Как я покрывал модуль автодома гелькоутом и утеплял крышу
Этот текст написан в Сообществе, в нем сохранены авторский стиль и орфография
Переворот модуля и покрытие двух боковых стенок полиэфирной смолой не вызвало никаких трудностей, если не считать того, что чтобы отшлифовать свисающие капли и прочие неровности я использовал УШМ без пылеудаления, и несмотря на защиту, все в сарае было в пыли и чесался я потом дня два. Шлифовки в будущем предстояло много, так что чтобы подобного избежать у Д. была взята на временное пользование шлифмашина Hilti с пылеудалением. В остальном я уже полностью привык к полиэфирке и последнюю стену делал даже с удовольствием.
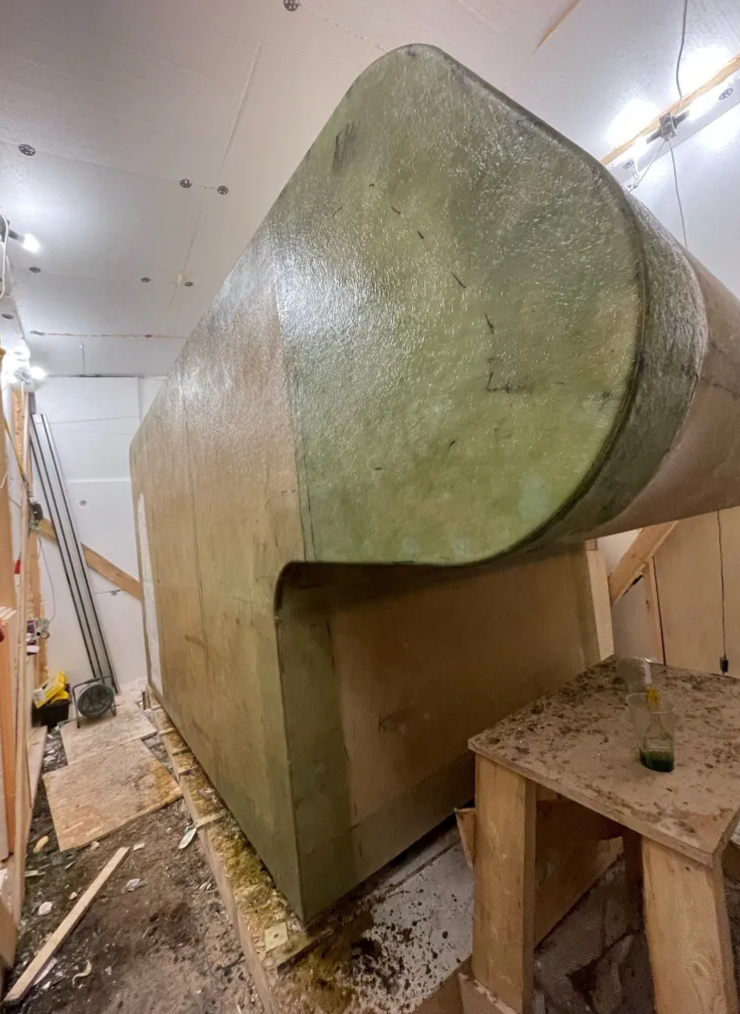
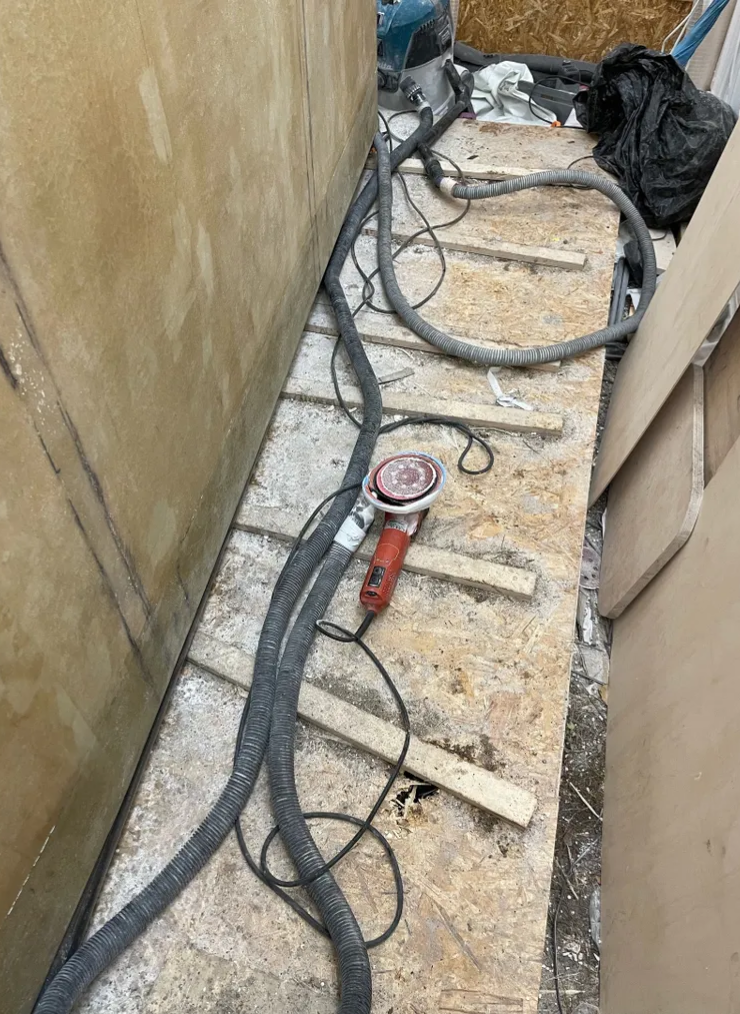
Когда смола застыла, весь модуль я отшлифовал абразивом р120. Шлифовал без фанатизма — надо только убрать торчащие волоски, наплывы и сильно выступающие дефекты, углубряться в полимер и убирать текстуру стекломата не надо — это ослабит полимерный кокон, так же очень аккуратно нужно шлифовать углы — их легко проточить и ослабить.
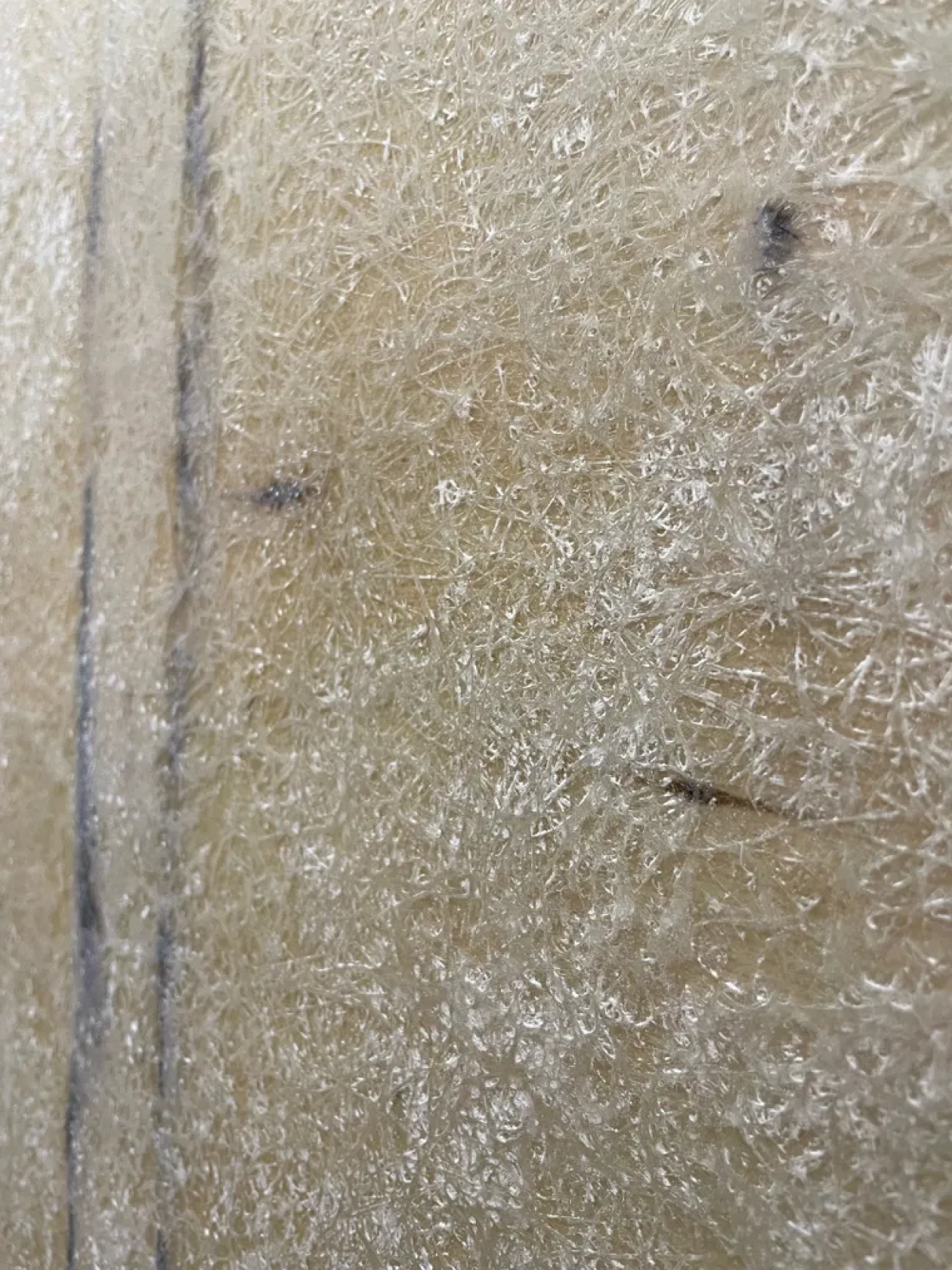
Затем модуль снова положили на бок, эти перевороты уже стали чем-то обыденным, и было отшлифовано днище, которое снова должно стать испытательным полигоном, теперь уже для гелькоута.
К этому моменту друзья у меня закончились (в переносном смысле, ближе к новому году в нашей сфере очень много работы, доделываются объекты и т.д, так что все постоянно заняты), а также начали заканчиваться деньги. Всё-таки два месяца стройки, когда я не работал, а тратил при этом сильно больше чем обычно, дают о себе знать. Сейчас нужно довести проект до какого-нибудь логичного этапа и в декабре придется немного денег подзаработать, но пока не об этом.
С гелькоутом я никогда не работал, да и маляр из меня прямо скажем никакой, но глаза боятся, а руки делают. В моем распоряжении было некоторое количество полиэфирной шпатлевки HB Body F250 Bodyfiber, которую я заказывал вместе с полиэфиркой и гелькоутом еще в самый первый заказ. Она представляет из себя довольно густую массу со стекловолокном, при добавлении отвердителя и замешивании становится более податливой и живет примерно 3-4 минуты, так что замешивать ее надо небольшими порциями. Я отшпатлевал небольшой кусок днища на 1 раз и небольшой кусок на 2 раза с промежуточной шлифовкой. Ушло примерно 1,5 банки из 3,5 которые у меня были. Примерно оценив расход, на ОЗОНе заказал еще много шпатлевки, такой и более мелкой текстуры — F220 Bodyfine. Все дно решил не шпатлевать, а просто покрыть гелькоутом.
Гелькоут по консистенции напоминает густой йогурт розвого цвета, после добавления 1% отвердителя и замешивания, он становится белым и более жидким, живет, как и полиэфирная смола примерно 15 минут — за это время подготовленный объем надо успеть нанести. Наносить его надо при температуре больше 16 градусов. У меня гелькоут для ручного нанесения, наносить его надо тонкими слоями с промежуточной сушкой между слоями порядка 40 минут. В финальный слой помимо отвердителя добавляется до 3% парафина в стироле, что перекрывает доступ кислорода к слою и он становится твердым, теряет остаточную липкость.
В начале я взял дешевые велюровые валики с ворсом 4мм, на каждый слой уходил один валик и в целом дно я покрыл, но как показала практика, неотшпатлеванную текстуру такой валик не перекрывает, остаются поры-краторы до самой полиэфирной смолы. Такого быть не должно, так как сама по себе смола гигроскопична и если в нее будет попадать влага, она будет ее впитывать. Слой гелькоута должен быть сплошной и цельный.
На дно попадать вода не будет, так что принято было решение дальше на него гелькоут не тратить, а локально задуть краской. Для этого был куплен балончик Раптора за 2750р, но порами оказалось покрыто все дно, кроме зашпатлеванных мест, так что раптора ни на что не хватило. Было принято решение купить недорогую молотковую эмаль и покрыть дно полностью, что хорошо держится на металле должно и на невпитывающем гелькоуте хорошо держаться.
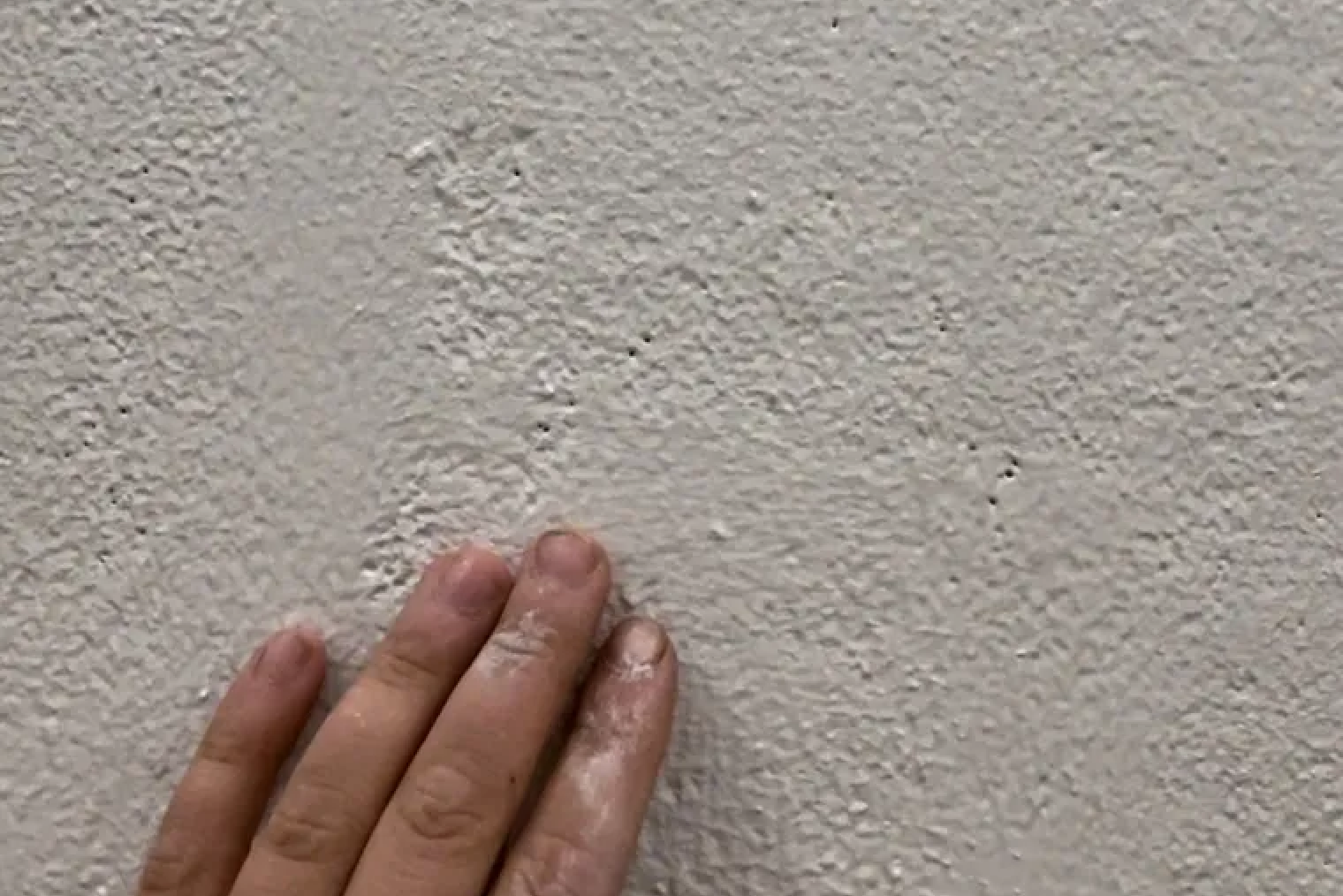
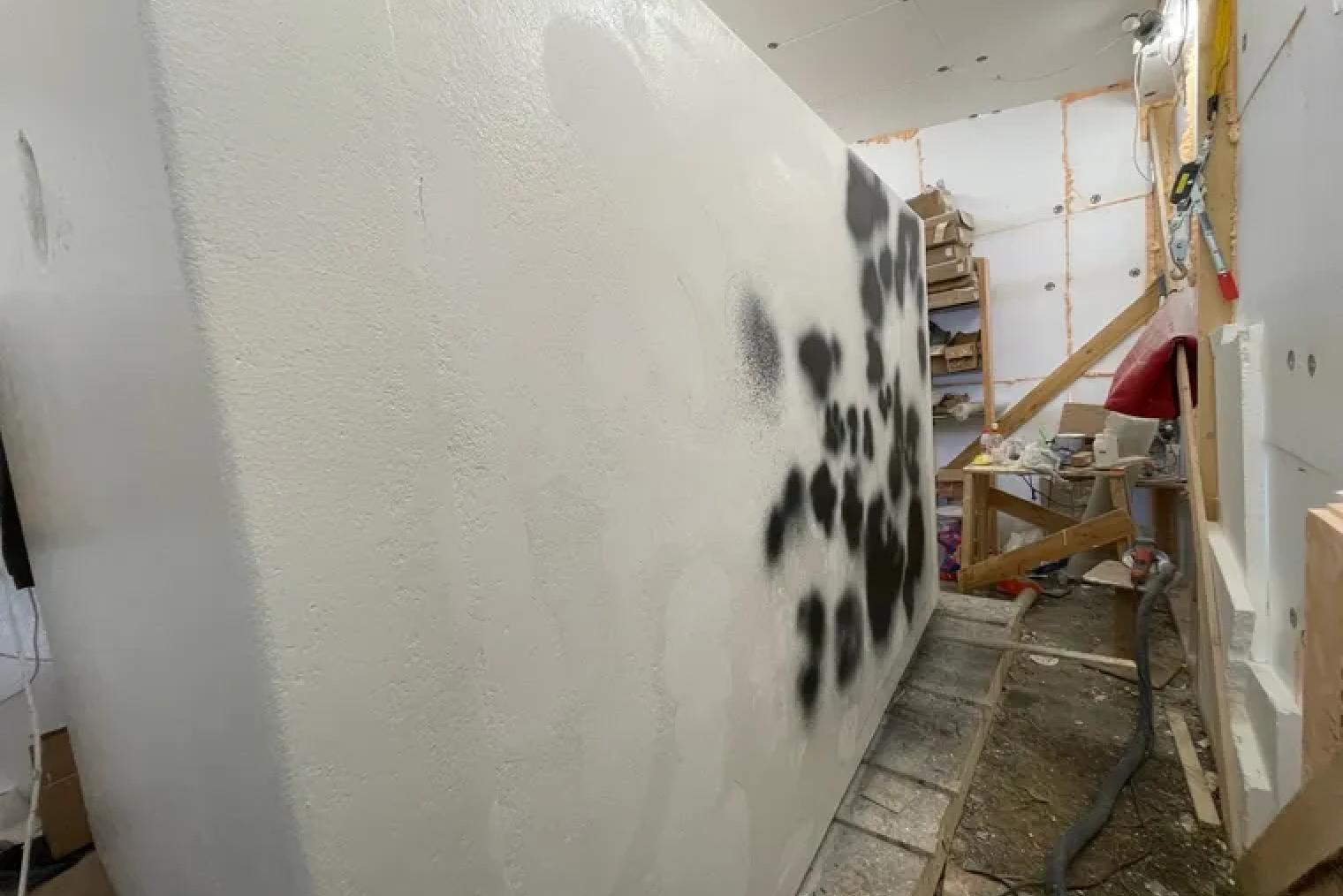
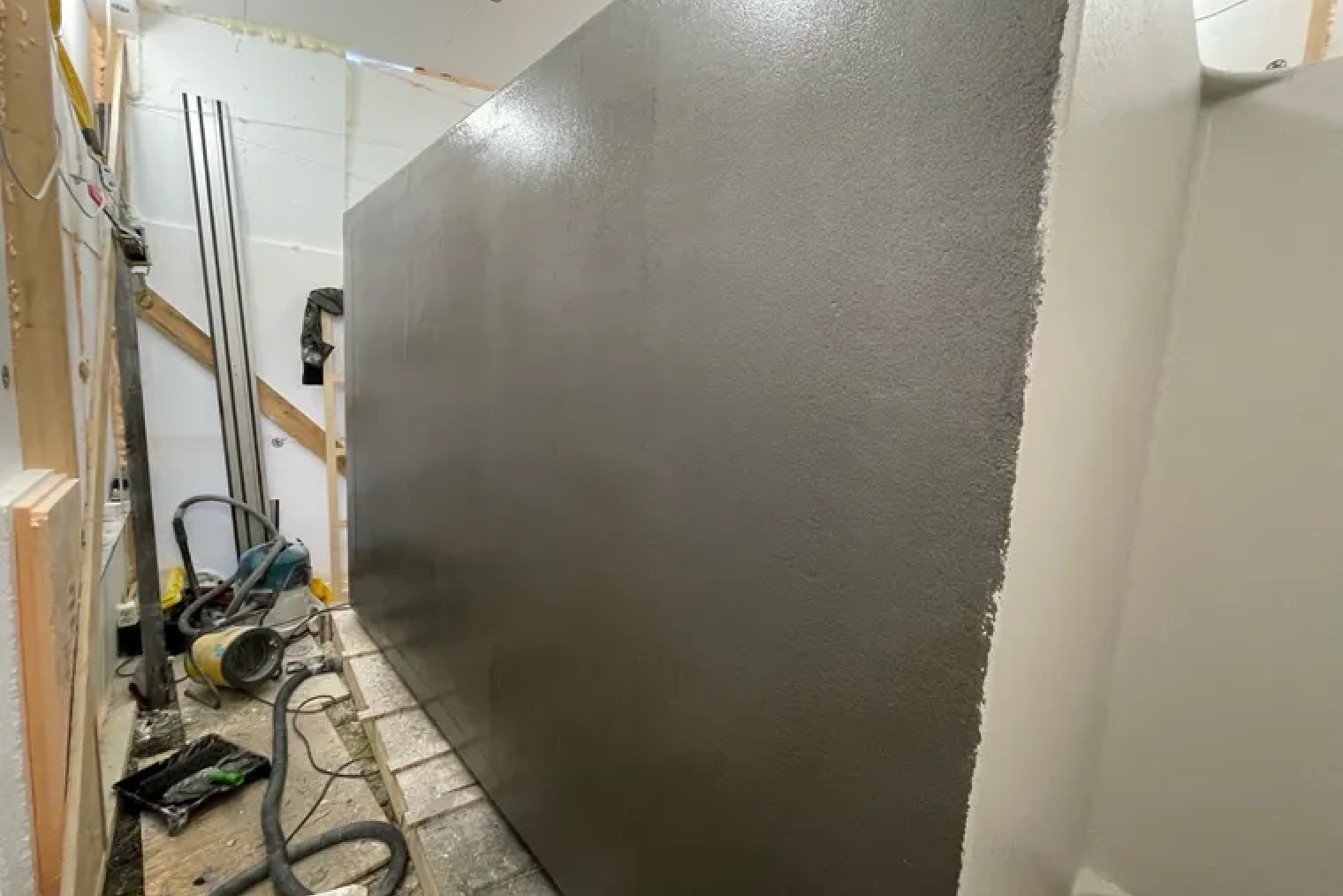
Поэкспериментировав с дном, я готов был переключаться на остальную часть модуля, к тому времени приехала и заказанная шпатлевка. Я пробовал разные варианты шпатлевания — например сперва на сплошную шпатлевать BodyFiber, а затем после шлифовки давать слой Bodyfine. Однако опыт показал, что Bodyfiber подходит только для заделки больших ям, отведения перепадов и прочего, где нужно дать слой, но плохо заполняет текстуру, в итоге расход очень большой, а большая часть в итоге просто сошлифовывается, обнажая текстуру. Тогда Бодифайбером я стал только отводить углы и перепады в местах нахлеста стекломата, а все остальное по плоскости шпатлевать Бодифайн — она более податливая, заполняет все перепады и расход ее выходит в итоге значительно меньше.
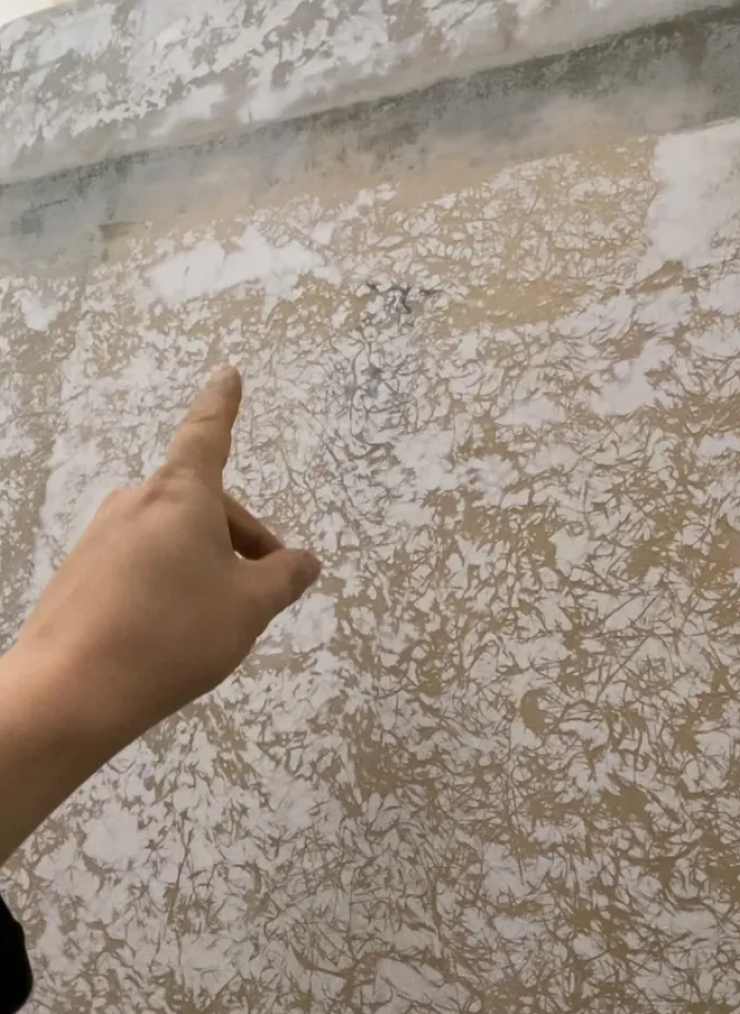
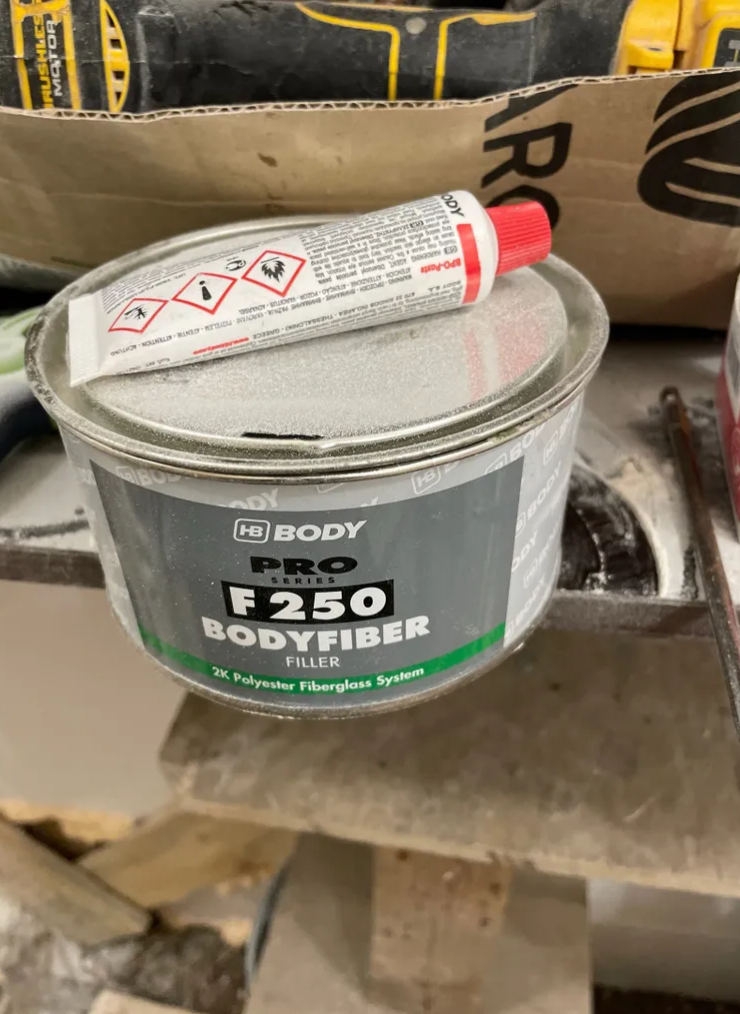
Для теста было закуплено большое количество валиков из разного материала и разной ворсистости. Все дешевые валики одинаково плохи, с них лезет ворс и катают они неравномерно, но умирает валик примерно за 15 минут, т.е на слой у меня уходит 3-4 валика, а во время «обучения боем» выходило и того больше. По факту лучше всего себя показали валики из полиакрила с ворсом 18 миллиметров. Их я нашел в большом количестве в Леруа за 114 р/шт и купил там все. Для сравнения такой же валик в Петровиче стоит 260р, а в максидоме и того больше.
Подход использовал такой же как со смолой — гелькоут замешивал в стакончиках по 400 грамм, на ванночку для валика надевал мешок для мусора и катал. Но выяснились некоторые нюансы — один стаканчик в ванночку вываливать бесполезно, он теряется в валике и размазывается по пакету, если замешать два стаканчика и их раскатать, то валик вроде еще жив, но пока мешаешь третью порцию он схватывается и умирает. В общем не буду рассказывать все многочисленные итерации моей работы с материалом, расскажу уже правильную схему работы, к которой я пришел.
4 нанесенные слоя были сомнительного качества — было много катышек от валика и вставшего в процессе экспериментов материала. Все это дело я отшлифовал зерном р120-150, не глубоко, сняв только катышки и большие неровности, затем обеспылил и обезжирил. Для замешивания на ОЗОНе были заказаны маленькие венчики для шуруповерта, сам же шуруповерт был замотан в стрейч-пленку, чтобы он выжил.
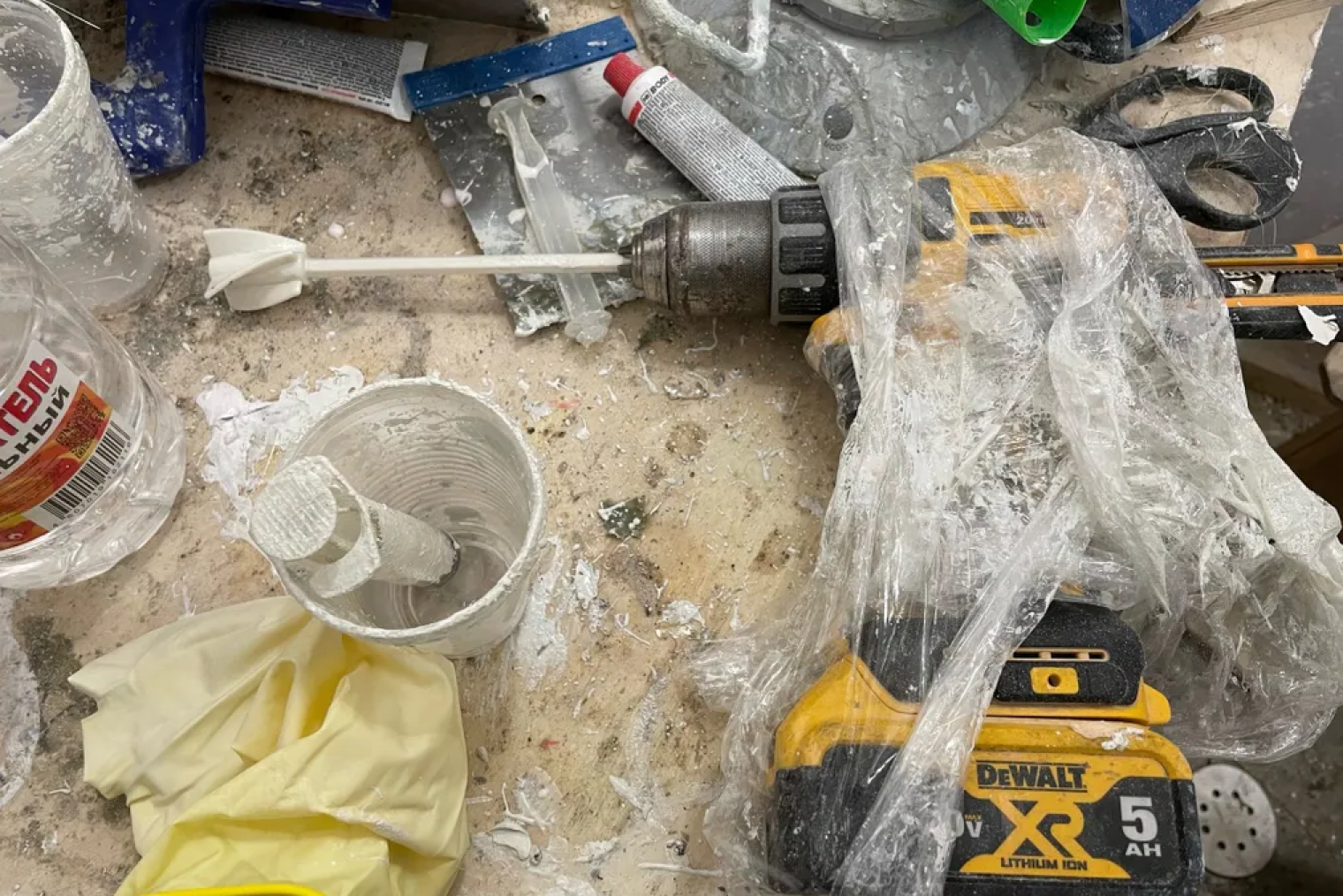
За счет механизации замеса получилось быстро делать сразу 3 стаканчика материала (1200 грамм) и его наносить. Возможно получится даже 4, но это надо пробовать. После нанесения валик меняется на новый, как и пакет на ванночке, после этого замешиваю новую партию материала. С таким подходом все получилось, слой получился равномерный без катышек и больших косяков, при этом ушло на слой всего 4 валика. Поверхность фактурная, с шагренью, напоминает раптор. Такой результат мне и был нужен.
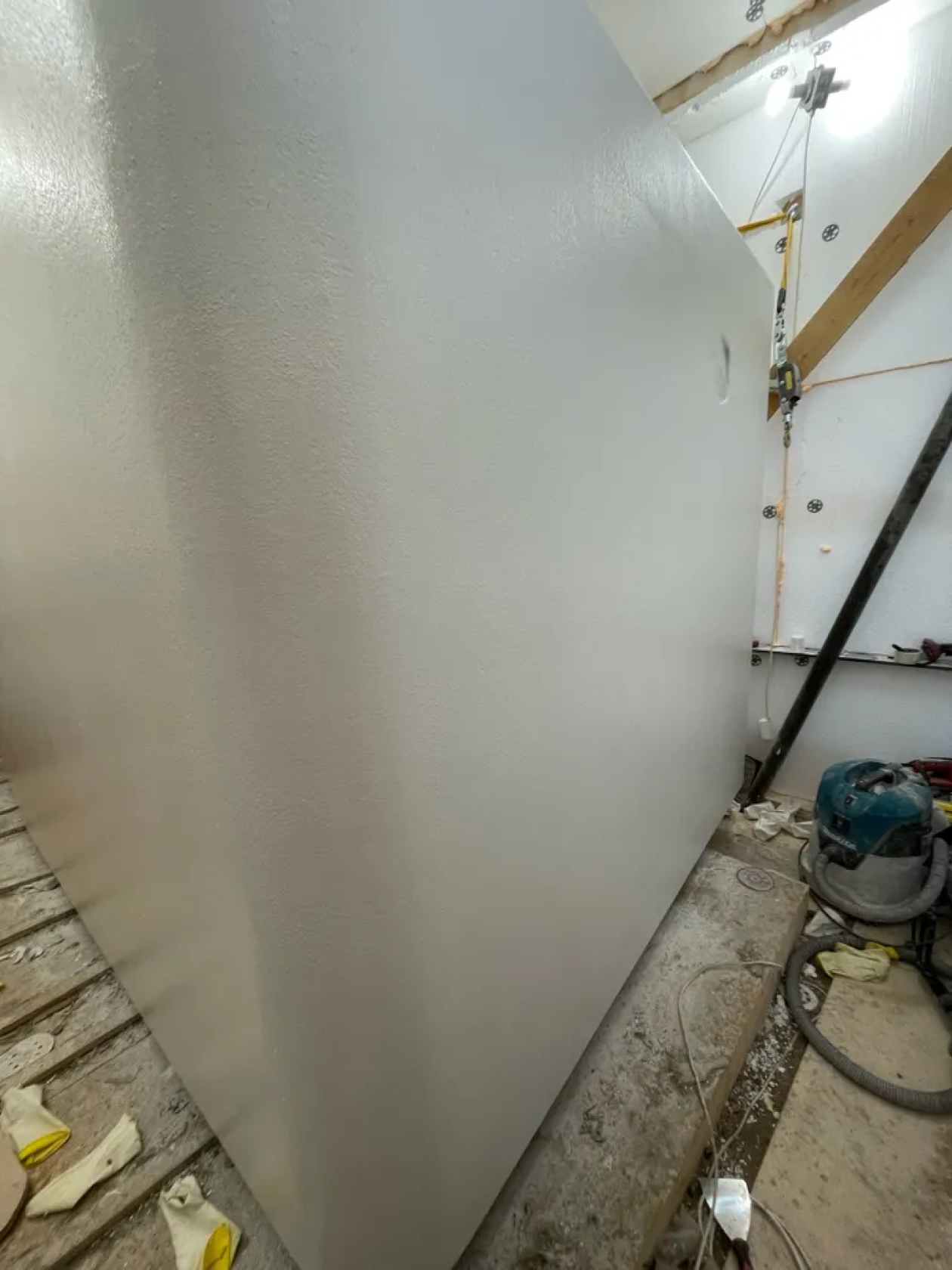
По нюансам — значительные перепады гелькоут не перекрывает, вернее он никакие перепады не перекрывает, а только подчеркивает, так что какой геометрия будет после шпатлевки — такой она и останется. У меня, например, местами видны нахлесты стекломата, но на крыше это не критично — боковые стены буду шпатлевать внимательнее.
Гелькоут довольно хорошо шлифуется и после шлифовки слой ложится проще и равномернее, так что оптимальный подход на мой взгляд сейчас — набрать 4 основных слоя толщины дешевыми валиками, дать высохнуть и шлифануть косяки, а затем сделать финишные 1-2 слоя хорошими дорогими валиками, так должен получиться хороший результат.
Но узнаем, насколько хорош этот план мы уже в следующий раз, так как в очередной раз закончилось вообще все — гелькоут, отвердитель, парафин в стироле. Это все было заказано в очередной раз в Москве и отправлено с большой задержкой. Заказал еще и полиэфирной смолы — по такой же технологии сделаю душевую.
Вся эта логистика с химией начинает уже бесить. В ремонтах квартир никогда нет такого, что что-то нельзя докупить завтра, а расход всего примерно понятен, а тут эти заказы, доставки, транспортная компания, ух!
Но нет худа без добра, пока модуль лежит на боку я решил утеплить крышу, и уже на этапе обработки огнебиозащитой, оказалось, что это чертовски правильная идея. Сейчас в альков и багажное отделение можно зайти в полный рост и ко всему есть доступ, но все равно брызги летят во все стороны и ты весь красный, а что бы было, если бы обрабатывать это все нужно бы было на потолке, согнувшись в три погибели в багажном отделении, или лежа на кровати?
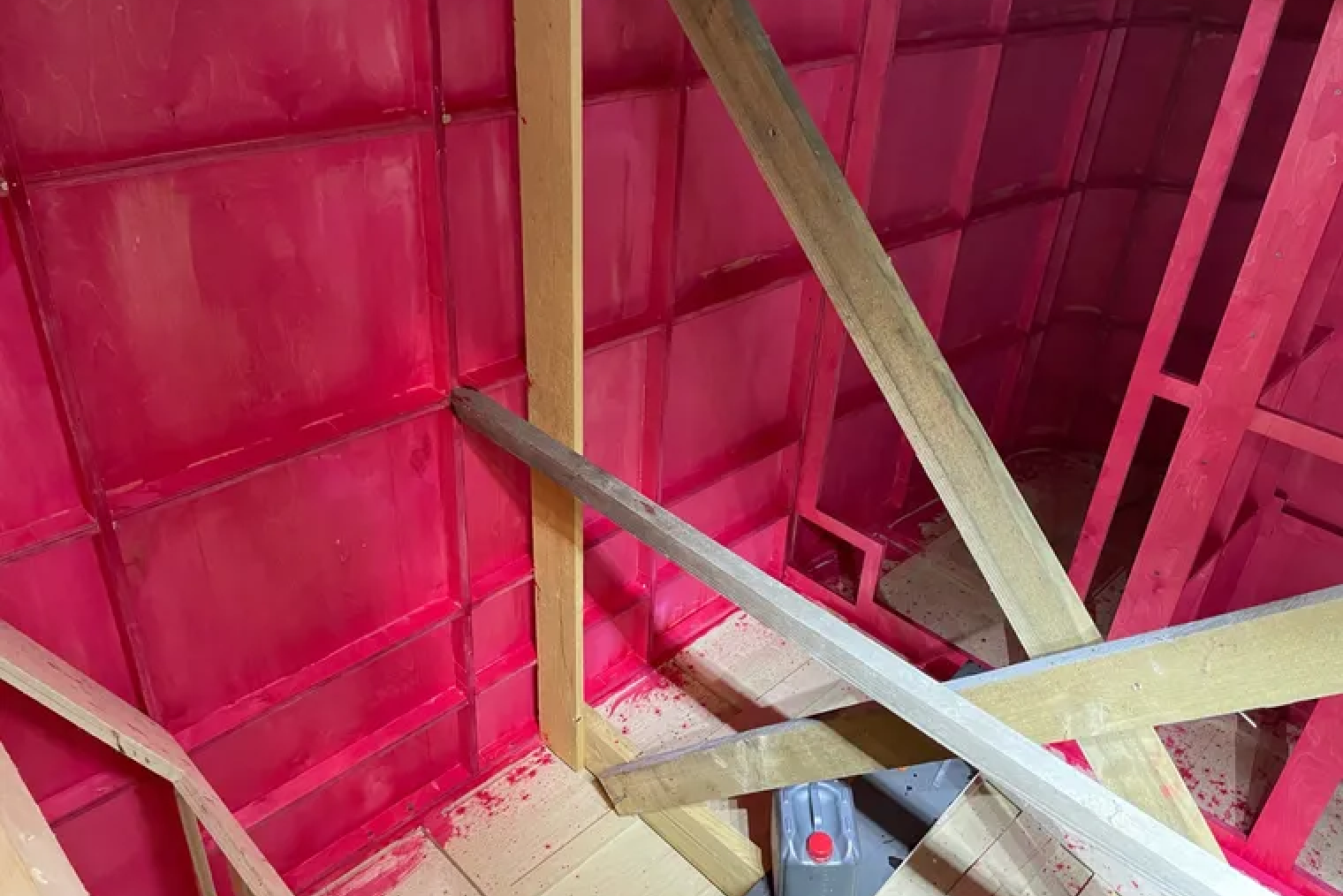
Я до конца не уверен в необходимости огнебиозащиты как таковой — если обеспечить хорошую пароизоляцию, круглогодично автодом топить, либо хранить в теплом помещении и хорошо вентилировать, то обработка фанере как таковая и не требуется — не будет там влажности, но будут ли условия всегда идеальными? Это большой вопрос. Так что лишней огнебиозащита точно не будет, к тому же она дополнительно запечатает ФСФ фанеру, которая не очень для человека полезна, и хотя и не будет контактировать с внутренним помещением, но все же будет нагреваться при эксплуатации и неизвестно насколько геметично будет закрыта.
Утеплять модуль буду PIR-плитой, она почти в три раза дороже обычного ЭППС типа Пеноплекс, но полностью негорючая и не выделяет никаких веществ, так как предназначена для бань. Пеноплекс же исключительно фасадно-фундаментный материал, довольно токсичный, и в помещении, особенно которое солнцем будет нагреваться, лично у меня нет желания его использовать.
Плиты крою большим ножом с лезвием 25мм, одной плиты хватает на два сектора, отходов и обрезков получается очень мало. Нюанс заключается в том, что крыша не одинаковой толщины — в центре 7 сантиметров и постепенно снижается к краям модуля до 5 сантиметров, плита же вся 5 сантиметров и расстояние под ней желательно полностью заполнить, чтобы не было воздушных карманов. Сперва попробовал использовать для этой цели напыляемый утеплитель полинор. Мне не очень понравилось — очень большой расход, пачкает все вокруг и при расширении давит плиту так, что как я не фиксировал — выдавил за плоскость на сантиметр. А ПИР-плиту нельзя просто сошлифовать как обычный пеноплекс из за фольгированного слоя, что несомненно добавит геморроя в будущем — что буду делать пока не решил.
В целом вариант рабочий, но нужно наносить по-меньше напыляемого ППУ и жестко фиксировать панель не тонкими полосками фанеры, а прямо какими-то брусками или профилями. Так же неизвестно как он полимеризуется в отсутствии кислорода.
Оставшиеся элементы монтировал уже на клей-пену, фиксируя по углам секторов небольми кусочками фанеры, а в перепады просто добавляю больше пены. Клей-пена не сильно расширяется и плиту уже не давит, но все равно местами выдавила середину на 3-5 миллиметров. В общем к утеплению я плохо подготовился — нужно было взять что-то вроде профилей для гипсокартона, сделать много заготовок, которыми после монтажа кусков панели их жестко временно прикручивать, чтобы не выдавливало, тогда бы плоскость будущего потолка сохранилась, а так придется проводить какие-то дополнительные мероприятия по выравниванию.
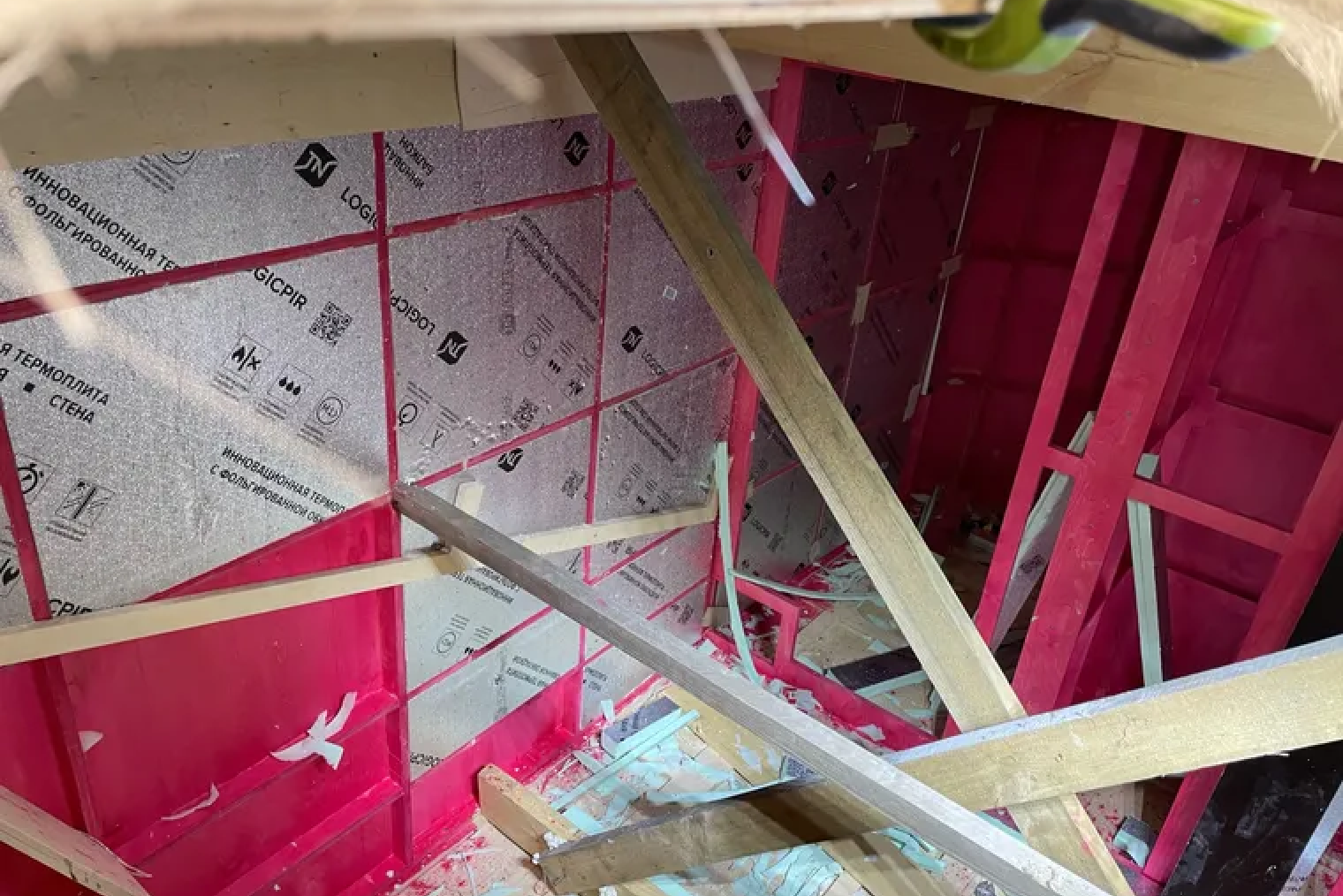
Острые японские лезвия для ножа Olfa к концу дня сыграли со мной злую шутку. Уже подустал, внимание рассеялось, пена давила и торопился сделать и закрепить последние кусочки панели. Нож прорезал панель, сорвался и полоснул по штанам чуть выше наколенника. Сопротивления он не встретил никакого, прорезал и штаны и кожу. Не глубоко, в травмпункте шить не стали, но разрез стянули специальным пластырем и несколько дней теперь нельзя сгибать ногу в колене, чтобы не разошлась, что работать не позволяет, потому что вся работа над модулем связана с постоянным лазанием и приседанием. Так что теперь нужно еще и раны залечивать.
На следующей неделе планирую окончательный переворот модуля, шпатлевку и покрытие гелькоутом оставшихся боковых стенок. Дальше можно будет установить окна, двери, навесное оборудование и это будет конец осенней компании по работе над модулем, так как нужно будет сделать перерыв и заработать немного денег.
Расходы на текущий этап
- Гелькоут полиэфирный NOAGEL ISO NPG VB 62,4 кг — 50856р
- Шпатлевка полиэфирная HB Body — 13274р
- Дополнительный отвердитель, парафин в стироле — 2235р
- Раптор — 2790
- Краска для днища модуля — 2575
- Стаканчики, венчики, перчатки в ОЗОНЕ — 4144р
- Все закупки в Петровиче, в основном это расходка — клей-пена, валики, шлифматериал, огнебиозащита и т.д. — 21867р
- Pir-плита 50мм для утепления крыши а алькова — 22527р
- Мелочевка в Максидоме — 4273р
- Такси и транспорт — 13999р
- Бензин для автономки 4260р.
Итого: 142 800р.
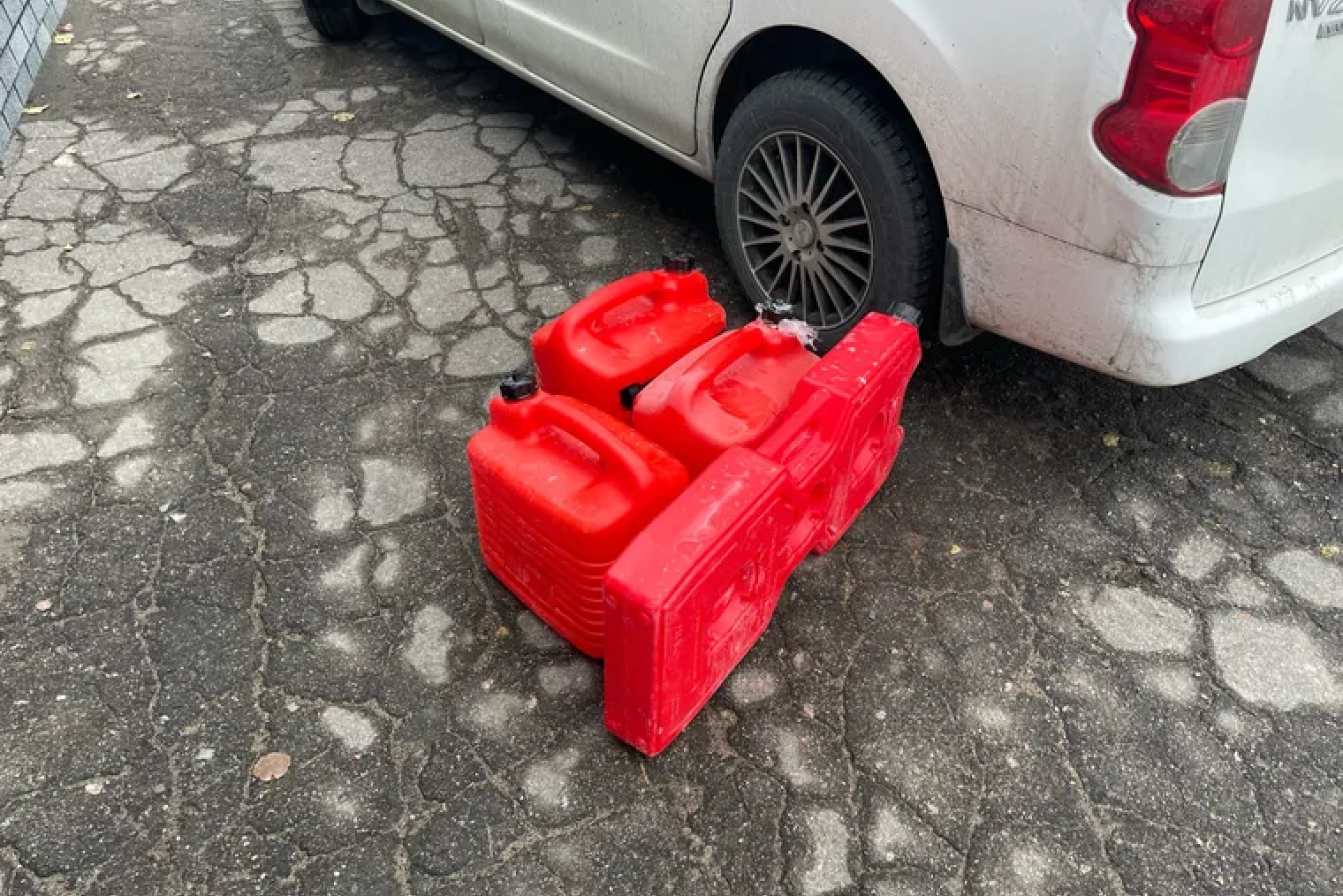
Еще 13 человеко-дней потрачено на текущий этап. Так же я стал немного экономить топливо, чтобы не заниматься лишний раз его заправкой. Чтобы не размораживать сарай когда нет ответственных работ, оставляю только электрическую дуйку на 1,5 киловатта, она нажигает примерно на 360р в сутки, но зато ее не надо постоянно заправлять, при этом температура в сарае порядка 13 градусов. Бензиновую же автономку включаю только когда прихожу работать и когда надо поддерживать 20 градусов для полной полимеризации материалов.