«Специфика бизнеса отпугивала инвесторов»: как я потерял 10 млн рублей на производстве ведер
История читателя
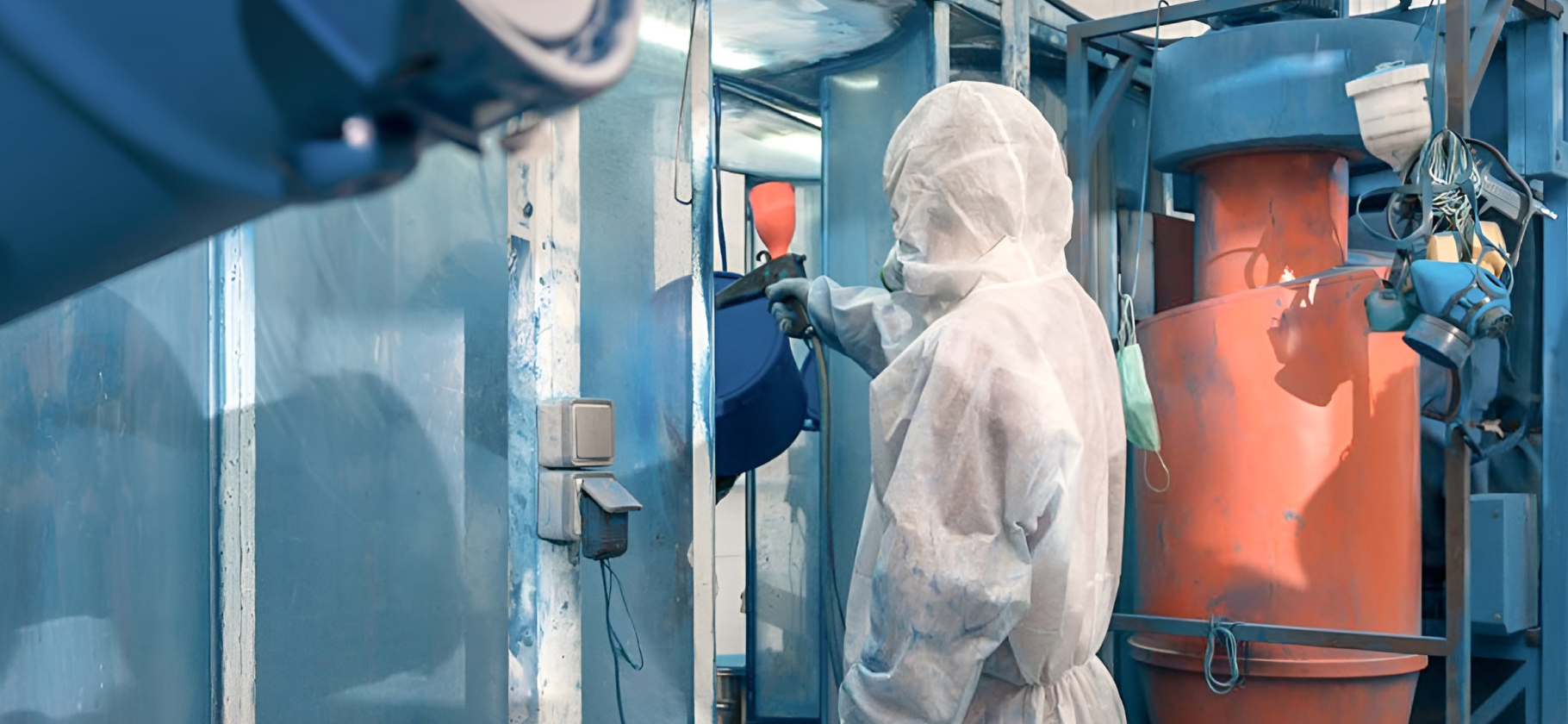
Читатель Тинькофф Журнала набрался опыта в производственной компании и открыл свое предприятие.
Чтобы начать выпуск ведер для краски и лака, он потратил больше 15 млн рублей: привлек опытных коллег, купил оборудование и нашел клиентов. Но возникли непредвиденные проблемы, которые в итоге привели к простою и закрытию проекта.
Герой рассказал, как дефицит сырья может повлиять на целую сферу и что бы он делал сейчас, чтобы сохранить свое дело.
Это история из Сообщества. Редакция задала вопросы, бережно отредактировала и оформила по стандартам журнала
Идея бизнеса
Я решил основать бизнес в 2020 году, когда мне было 27 лет. На тот момент я уже более двух лет занимал место руководителя планово-экономического отдела на крупном предприятии в Уфе, где трудилось около тысячи человек. Одним из видов деятельности фирмы было производство металлической тары объемом 26—52 л для лакокрасочной продукции.
В какой-то момент руководство компании решило сосредоточиться на направлении, на которое приходилось около 80% оборота, и прекратить производство тары. К этому времени у меня уже сформировалось желание попробовать себя в роли предпринимателя, поэтому я начал общаться с ключевыми сотрудниками, чтобы оценить потенциал такого бизнеса.
Руководитель отдела сбыта сообщил мне, что спрос на тару такого объема упал, потому что многие производители лакокрасочной продукции перешли на использование емкостей объемом 12—21 л, известных как евроведро с крышкой типа «корона». А главный инженер оценил имеющееся на предприятии оборудование как устаревшее.
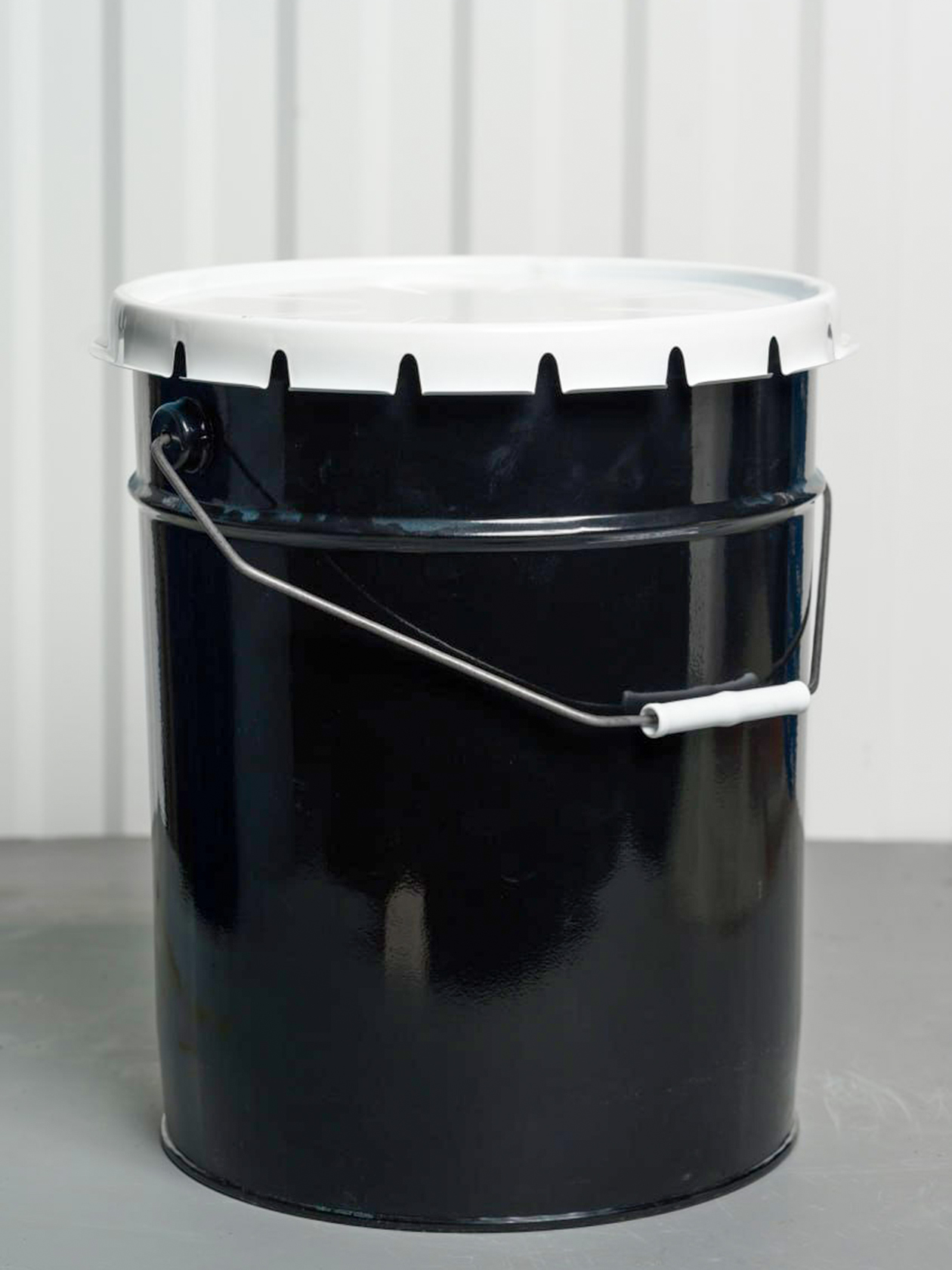
Если раньше я не исключал возможности возглавить направление по выпуску емкостей, то после беседы с сотрудниками понял, что это не лучшая идея. Поэтому я решил заняться производством евроведер самостоятельно, ведь моя продукция будет похожа на ту, что выпускал мой прежний работодатель, а покупателями евроведер станут те же лакокрасочные заводы. С поддержкой работников тарного направления можно было бы быстро выйти на рынок.
Чтобы оценить потенциал проекта, я посчитал себестоимость производства одного ведра на 20 л: при затратах в 118 ₽ я мог бы продавать его за 148 ₽. На основе этих данных я составил бюджет доходов и расходов. Этот процесс мне был уже знаком: подобные задачи входили в мои обязанности на предыдущей работе.
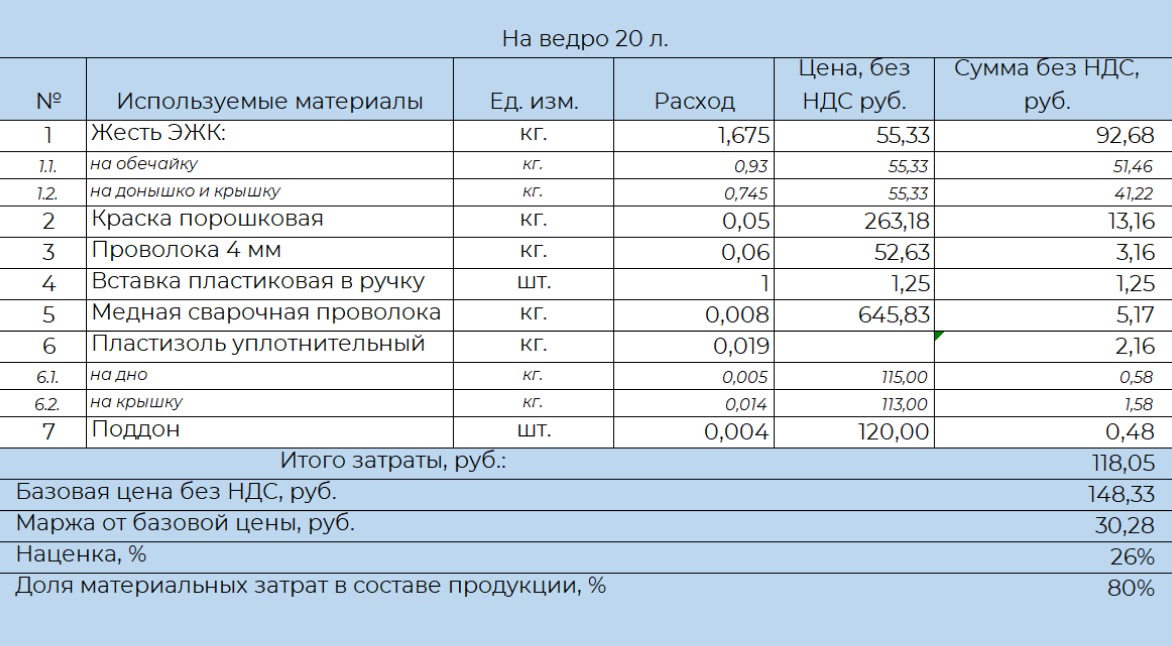
При выпуске 60 000 изделий в месяц я бы получил около 650 000 ₽ операционной прибыли без учета производственных, административных и коммунальных затрат. Но в моем понимании такая сумма с лихвой покрыла бы эти расходы.
Для запуска бизнеса я опирался на свое понимание экономики проекта и особенностей рынка — я знал, кому и в какие регионы смогу продавать изделия. Также я собирался трудоустроить команду специалистов с предыдущей работы: руководитель отдела продаж, главный инженер и электрик-механик искали новое место после закрытия тарного направления.
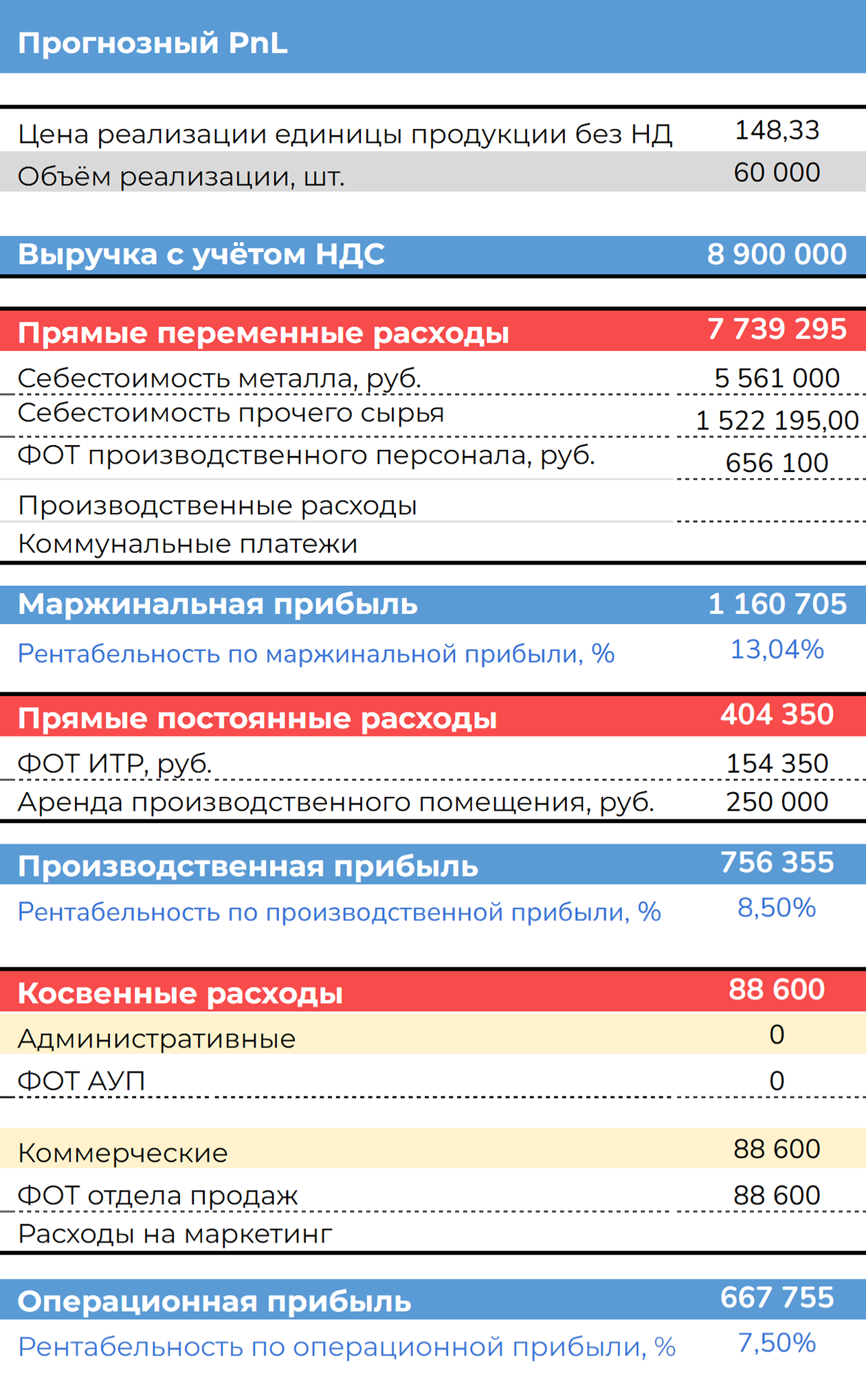
Поиск и покупка оборудования
Оборудование для выпуска евроведер — это полуавтоматическая производственная линия из станков, которые последовательно обрабатывают заготовку. Также бывают автоматические линии, но о них речь в моем случае не шла: слишком затратно.
В России производителя такого оборудования не оказалось. Я обращался и к китайским дистрибьюторам, и к представителю турецкого завода-изготовителя, которых нашел в интернете. Производительность полуавтоматической линии у всех поставщиков была одинаковая — около 400 единиц продукции в час, а вот цены на оборудование из Китая были ниже в полтора раза.
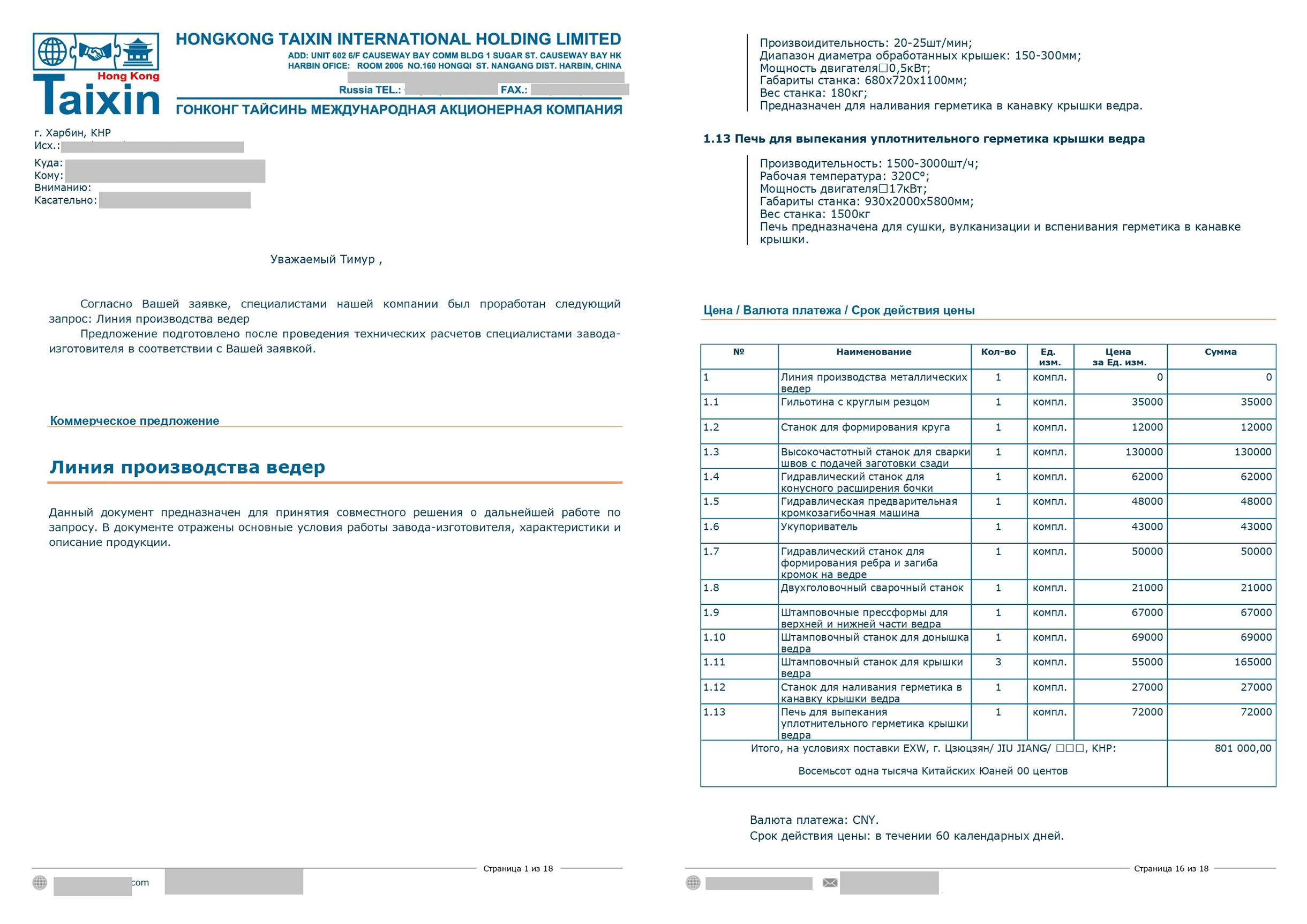
Стоимость нового оборудования оказалась слишком высокой, а ждать поставки пришлось бы четыре месяца, поэтому я начал искать варианты на «Авито». Там я обнаружил объявление о продаже подержанной производственной линии за 6 млн рублей в полном составе.
Звонок, запрос технических паспортов — и уже через несколько дней мы с коллегой-электромехаником летели в Волгоград осматривать станки.
- 6 млн рублей
- стоимость подержанной полуавтоматической производственной линии
Как оказалось, продаваемое оборудование со всеми активами было выкуплено у завода, который производил евроведра, не использовалось уже около пяти лет и стояло аккуратно законсервированным в углу. Что оно из себя представляло:
- Линия по производству конической тары, так называемых евроведер, объемом 15—20 л.
- Линия по производству цилиндрических бочек объемом 50 л.
- Линия нанесения порошкового покрытия и печь полимеризации конвейерного типа.
После проверки документов и работоспособности техники мне удалось договориться с продавцом на небольшую рассрочку платежа. Мы подписали договор, я внес задаток и пообещал вернуться и забрать линию после подготовительных работ в Уфе: мне нужно было найти помещение и зарегистрировать юрлицо.
Спустя месяц мы тем же составом прибыли в Волгоград для отгрузки оборудования. За транспортировку линий тремя фурами я заплатил 240 000 ₽.
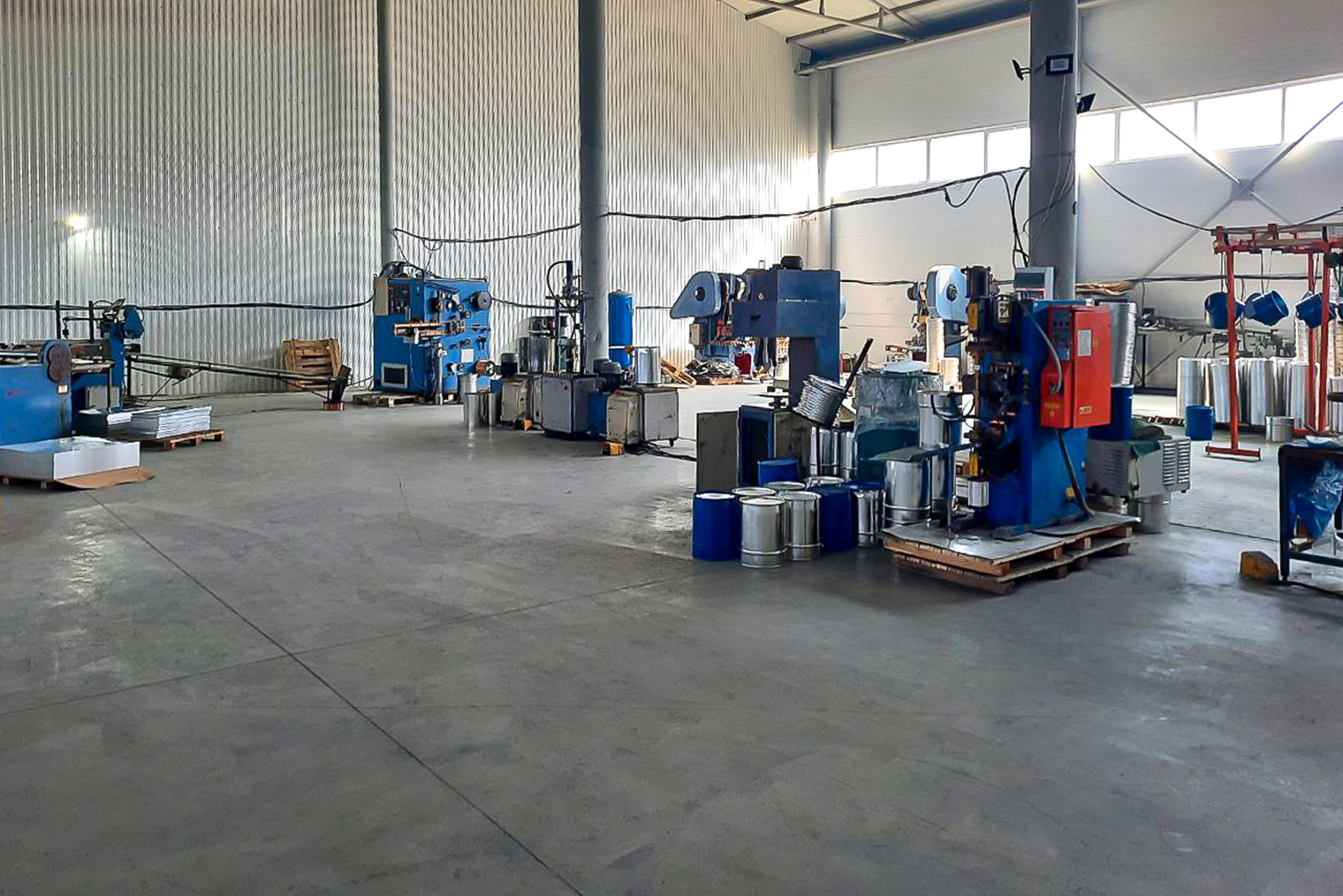
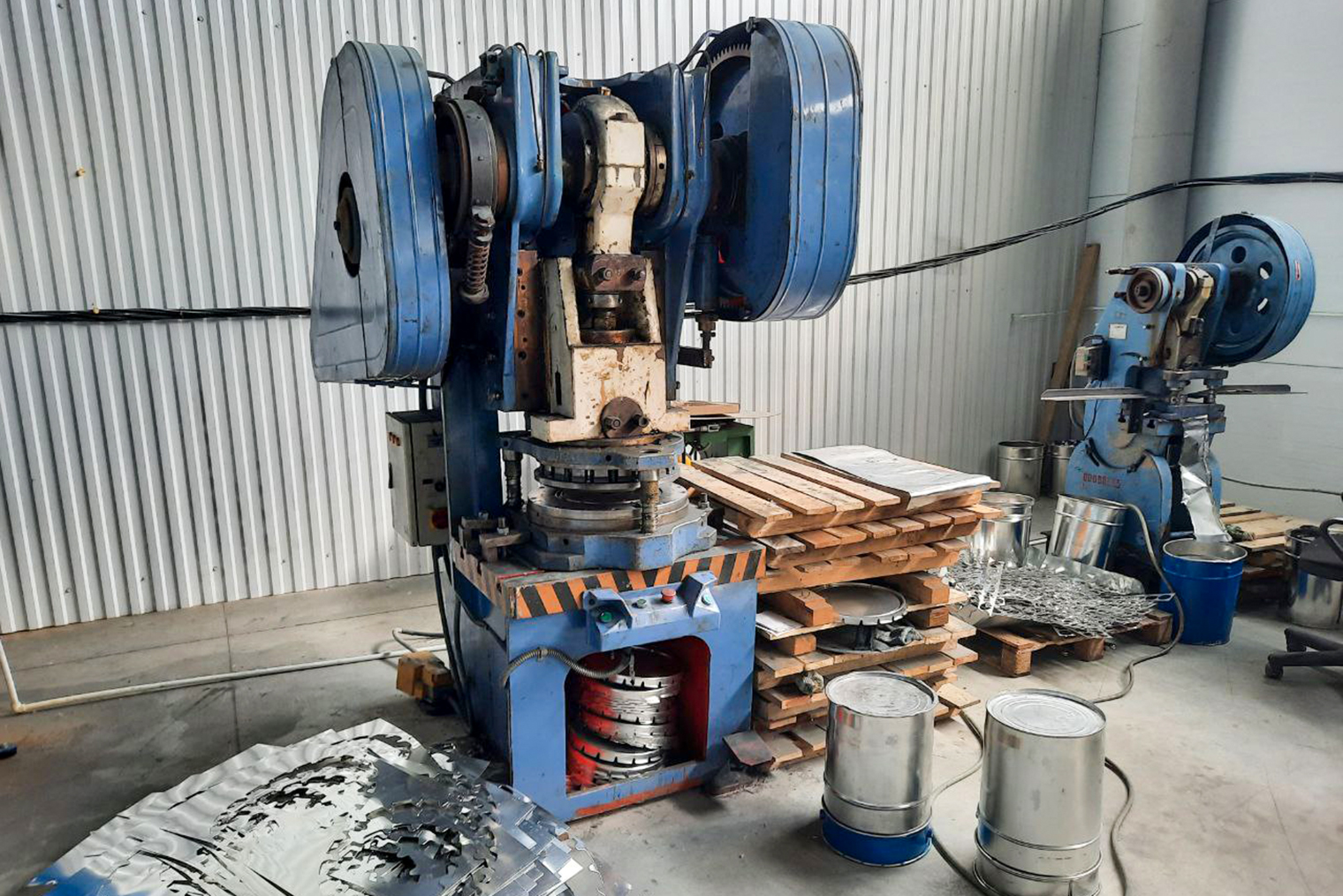
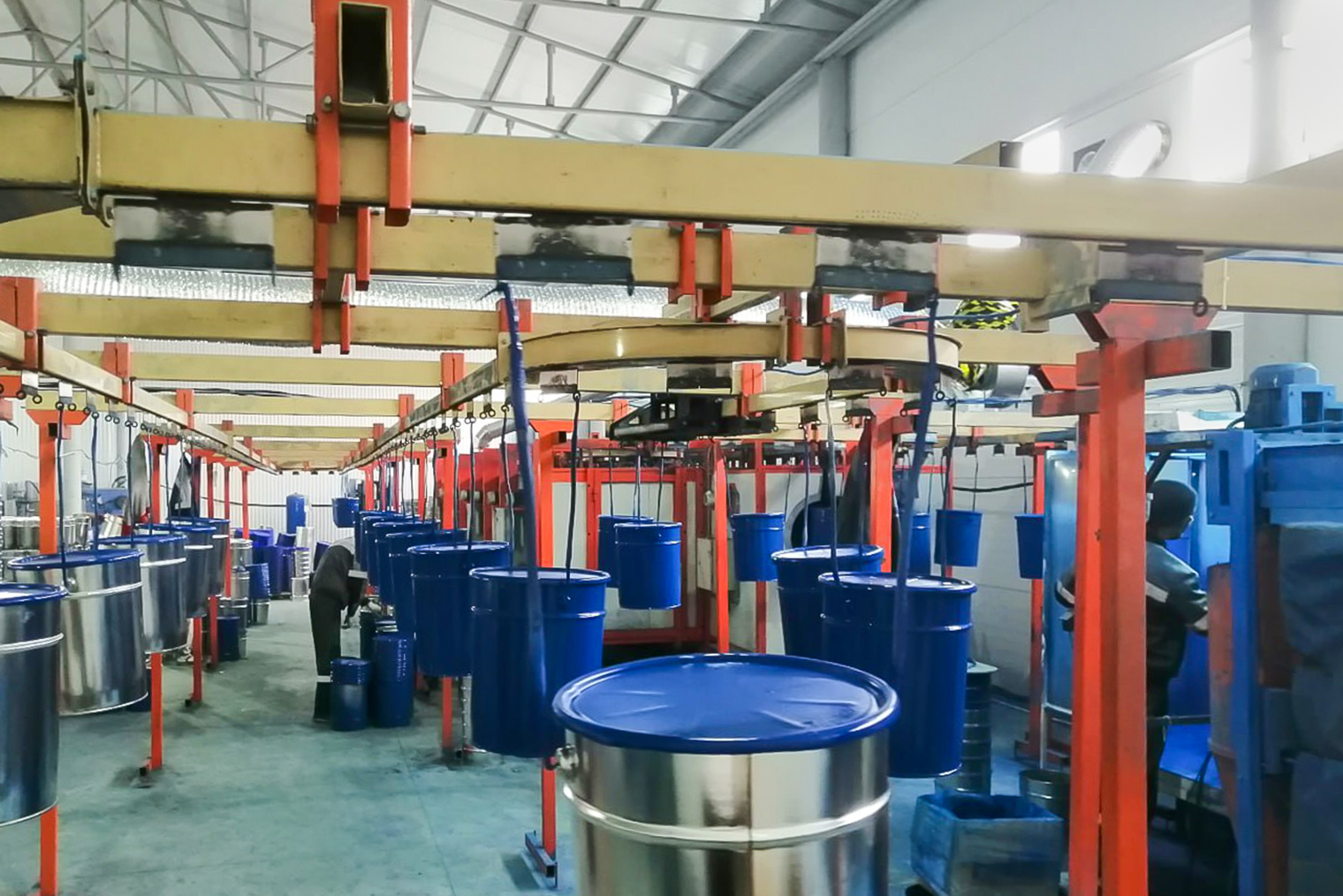
Открытие компании
Для стабильной работы оборудования требовалась электролиния мощностью 200 кВт. В начале июля 2020 года я нашел подходящее помещение площадью 1000 м² и арендовал его за 250 000 ₽ в месяц. Также договорился на двухнедельные арендные каникулы. Еще около 250 000 ₽ ушло на строительство бытовых и офисных помещений внутри цеха.
Получив гарантийное письмо от арендодателя о том, что он предоставит мне помещение в качестве юридического адреса, я зарегистрировал ООО. Поскольку моими потенциальными покупателями были крупные производственные предприятия, не применяющие специальные налоговые режимы, я оставил общую систему налогообложения. Сделал это, чтобы выписывать счет-фактуры и предоставлять своим клиентам возможность налогового вычета по НДС.
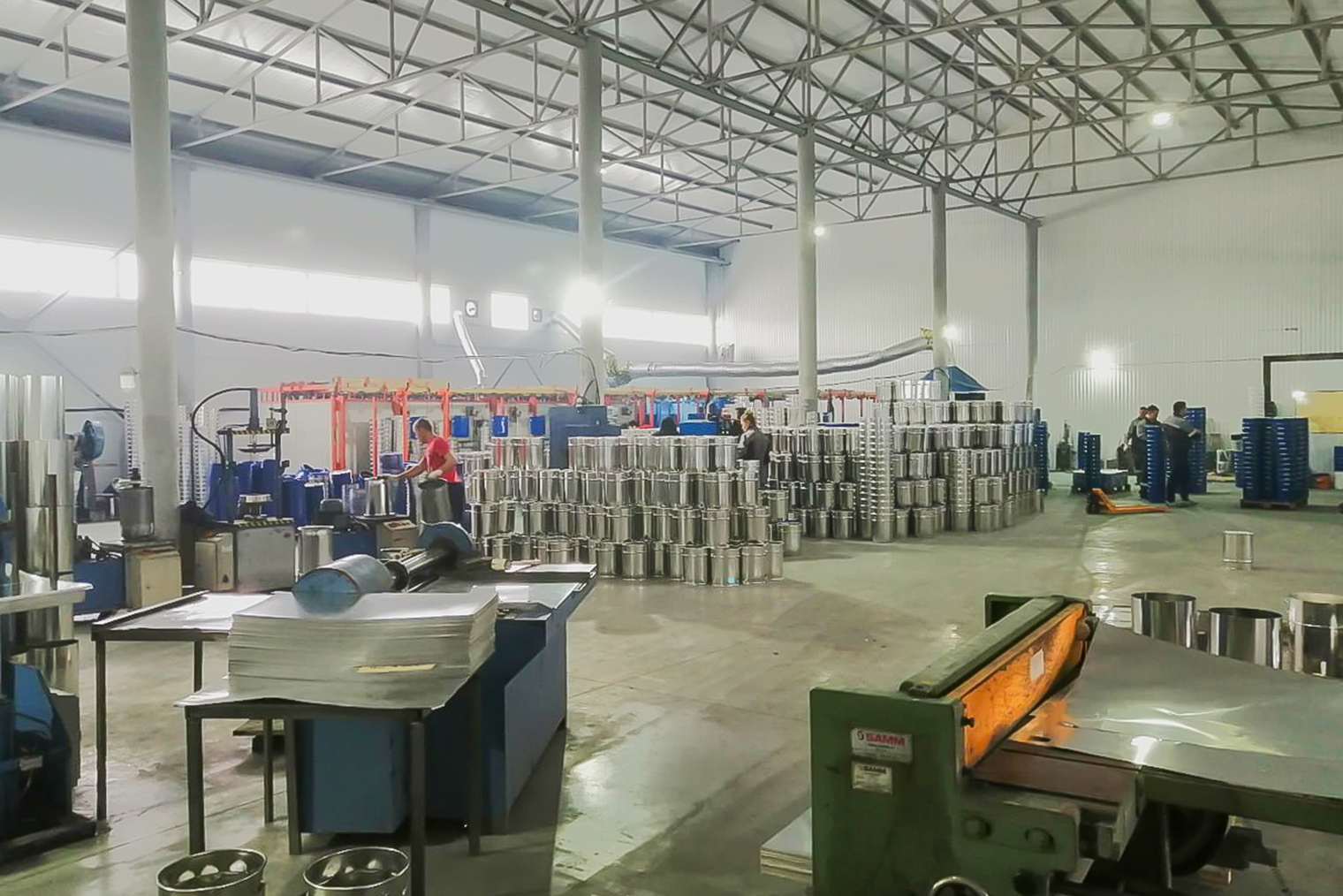
Тесты и производство
Инженерно-технические работники и административно-управленческий персонал были сформированы за счет освободившейся команды с моей прежней работы, нужно было только набрать сотрудников на производственные линии. Мы подали объявление о наборе персонала еще на стадии пусконаладочных работ, длившихся две недели. Когда мы закончили, у нас было 10—12 слесарей, которые стали посменно трудиться на станках.
В это время мы заказали пробную партию сырья на полторы тонны, из которого изготовили образцы. Часть ведер мы испытывали сами: заполняли песком и подвешивали на сутки за ручку, набирали в них воды и ставили друг на друга в несколько рядов, затем сбрасывали с небольшой высоты. Другую часть мы отправили на проверку клиентам. Образцы ушли в 35 организаций, замечания были только у двух-трех из них.
В итоге мы запустили производство, но, к сожалению, не вышли на плановый объем выпуска в 60 000 единиц в месяц.
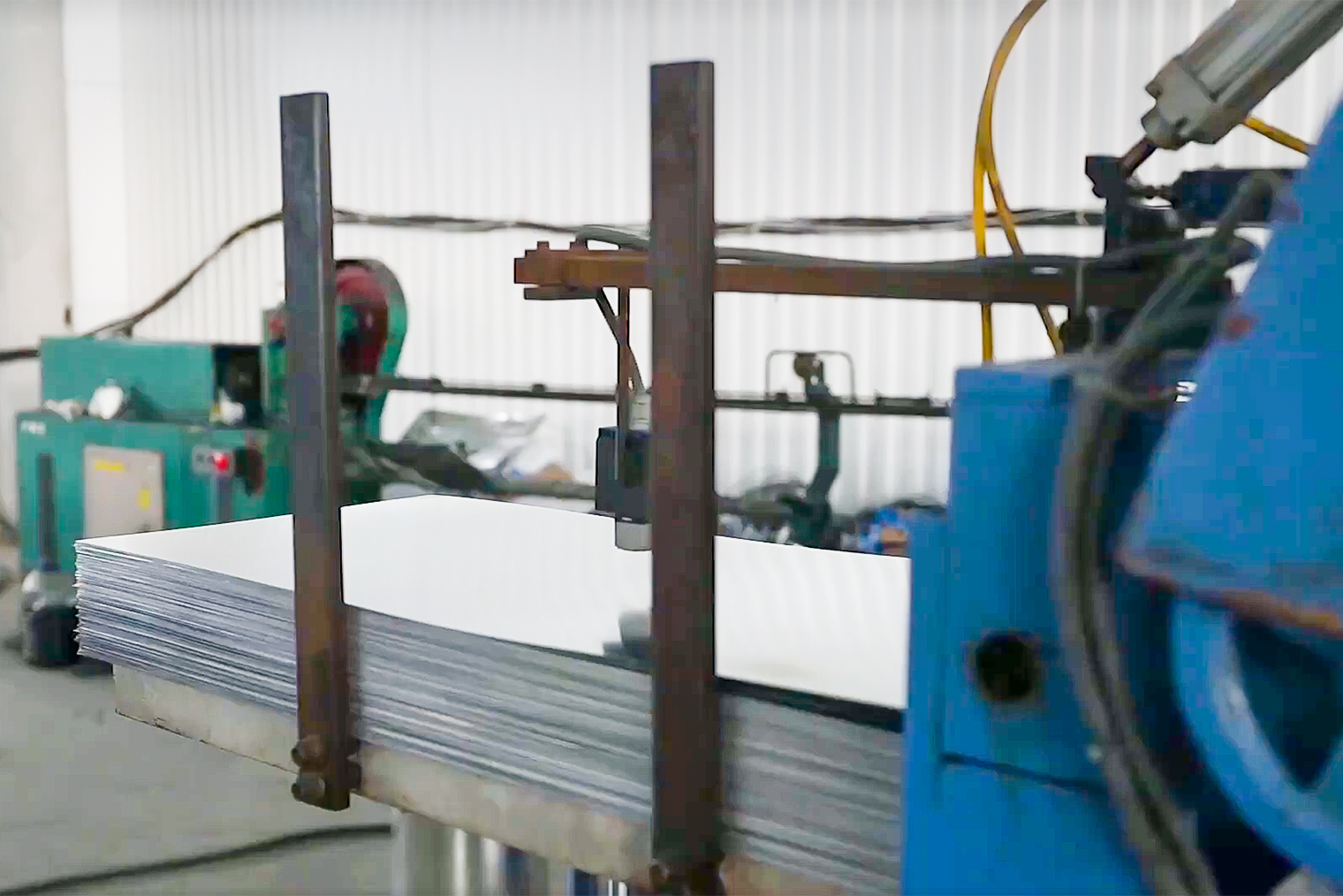
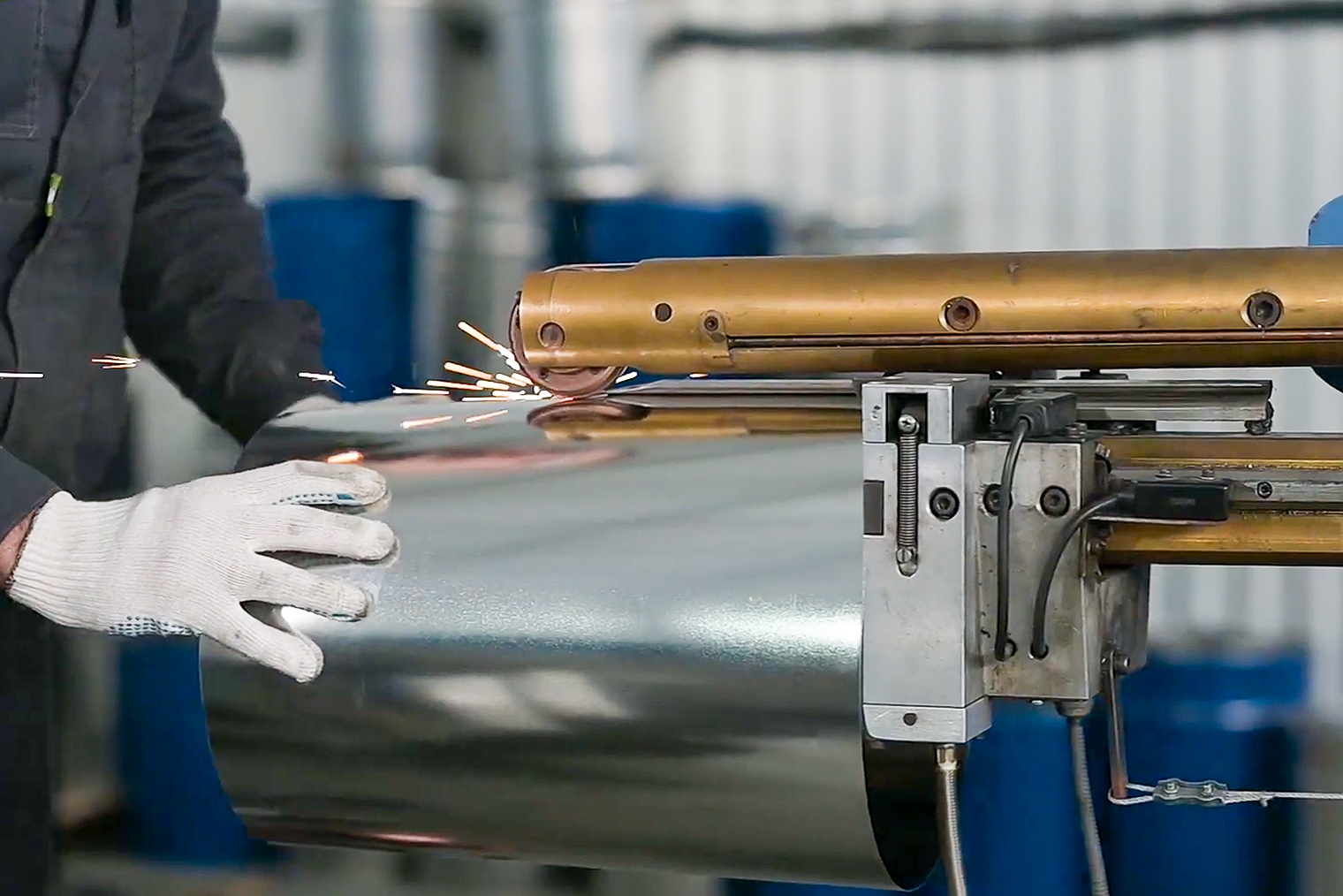
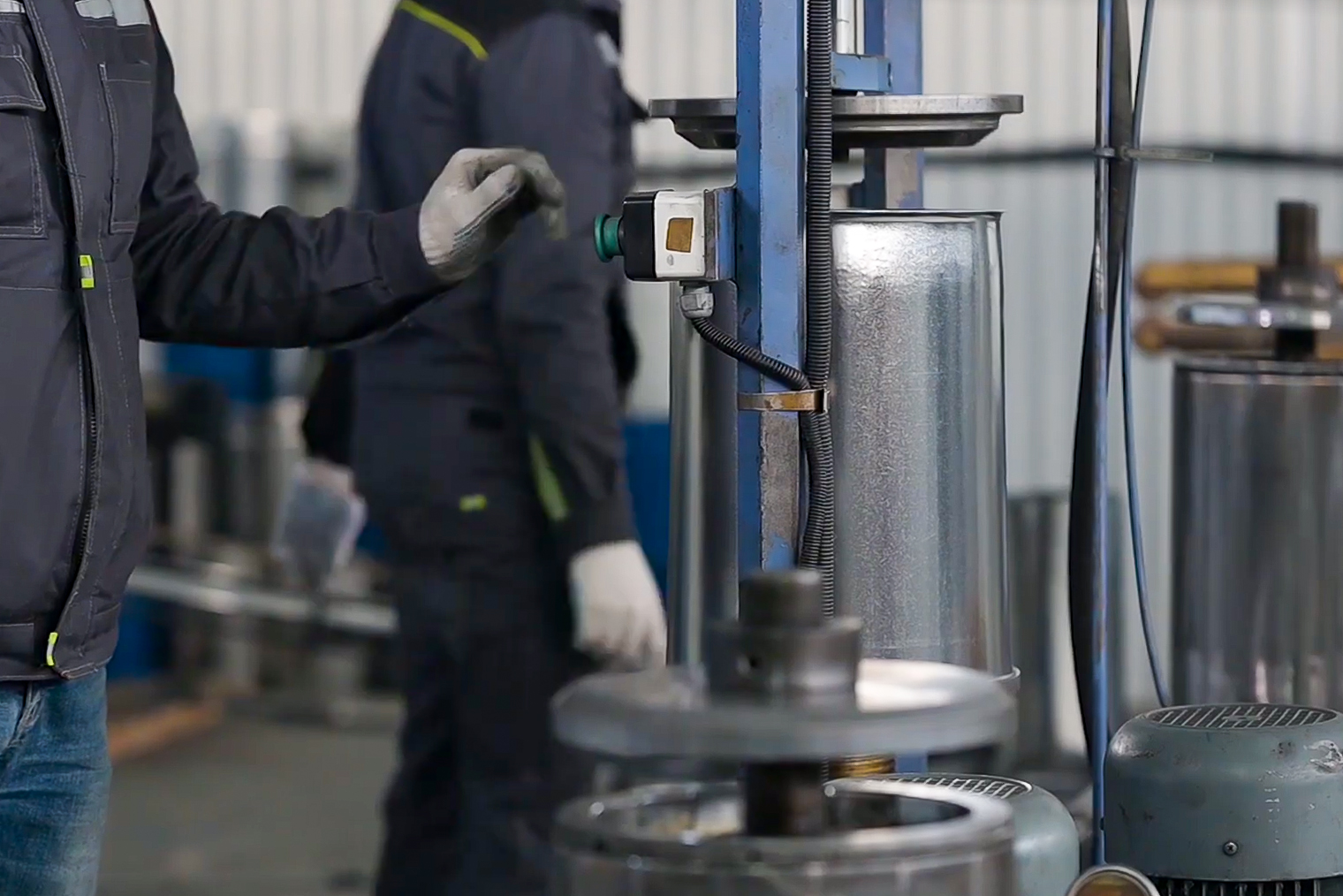
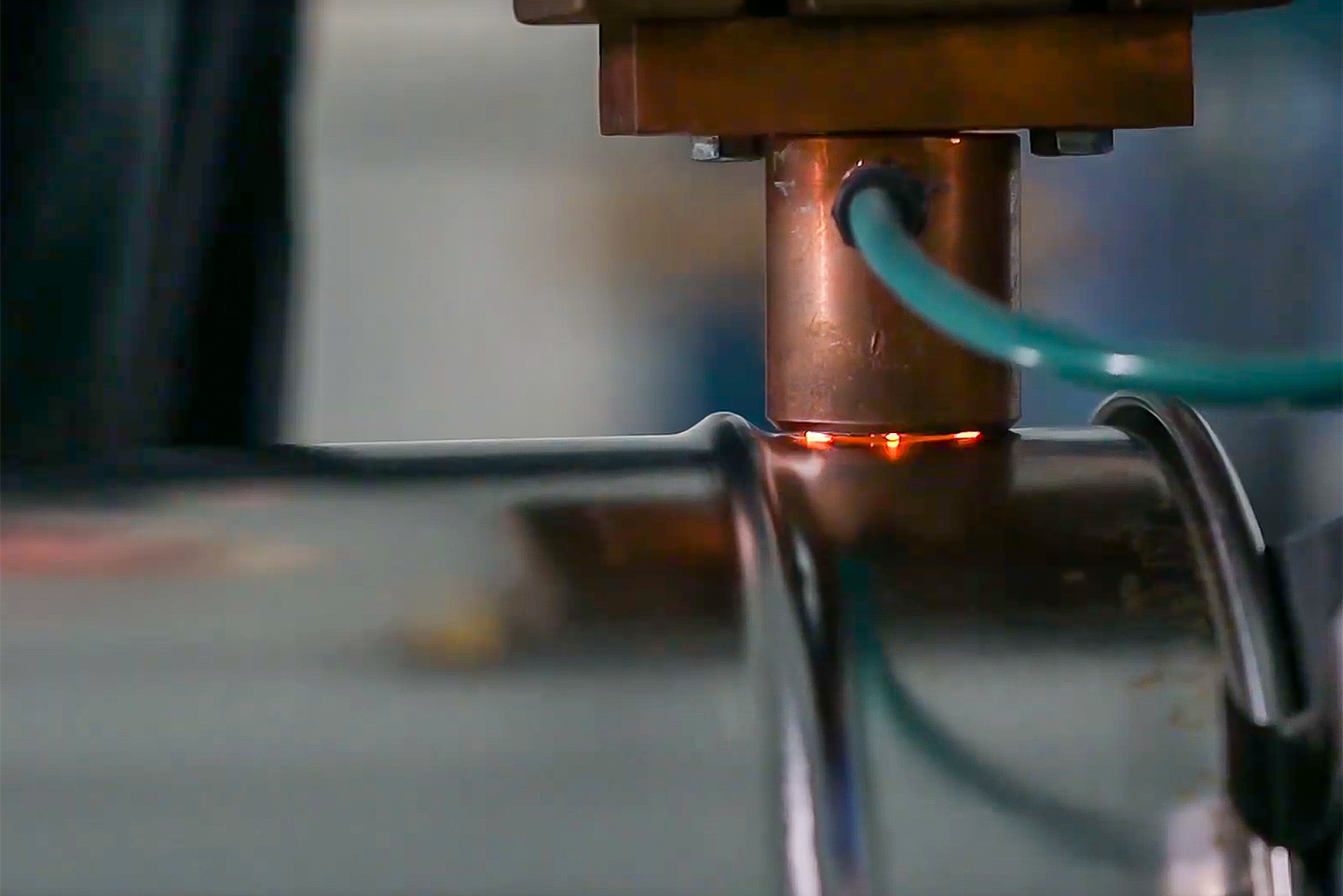
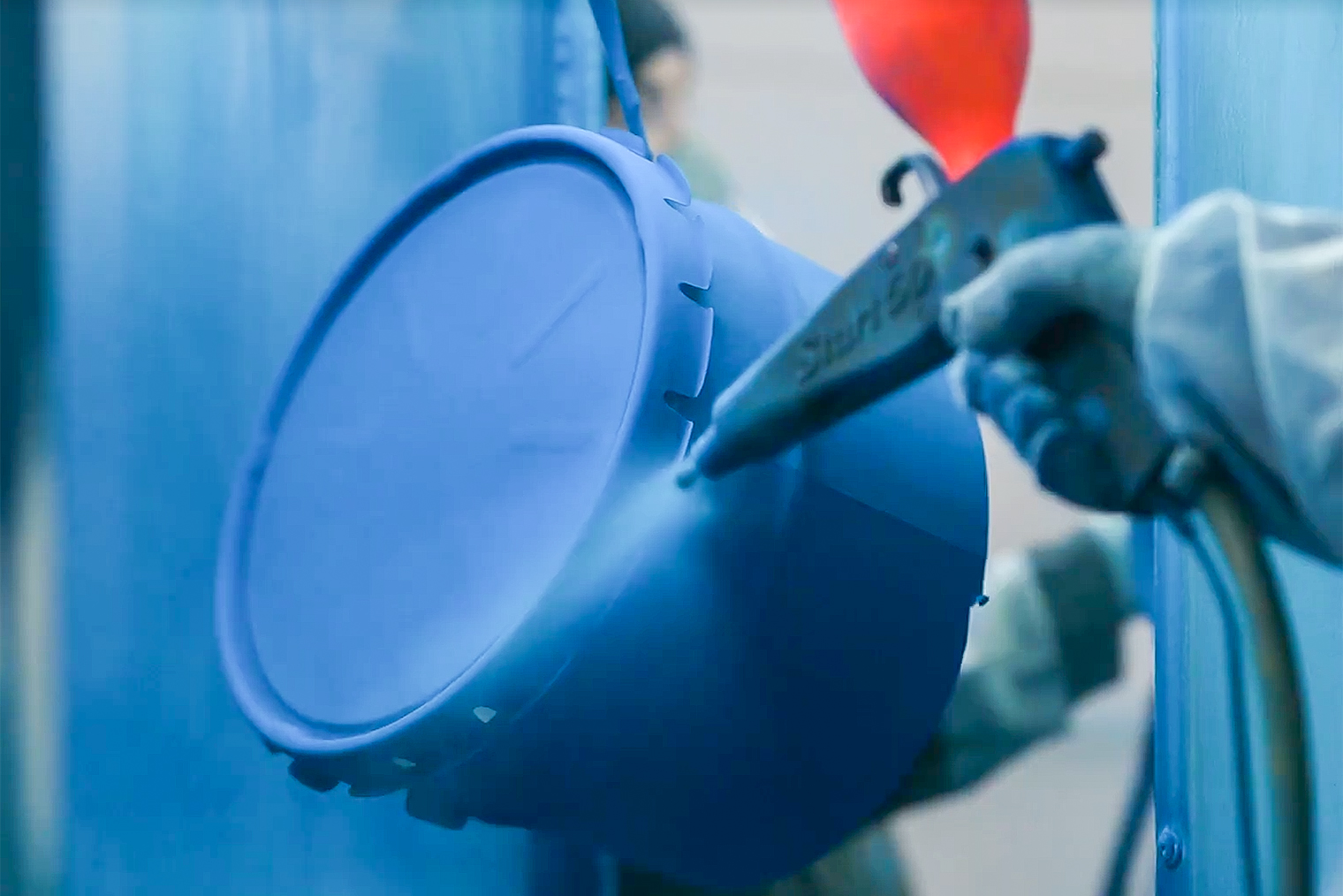
Ошибки планирования
Основным сырьем при производстве была жесть ЭЖК . Поначалу мне удавалось найти ее в наличии у частных продавцов, но позже оказалось, что вся жесть была адресная, то есть под конкретного заказчика. Не стоило рассчитывать больше чем на партию по паре тонн, а мне на выпуск 60 000 ведер по плану требовалось около 100 тонн жести.
Было два варианта закупки сырья. Первый — приобрести материал у Магнитогорского металлургического комбината, единственного производителя жести ЭЖК в России. Для этого нужно было внести 100% предоплаты за партию, кратную 60 тоннам: столько помещается в один вагон поезда.
Для моих нужд мне пришлось бы заказывать два вагона, что стоило бы мне больше 7 млн рублей. При этом ждать поставку нужно было полтора-два месяца. То есть, чтобы обеспечить себя сырьем, мне потребовалось бы внести предоплату в 15 млн рублей на два месяца вперед. Это привело бы к кассовому разрыву.
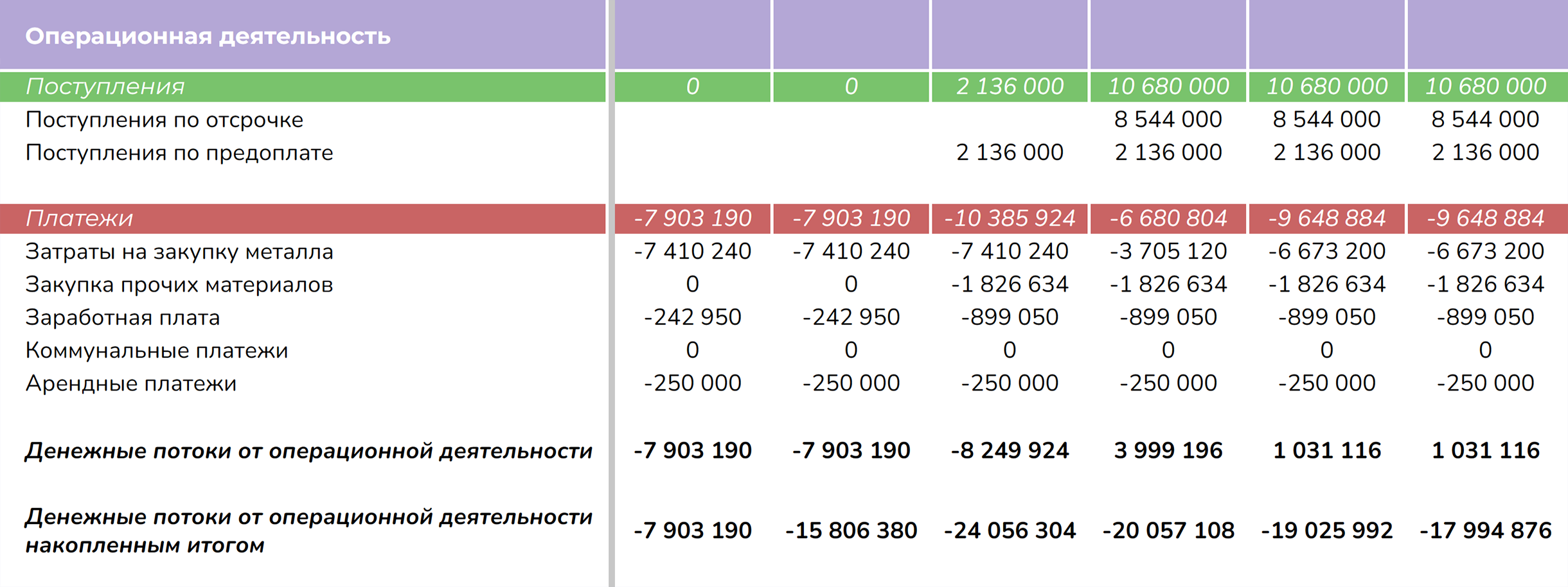
Второй вариант, который я в итоге выбрал, — закупка металла через дистрибьютора. Посредник просил предоплату в 20%, за свой счет привозил сырье с комбината себе на склад и оттуда отгружал мне жесть по факту оплаты. Стоило это немного дороже, но позволяло высвобождать средства.
С реализацией ситуация тоже оказалась непростой. Моими клиентами были производители краски, которые поставляли продукцию под реализацию — то есть с большой отсрочкой оплаты — на строительные рынки. Я думал, что, если предложить им небольшую скидку, это замотивирует их купить мой товар по предоплате. Здесь я ошибся: у производителей краски попросту не было свободных денег.
Отдельно о клиентах: часть заказчиков я нашел в интернете по запросу «лакокрасочный завод». С другими я начал сотрудничать после участия в выставке «Интерлакокраска», которая проходила в московском Экспоцентре.
Чтобы решить проблему, я начал переводить заказчиков на факторинг . Здесь тоже были нюансы: многие факторинговые фирмы финансировали отгрузки только в топ-500 компаний по России, например в «Роснефть», «Газпром», «Леруа Мерлен», «Магнит», X5 Group. У других были условия по годовому обороту покупателей, у третьих — еще какие-нибудь невыполнимые требования. Но мне все-таки удалось найти хорошую факторинговую компанию. Дополнительно я подключил овердрафт в банке и начал искать заемные средства для пополнения оборотного капитала.
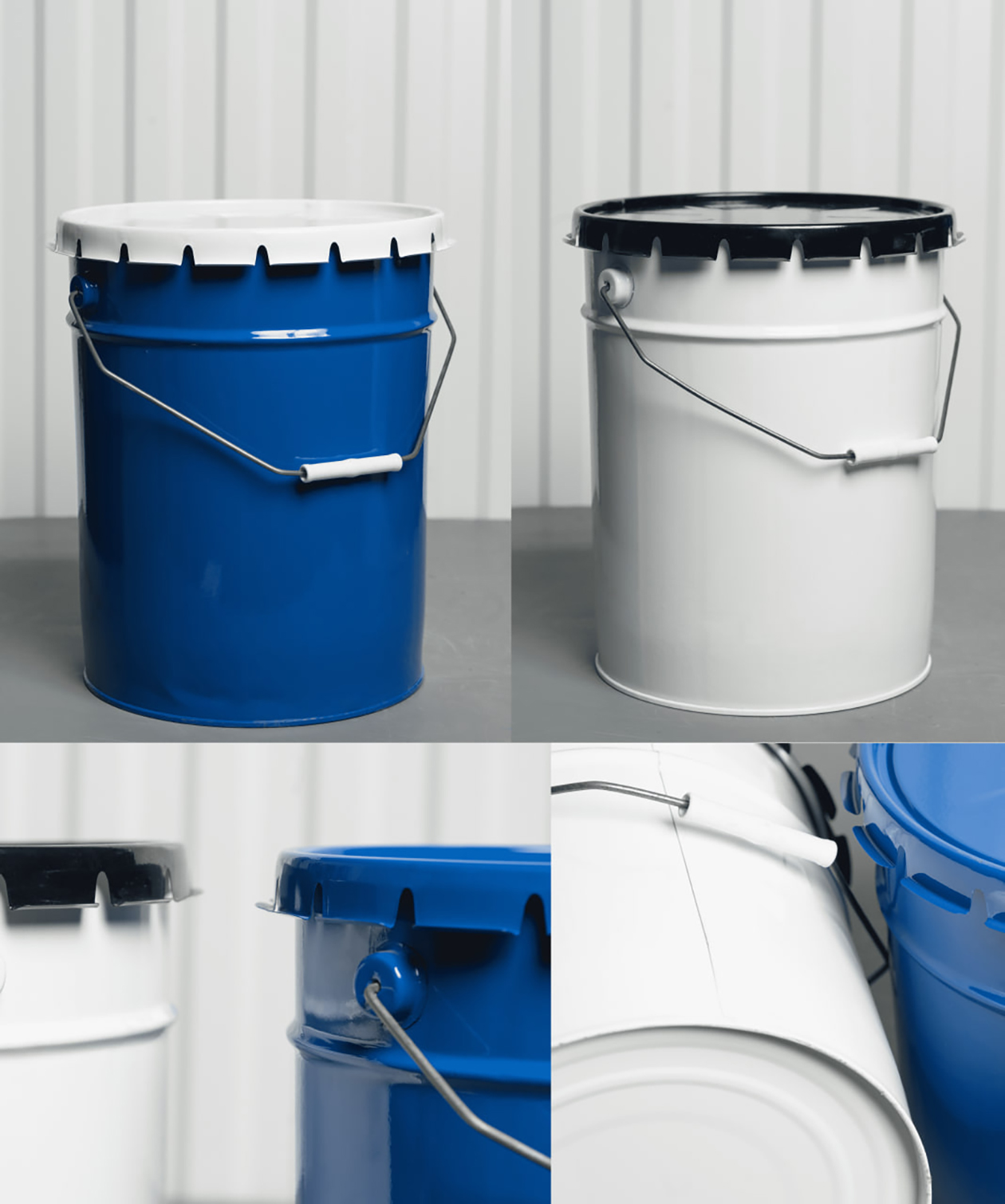
Производственные проблемы
Я установил план производства в 60 000 ведер в месяц, или 3000 за смену, но первое время мы выпускали не более тысячи в день. Я списывал это на неопытный персонал. Но сейчас я понимаю, что особых умений и не требовались, так как оборудование полуавтоматическое: работнику нужно было просто загружать заготовку в станок и нажимать кнопку.
Прошло несколько недель, выпуск уперся в 1000—1200 единиц. Проблема была связана с процессами на малярном участке, где работники с двух сторон наносили покрытие на ведра. Чтобы повысить производительность, я убрал операции, на которые маляры отвлекались, например засыпку краски в оборудование, поручив это комплектовщикам. Какие-то процессы автоматизировал.
Но тут встала другая проблема: если ускорить работу маляра, приходилось ускорять и конвейер, из-за чего ведро находилось в печи недостаточно долго — покрытие не полимеризовалось до конца и трескалось.
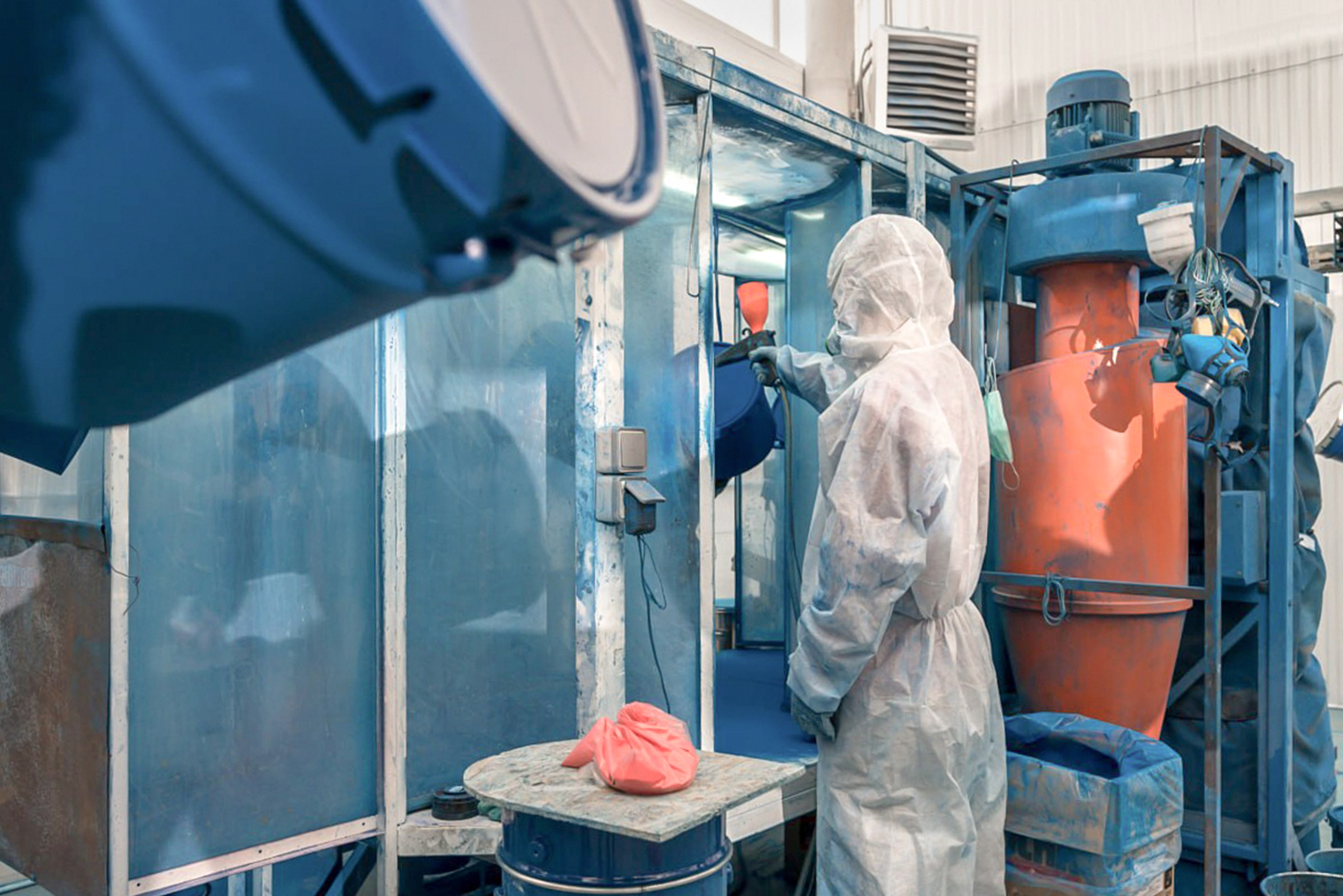
И тут я заметил еще один интересный момент: на слесарной линии был полный штат сотрудников, что давало производительность на уровне 350—400 единиц в час, тогда как малярный участок мог сделать только 100—150 штук. Таким образом, слесарный участок мог обеспечить полную загрузку малярного цеха всего за три часа работы. Люди при подобных обстоятельствах начинают работать медленнее, а руководству кажется, что все сотрудники заняты.
Сейчас я понимаю, что для решения проблемы низкой производительности нужно было перейти на металл с заранее нанесенным цветным и защитным покрытием. Подходящее оборудование было у дистрибьютора, но оно очень дорогостоящее и со своими сложностями в использовании.
По итогам пяти месяцев проекта мы получили операционный убыток около 3 млн рублей — в основном из-за затянувшихся сроков поставки адресной жести в самом начале и низкой производительности малярного цеха в период работы.
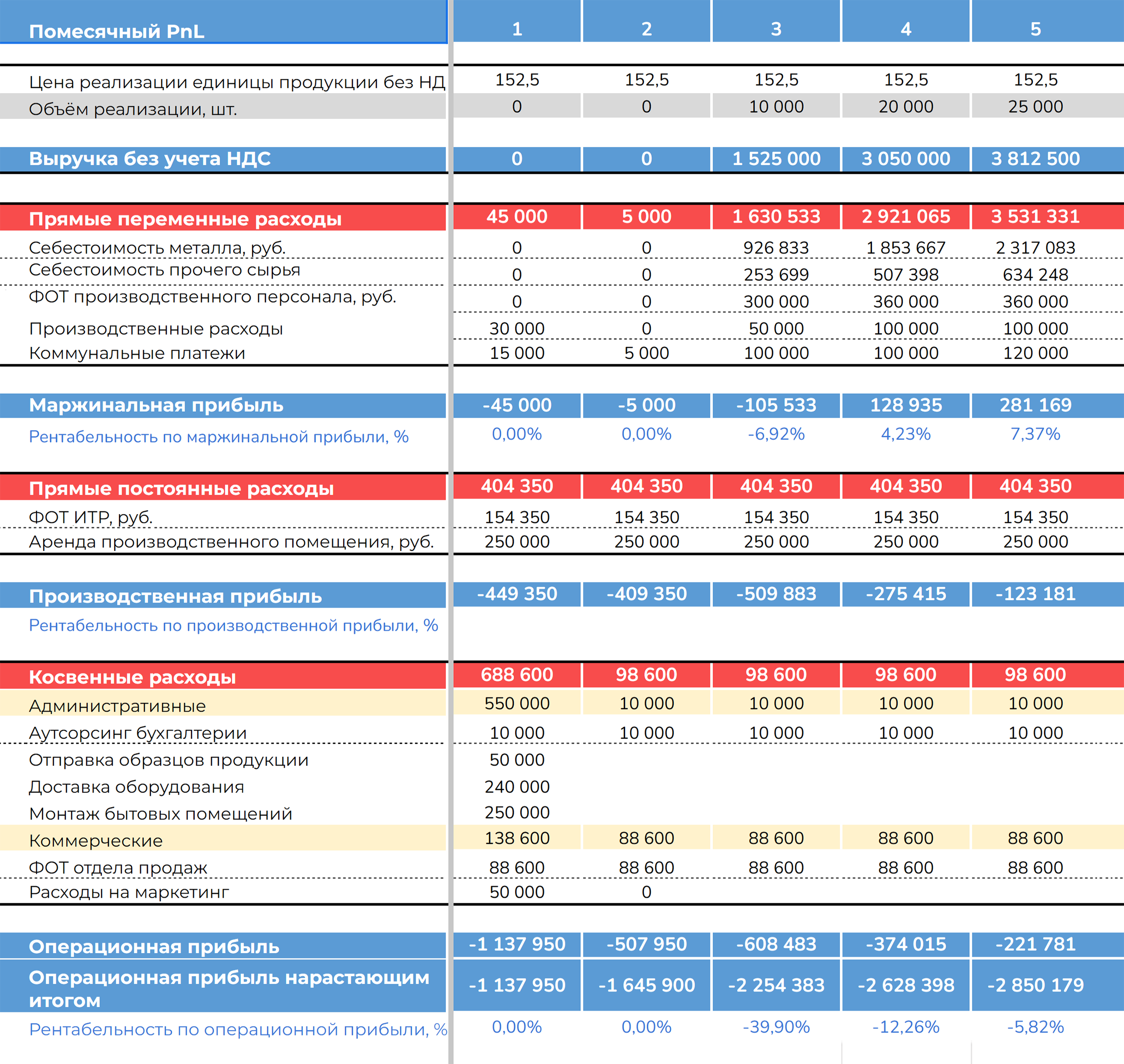
Новые препятствия
Случилась еще одна неприятность. В марте 2021 года, перед началом строительного сезона, Магнитогорский металлургический комбинат начал технологическое обслуживание своих линий по производству жести ЭЖК, а оставшиеся мощности направил на выпуск пищевой жести. С рынка на два-три месяца пропало все сырье, поэтому на это время я приостановил работу компании.
В тот момент жесть еще производили в Казахстане, но ее не поставляли в Россию. Нужное сырье было в Беларуси, но предприятие там было загружено на несколько месяцев вперед. Жесть вернулась только в августе, по цене уже более 150 000 ₽ вместо прежних 70 000 ₽.
Производство приносило убыток, оборотных средств стало не хватать, поэтому я обратился в компанию, которая занимается поиском инвесторов. За полгода они никого не нашли. Я пытался найти инвестиции через свои контакты, но тарное производство низкомаржинальное — эта специфика бизнеса отпугивала инвесторов, которые предпочитали ИТ-сферу.
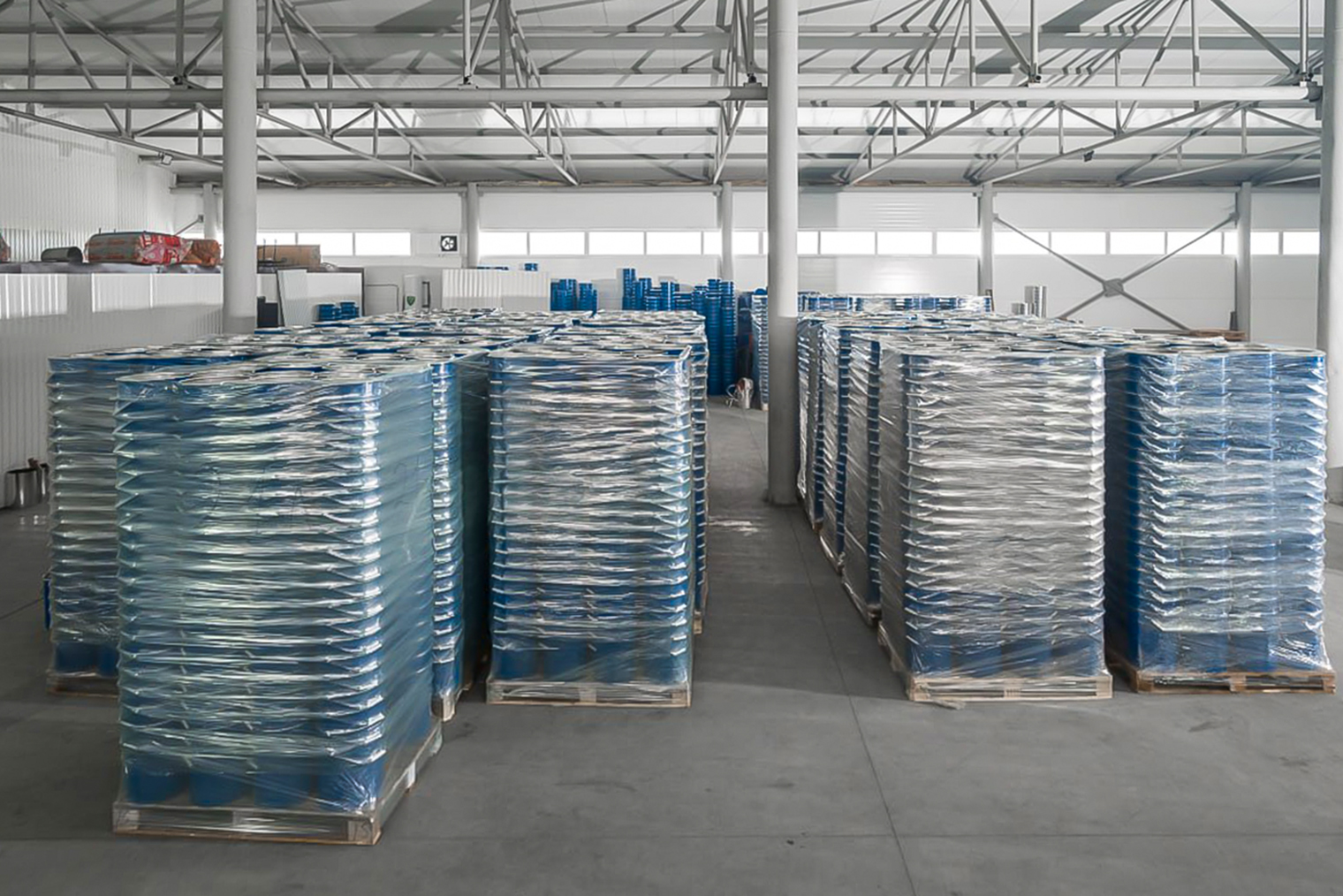
Итоги
Из-за проблем с поставками жести и отсутствия инвесторов мое производство не работало три месяца. Мне пришлось оплачивать аренду, простой сотрудников и компенсации при сокращении. Как только стало понятно, что сырье появится не раньше чем через три месяца, стоило перевезти производственные линии в небольшое помещение и законсервировать их. Если бы с рынка не исчезла жесть, возможно, мне удалось бы сохранить свой бизнес.
К концу лета 2021 года я окончательно закрыл бизнес, убытки достигли 10 млн рублей. Это решение далось мне нелегко. Я хотел откусить сразу большой кусок пирога, за что и поплатился. Но при этом я приобрел бесценный опыт, который бы не получил ни на одной работе.
Сейчас я занимаюсь консалтингом в области экономики и финансового менеджмента для небольших предприятий и помогаю другим предпринимателям избегать ошибок, которые сам когда-то совершил.