.
Еще мы берем заказы на мерч вроде пластиковых брелоков, кружек, медалей. Делать их сложнее и дольше, чем листовой пластик. Для каждого заказа мы делаем пресс-форму — металлическую основу, в которую попадает горячий жидкий пластик и застывает там.
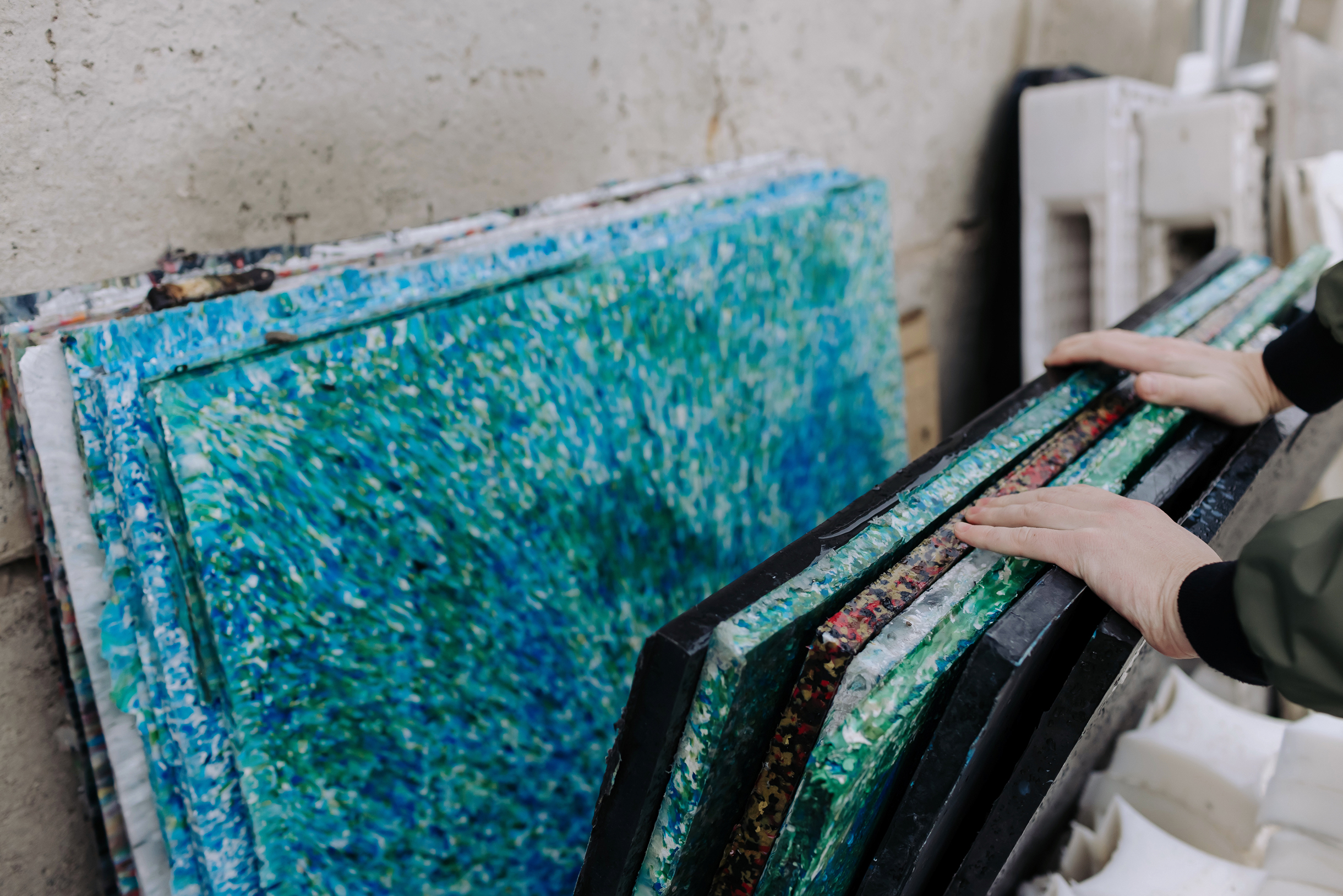
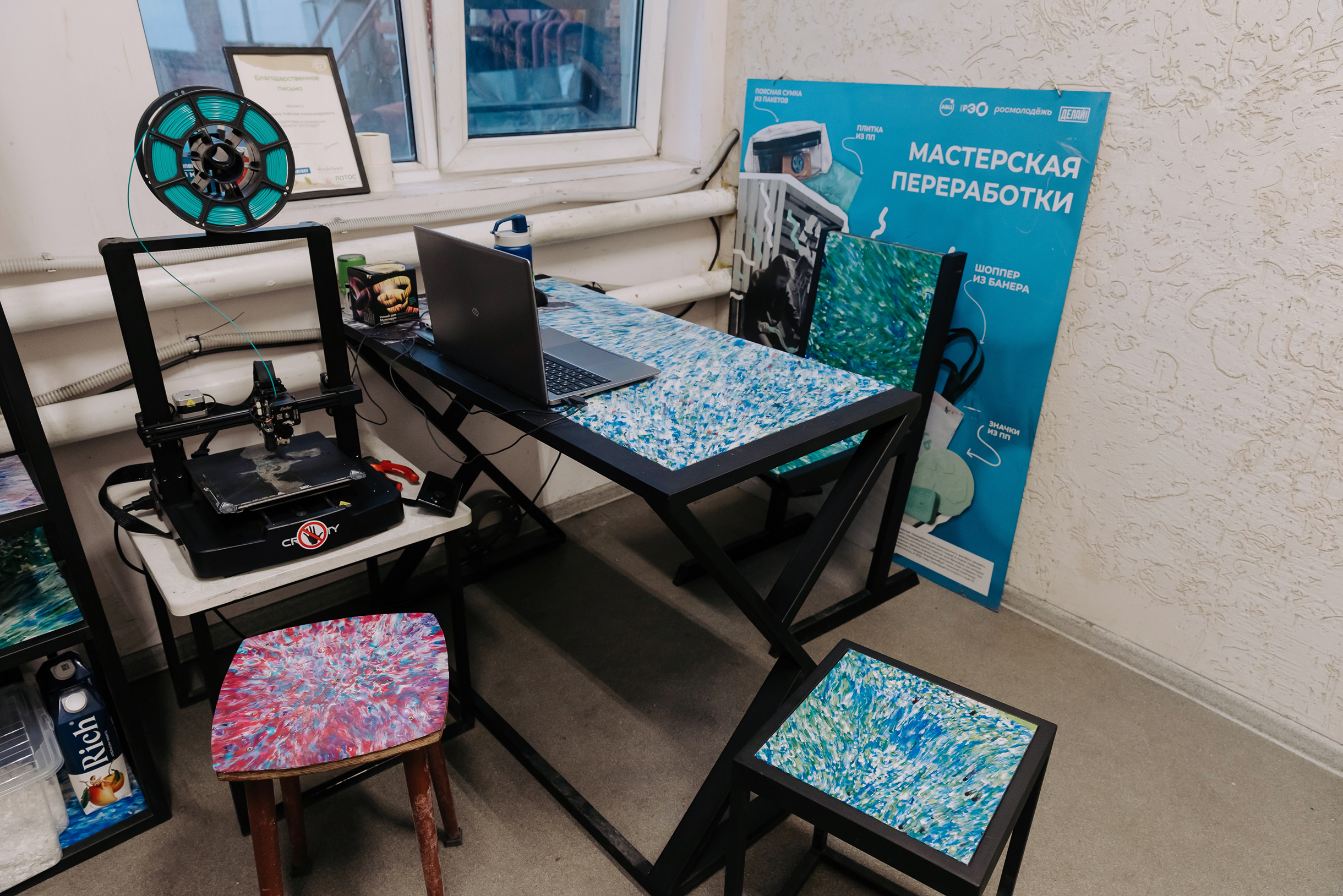
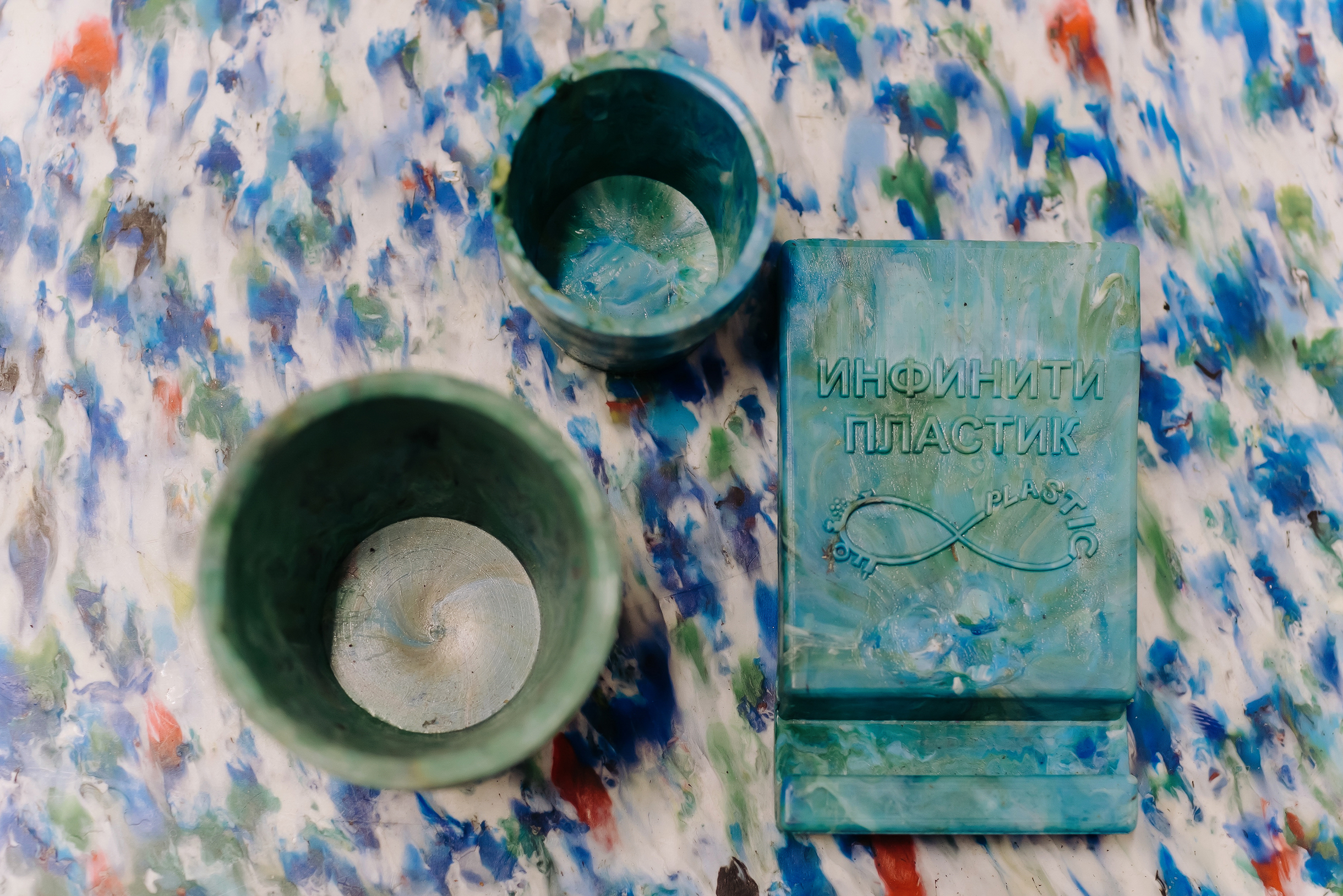
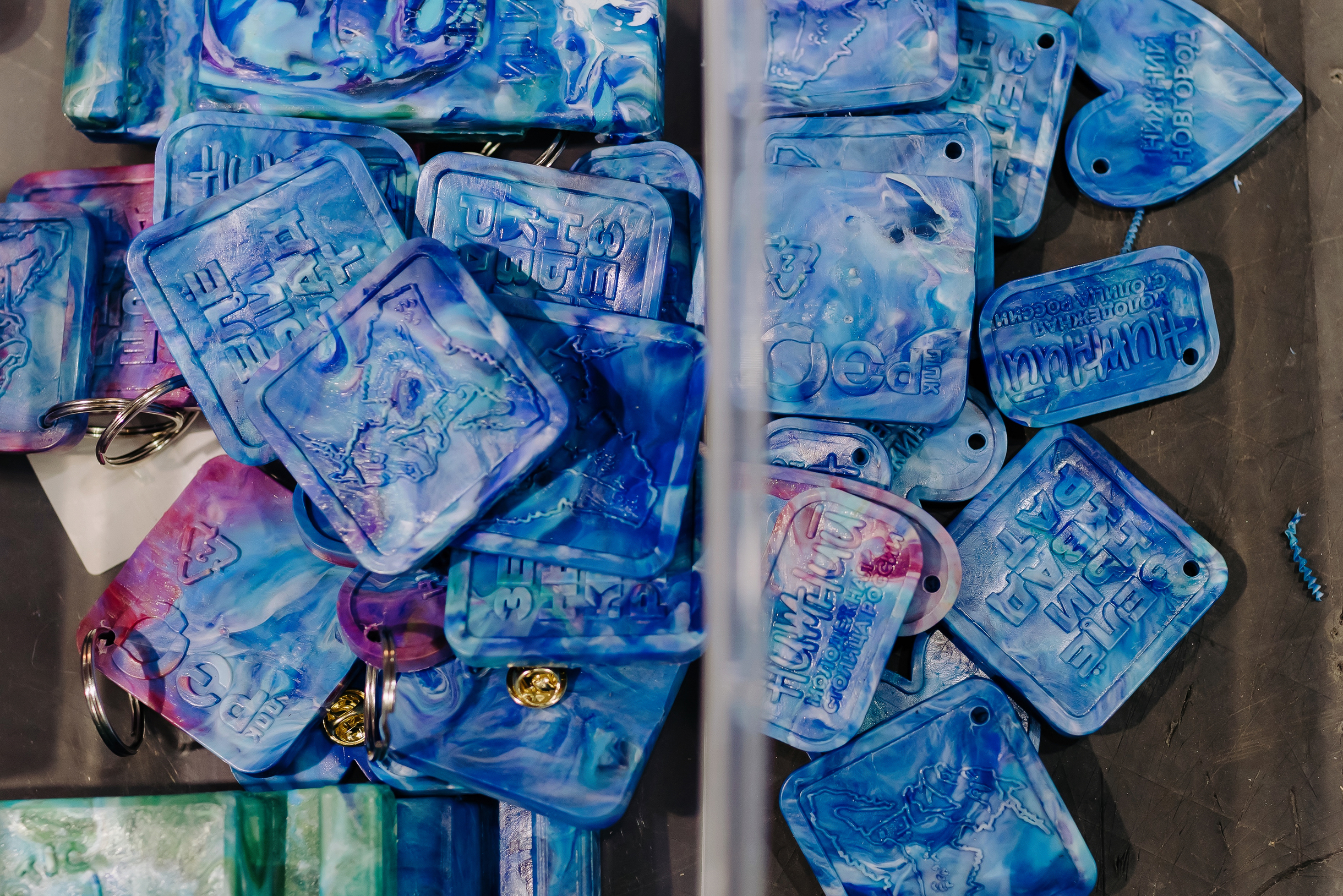
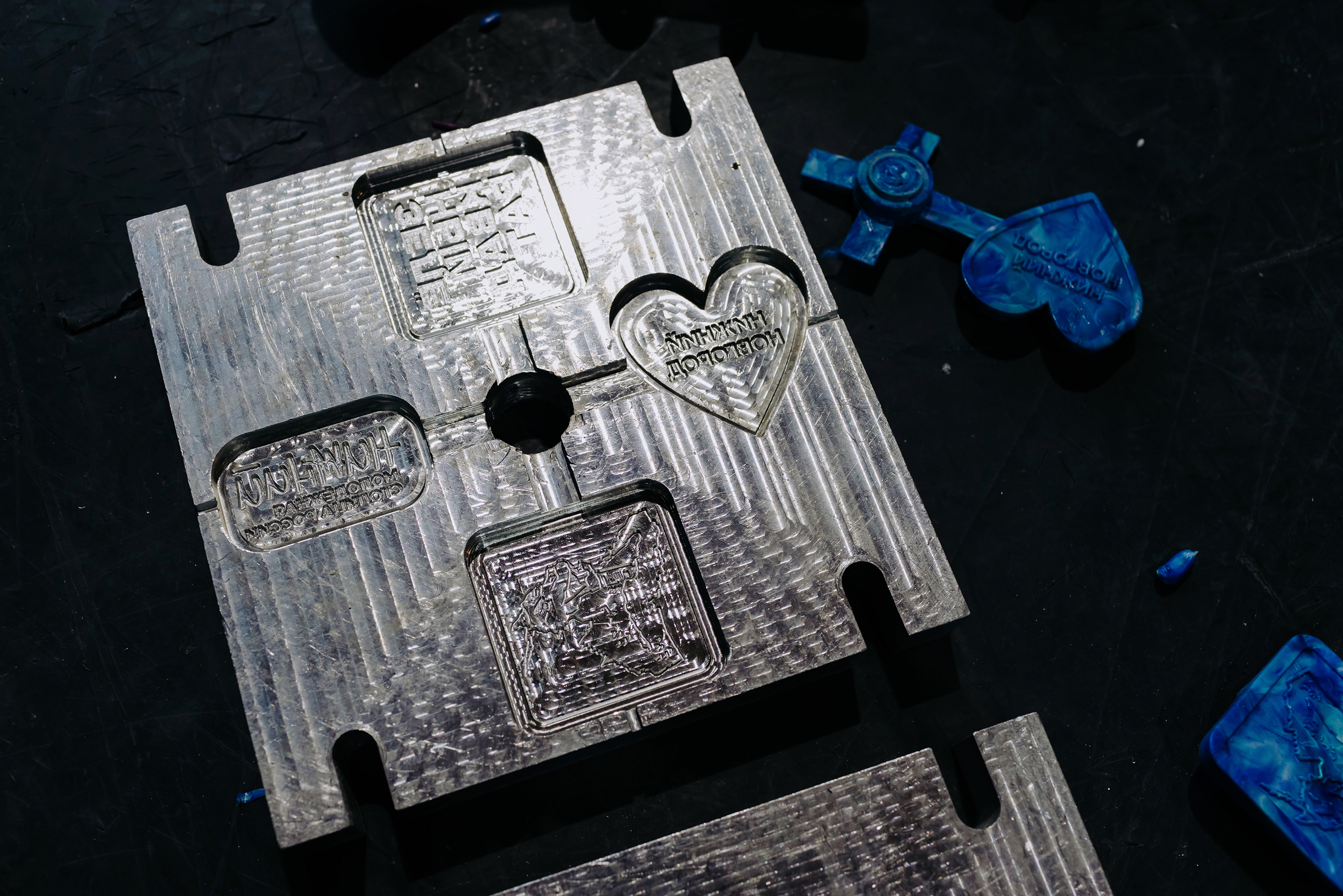
Дальше половину работы берет на себя инжектор: он нагревает, плавит пластик и выдавливает его в форму. Остальное делает рабочий: нажимает на рычаг, чтобы расплавленный пластик переместился в пресс-форму. Когда брелоки остынут, рабочий разбирает форму, достает изделия, обрезает лишний пластик по краям и прикрепляет к брелокам колечки.
Один такой цикл занимает около десяти минут. Если нужно сделать тысячу брелоков, а в форму помещается не больше 16 штук, получается 63 цикла. Это примерно десять с половиной часов работы. Вот такими заказами наши рабочие часто заняты на производстве.
При больших заказах, например на пять тысяч брелоков, наших запасов пластика одного цвета часто не хватает. Обычно мы покрываем около 20%, а остальное собираем или закупаем у экоорганизаций — волонтеров, которые собирают чистый сортированный пластик у людей и передают его нам. Школы и детские сады бесплатно отдают крышки при самовывозе. Если требуется сразу много, я обращаюсь к нижегородской организации «Раздельно» или к питерским «Добрым крышечкам».
Крышки, как я уже говорил, бывают с маркировкой 2, 4 или 5, но иногда попадаются сложные многокомпонентные — с такими мы не работаем. Для переплавки нужны отсортированные по типу пластика и цвету. Мы либо сортируем их сами на производстве, либо покупаем уже рассортированные у волонтеров. Несортированные стоят 30—50 ₽ за 1 кг, а рассортированные — 100—300 ₽.
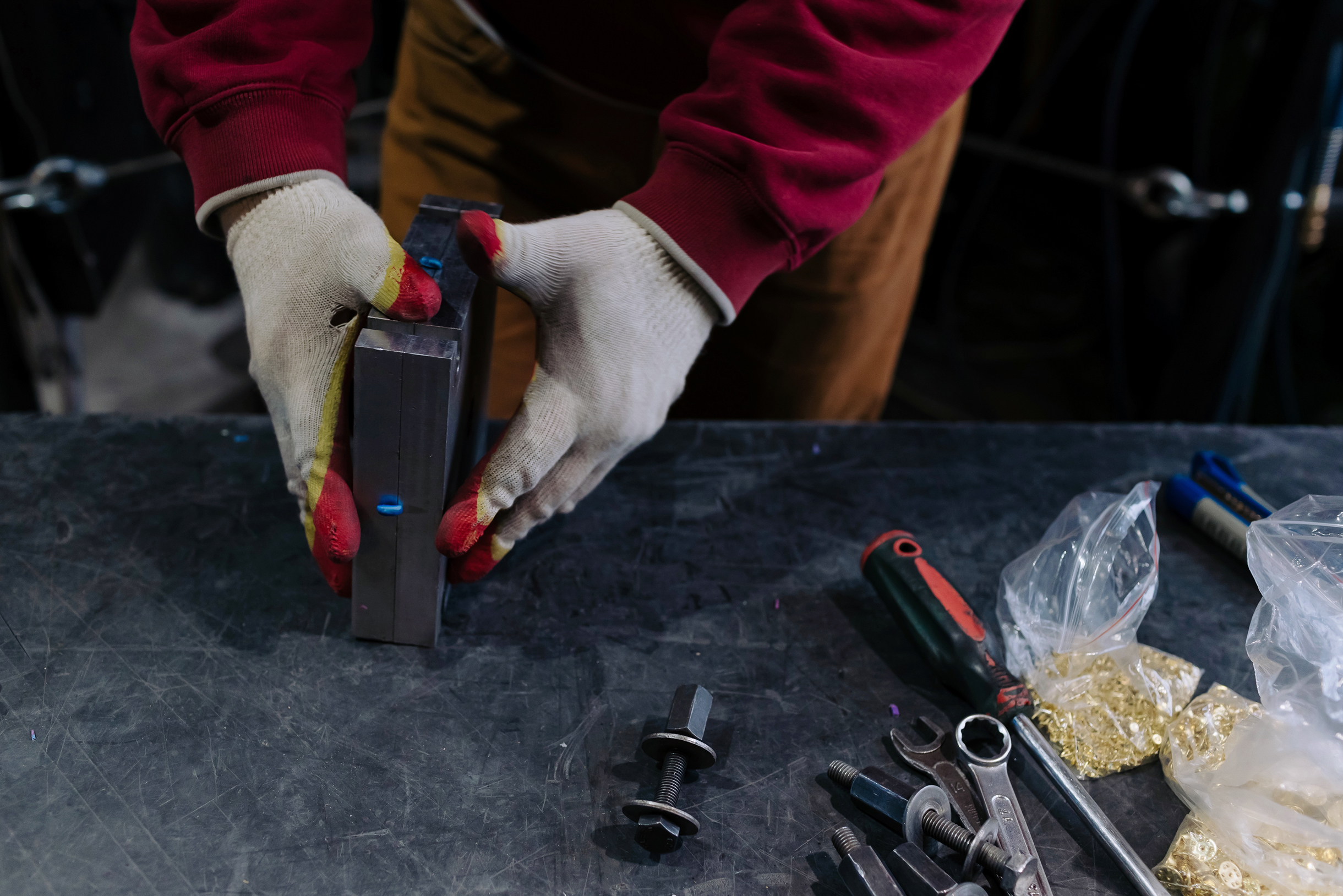
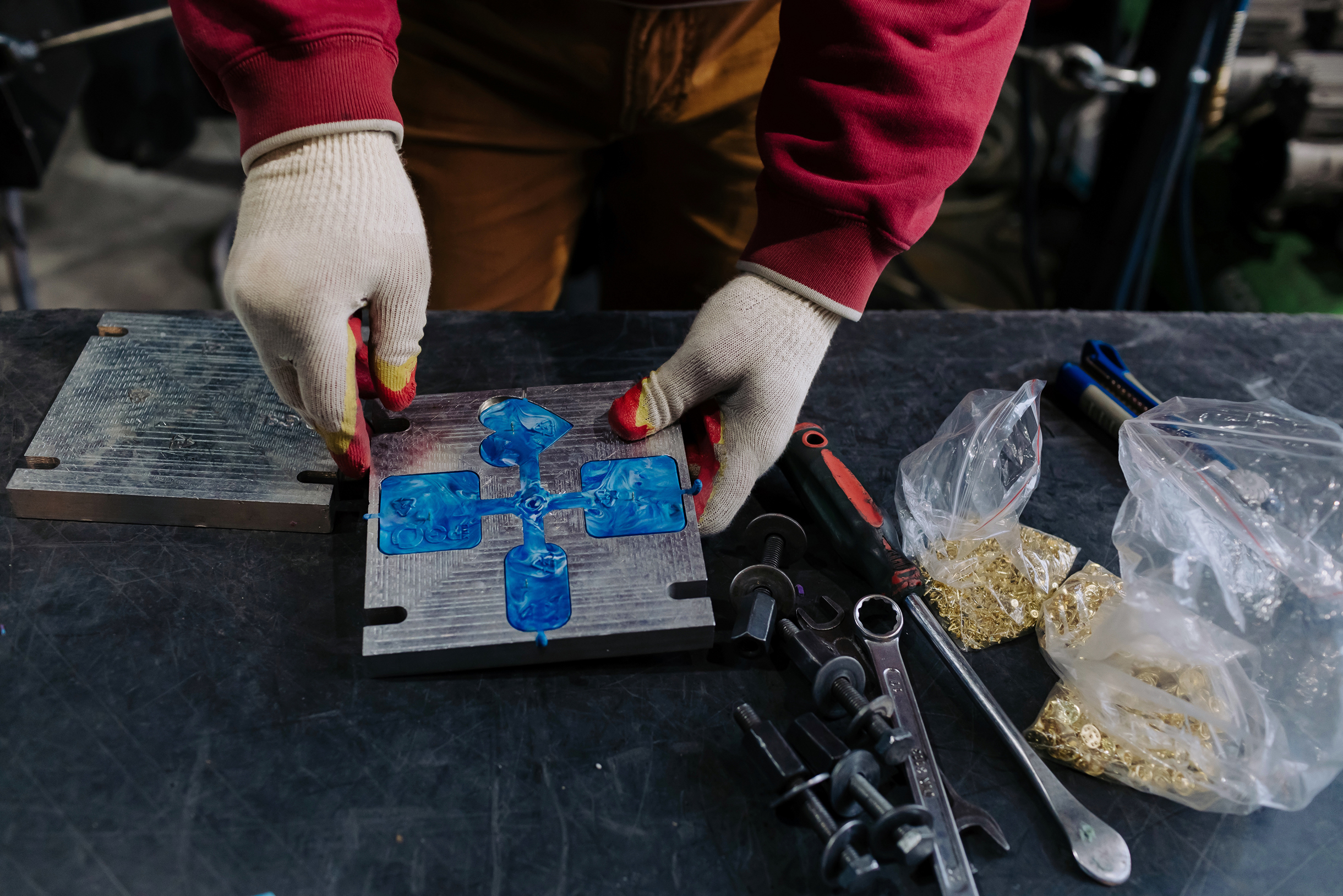
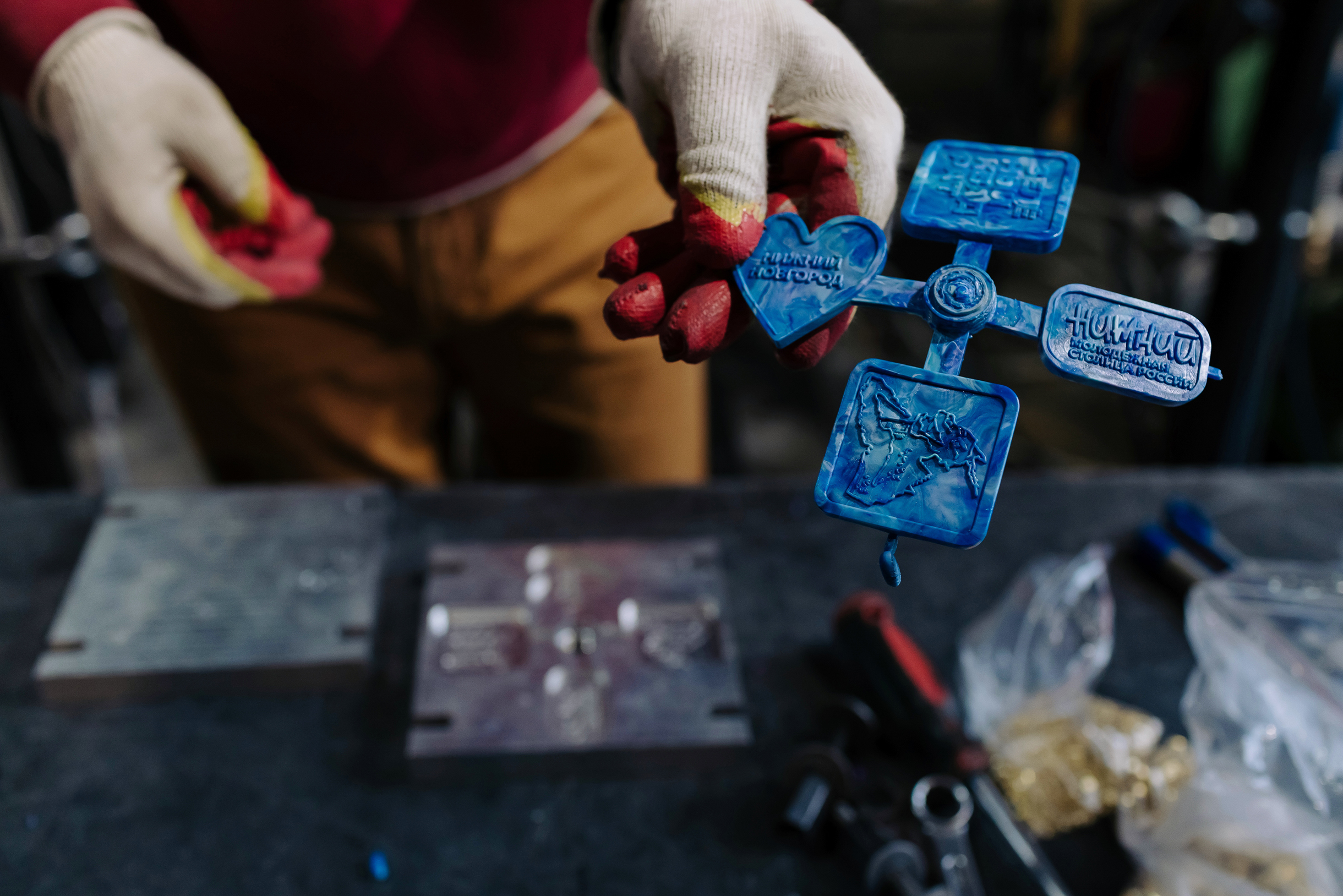
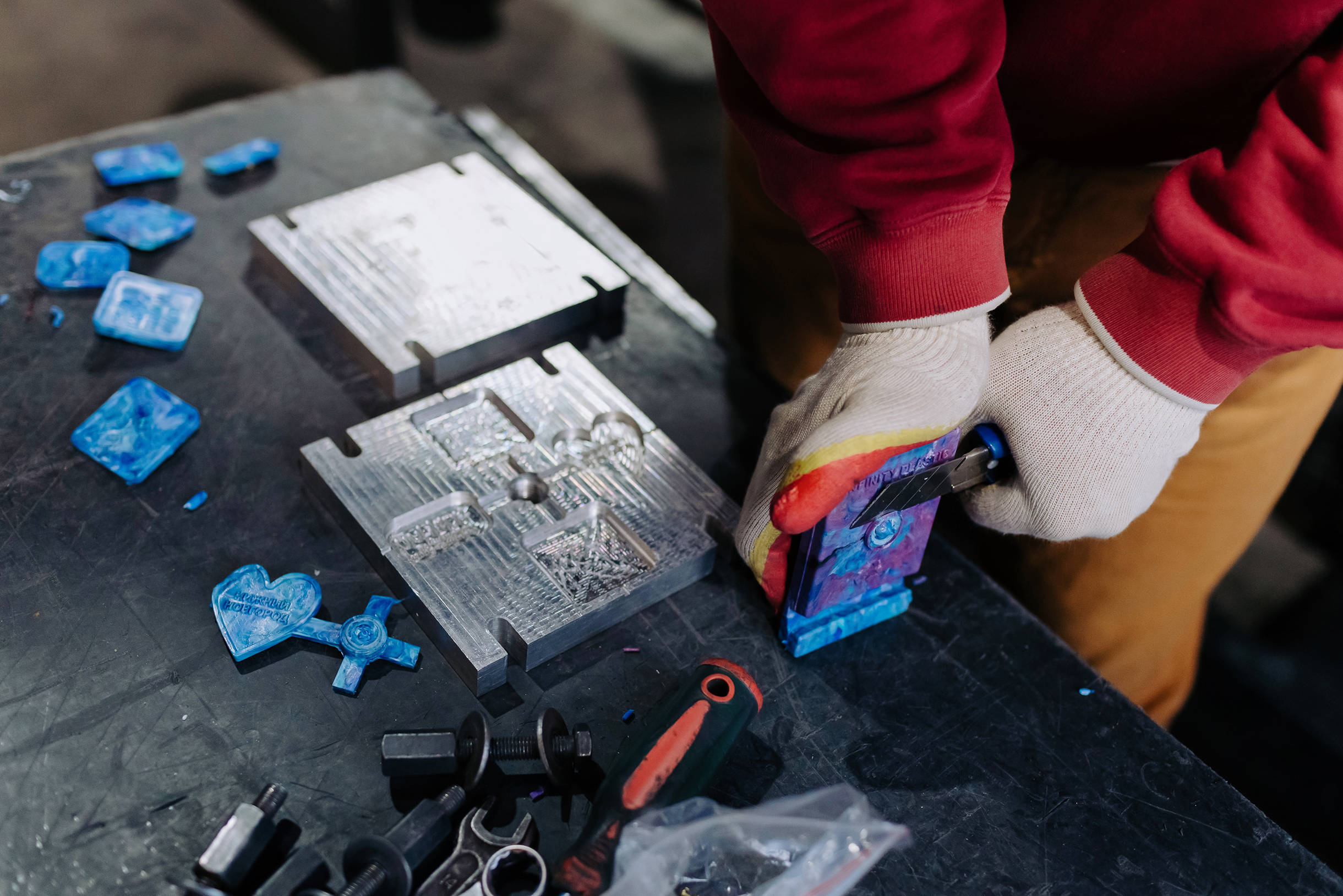
На фестивалях можем получить 200 000 ₽ в день
В 2022 году мы побывали на 40 выставках и фестивалях. Все оборудование я возил на своей машине. Мы тратили деньги на установку стендов, которые потом не могли забрать — это было неудобно, невыгодно и неэкологично. Так появилась идея сделать мастерскую на колесах.
В 2023 году мы заказали у производителя прицепов проект «Зеленого фургона». Для нас сделали прицеп на базе фудтрака с перегородками, между которыми я разместил оборудование. Внутри помещаются все наши станки, сырье, расходники и готовая продукция.
Теперь мы прицепляем фургон к любому автомобилю, приезжаем на фестиваль, проводим мастер-класс и бесследно уезжаем, не оставляя после себя строительного мусора. А иногда увозим с собой вторсырье, которое сдают люди. Нам нужна только розетка, чтобы все заработало.
Нас с «Зеленым фургоном» часто приглашают крупные компании, которые закрывают свои «экологические дыры». Например, производители полимеров или сигарет, которым выделили бюджет на экоразвитие. Они проводят три-четыре экодня в год: копят пластик, а во время экодней перерабатывают его на нашем оборудовании и изготавливают сувениры, для которых мы заранее готовим пресс-формы.
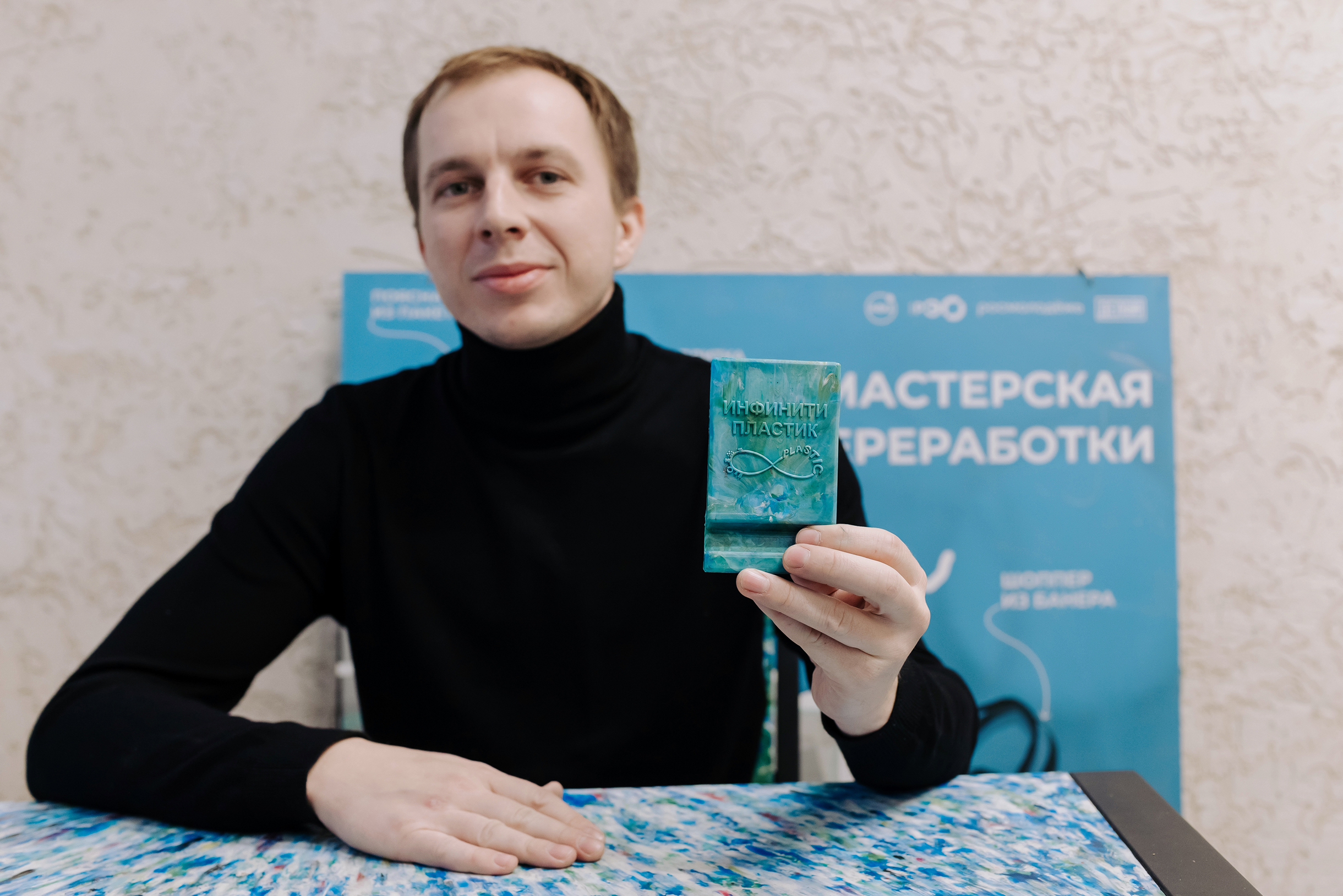
Мы, если нас об этом просят, брендируем фургон в фирменном стиле компании, одеваем сотрудников в футболки с логотипом заказчика. На мероприятии рассказываем про переработку и помогаем сотрудникам сделать что-то из пластиковых крышек.
Средний чек за день работы — 200 000 ₽. Если мероприятие длится три-четыре дня, общая сумма — 400 000 ₽. Примерно половина уходит на расходы: бензин, обслуживание автомобиля, зарплату водителю и платные дороги. Далее идут расходы на сотрудников — мы платим каждому по 9000—10 000 ₽ в день, а также покрываем их проживание и питание. Третья статья расходов — сырье и расходные материалы.
Например, за день работы в Москве мы заработали 400 000 ₽. На мероприятии работало семь человек посменно. Я закупил расходные материалы, оплатил труд, дорогу и проживание сотрудников. В итоге чистая прибыль — почти 170 000 ₽.
Расходы и прибыль на Дне города в Москве в 2023 году
Доход | 400 000 ₽ |
Расходы | 230 500 ₽ |
Чистая прибыль | 169 500 ₽ |
Зарплата шести сотрудникам | 60 000 ₽ |
Изготовление пресс-формы для мероприятия | 60 000 ₽ |
Оплата проезда и проживания сотрудников | 52 500 ₽ |
Расходники | 30 000 ₽ |
Зарплата куратора | 20 000 ₽ |
Транспортировка фургона и зарплата водителю | 8 000 ₽ |
Расходы и прибыль на Дне города в Москве в 2023 году
Доход | 400 000 ₽ |
Расходы | 230 500 ₽ |
Чистая прибыль | 169 500 ₽ |
Зарплата шести сотрудникам | 60 000 ₽ |
Изготовление пресс-формы для мероприятия | 60 000 ₽ |
Оплата проезда и проживания сотрудников | 52 500 ₽ |
Расходники | 30 000 ₽ |
Зарплата куратора | 20 000 ₽ |
Транспортировка фургона и зарплата водителю | 8 000 ₽ |
Кто работает в команде
В 2021 году половину рабочего времени я тратил на основной бизнес, остальное — на Infinity Plastic. Сейчас переработка занимает 80% рабочего времени. Я сам общаюсь с заказчиками, езжу на фестивали. Плюс часто мне помогает жена.
Все, что касается производства пластиковых изделий, я делегирую двум тезкам Алексеям. Они начальники смен на производстве. У каждого в подчинении — два рабочих. С начальниками смен у нас есть рабочий чат «Три Алешки», туда я пишу производственные задачи.
Один из Алексеев раньше занимался маркетингом в «2ГИС». Так что сейчас он не только контролирует рабочих, но и находит новых клиентов. Например, мебельные производства, для которых мы делаем пластиковые столешницы.
Еще с нами работает водитель-разнорабочий, он многофункциональный помощник. Обычно он развозит заказы, но может помочь на производстве или на выставке.
Эти семь сотрудников — в штате. Рабочие и водитель получают по 40 000 ₽, начальники смен — 50 000 ₽. Но в некоторые месяцы, когда много работы, их премия превышает оклад. Я начисляю премии за нестандартные проекты и новые изделия. Например, создание арт-объекта на заказ, работу сверх нормы, срочные заказы, выезды на мероприятия. Плачу за сотрудников взносы в ПФР и ФСС, поэтому у ребят есть оплачиваемые отпуска и больничные, страховки и пенсии.
На аутсорсе с нами работает инженер-конструктор. Он делает чертежи новых изделий: станков, оборудования и сложных пластиковых конструкций, которые иногда нужны заказчикам.
Еще сотрудничаю с проектировщиком пресс-форм. Те, кто покупает у нас оборудование, заказывают формы для каждого нового изделия. Проектировщик разрабатывает их удаленно и высылает чертежи, по которым мы сами делаем пресс-формы.
Также на аутсорсе у нас бухгалтер. Плачу ей 10 000 ₽ в месяц. Она ведет первичную бухгалтерию и делает отчеты, а я закрываю текучку.
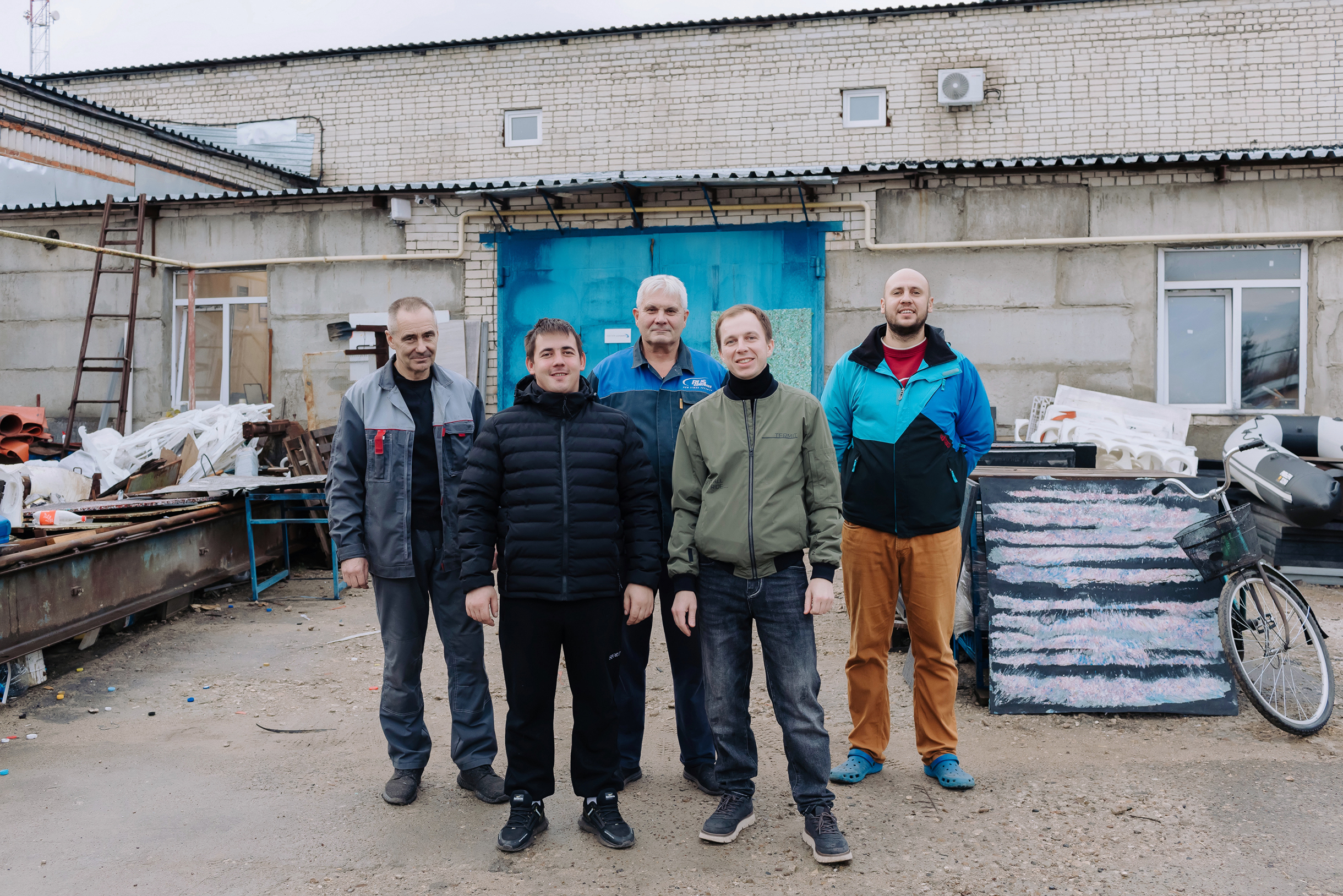
Даем пожизненную гарантию
Продажей оборудования занимается отдельный сотрудник на аутсорсе. Он отвечает за то, что мы называем социальной франшизой, и получает 50 000 ₽ в месяц. Я называю каждую продажу комплекта станков социальной франшизой. Сейчас объясню почему.
Социальная — потому что мы не берем взносы и роялти. Франшиза — потому что мы передаем покупателям методичку с инструкциями по проведению мастер-классов на оборудовании, добавляем их в общий чат для ответов на вопросы, а также передаем заказы из их городов, которые поступают к нам. Кроме того, мы бесплатно высылаем замену сломанных деталей и проектируем новые пресс-формы.
Мы заключаем с покупателем только договор на поставку оборудования, а франшизу официально не оформляем. Термин социальная франшиза придумал я — это скорее маркетинговый ход.
Социальной франшизой обычно пользуются экоорганизации, которые приобретают оборудование на грантовые деньги. Это могут быть региональные молодежные центры, университеты, центры развития малого бизнеса или экоцентры. Такие организации получают полное или частичное финансирование от государства. Как правило, от подачи заявки на грант до покупки оборудования проходит около года, и на этот период мы фиксируем для них цену.
Мы даем 12 месяцев гарантии на станки, так как используем в сборке покупные детали. Например, нагреватели и подшипники. Их производители предоставляют годовую гарантию, и мы передаем ее нашим покупателям. На части, которые изготавливаем сами, даем пожизненную гарантию — они служат десятилетиями.
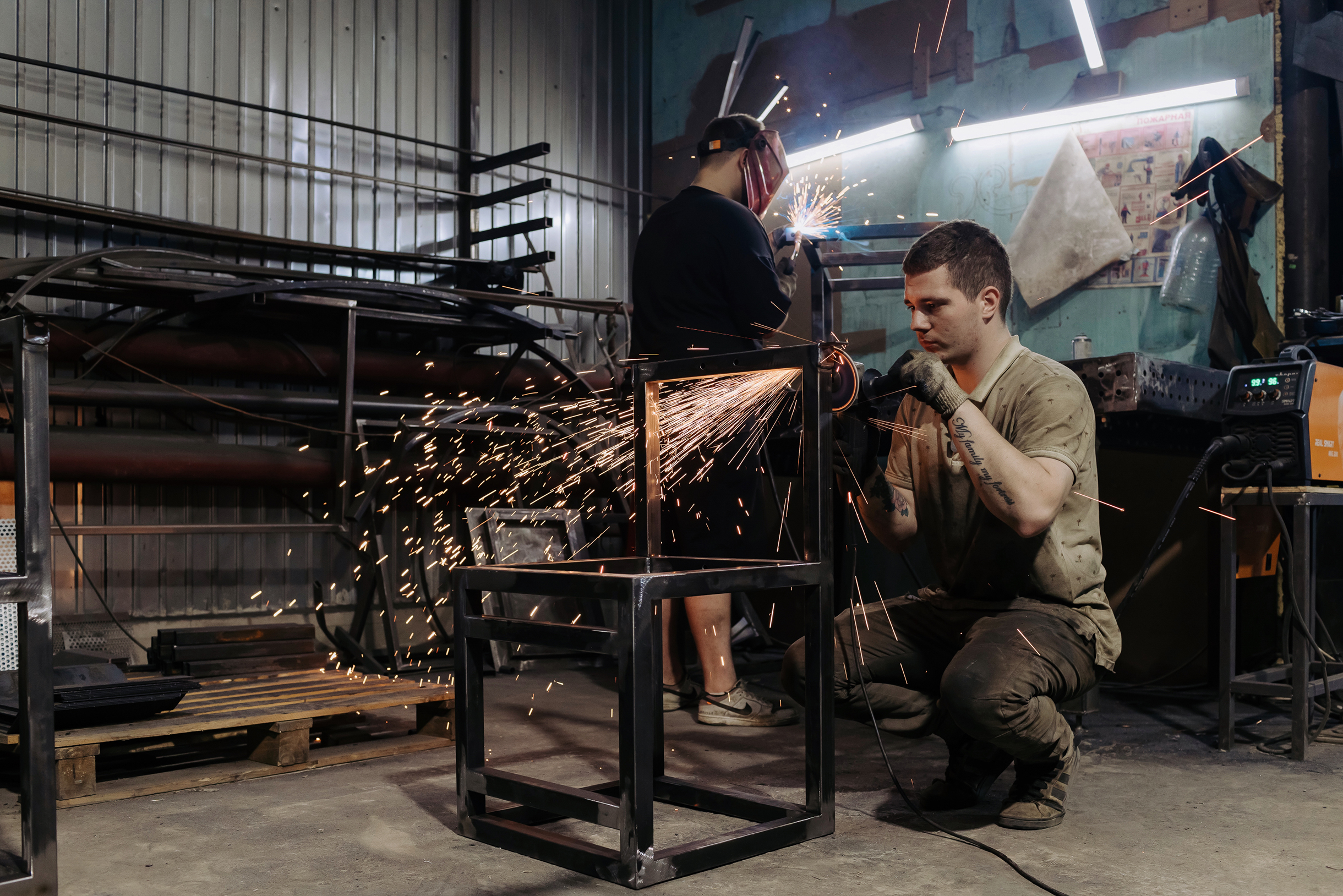
Когда на станке выходит из строя покупная деталь, я отправляю замену из своих запасов. Если это что-то недорогое, например подшипник, высылаю бесплатно. Дорогие детали тоже отправляю без оплаты, но договариваюсь с клиентом, чтобы он включил эту запчасть в следующую грантовую заявку. Тогда при продаже нового оборудования этому клиенту я получу плату и за деталь.
Если клиент приходит к франчайзи от нас, мы получаем 50% чистой прибыли. Это, например, мастер-классы на нашем оборудовании для учебных заведений. Стоимость одного мастер-класса — около 50 000 ₽, из которых мы зарабатываем 15 000—20 000 ₽. Если франчайзи находят клиентов самостоятельно, они ничего нам не платят.
В среднем я зарабатываю 300 000—500 000 ₽ в месяц. Половину оставляю в семье, а остальное реинвестирую в закупку материалов и комплектующих для станков, производство новых пресс-форм и ремонт помещения. Свободные деньги на покупку сырья у меня всегда есть, так как его продают только по предоплате.
В 2023 году оборот компании был 12 млн рублей. В этом году будет более 20 млн. 40% выручки принесли выездные мероприятия, столько же — продажи оборудования, 20% — пластиковые изделия.
В следующем году найму еще двух сотрудников на производство. Планируем развивать переработку: ставить ящики из переработанного пластика в детсадах, школах и университетах, собирать и сортировать больше крышек, а также увеличивать выпуск листового пластика.
Операционные расходы за сентябрь 2024 года
Выручка в месяц | 1 270 000 ₽ |
Всего расходов | 870 000 ₽ |
Прибыль | 400 000 ₽ |
ФОТ | 350 000 ₽ |
Отчисления в ПФР и ФСС | 245 000 ₽ |
Налоги | 100 000 ₽ |
Аренда | 50 000 ₽ |
Коммунальные расходы | 50 000 ₽ |
Расходные материалы | 40 000 ₽ |
Логистика | 15 000 ₽ |
Ремонт | 10 000 ₽ |
Амортизация оборудования | 10 000 ₽ |
Операционные расходы за сентябрь 2024 года
Выручка в месяц | 1 270 000 ₽ |
Всего расходов | 870 000 ₽ |
Прибыль | 400 000 ₽ |
ФОТ | 350 000 ₽ |
Отчисления в ПФР и ФСС | 245 000 ₽ |
Налоги | 100 000 ₽ |
Аренда | 50 000 ₽ |
Коммунальные расходы | 50 000 ₽ |
Расходные материалы | 40 000 ₽ |
Логистика | 15 000 ₽ |
Ремонт | 10 000 ₽ |
Амортизация оборудования | 10 000 ₽ |
Мы ищем предпринимателей. Если хотите рассказать историю своего бизнеса — заполняйте анкету